Industry News, trenchless people, trenchless products
Raven’s story began 30 years ago when it used a blue epoxy coating to protect a manhole. Throughout our history, we have continued to build this company and its products on the confidence and trust of that blue flagship product, Raven® 405. This confidence is shown in the 50-year design model, experience and commitment represented every day in our protective coatings, unmatched technical experience and customer service.
Over the course of 30 years, Raven has continued our innovative approach to solving corrosion issues while committing to producing high quality protection products. While known as an industry leader in manhole rehabilitation, Raven is more than just manholes. Therefore, we strive to solve as many corrosion problems in such additional markets as potable water, industrial, OEM and oil & gas.
Raven stands firmly behind its ‘Proven, True & Blue! Proven, True & New! ®’ slogan. With over 21 million square feet of Raven product applied to a variety of structures since 1988, Raven’s team of experts spend endless hours creating and testing products that will endure the most extreme conditions.
As Raven looks back on what has helped propel the company forward as a front runner, the development of quality products and relationships are among the most important. Raven’s success and commitment is largely attributable to the highly trained network of 70+ Certified Applicators (CA) that are dedicated to high quality standards that have come to be expected over the past 30 years.
Raven has a diverse line of products but the more renowned products are:
Raven® 405, the ‘Proven, True & Raven Blue’, is a solvent-free 100% solids, ultra-high build epoxy coating formulated with exceptionally high physical strengths and broad range chemical resistance. 405 exhibits superior bond to concrete, steel, masonry, fiberglass and other surfaces. 405’s unique ultra-high-build ability allows it to be spray applied on vertical and overhead surfaces. The surface tolerance and high physical strengths of 405 allow it to be designed as a structural lining in manholes, pipelines, tanks and other deteriorated structures.
AquataFlex® 505 & 506, are versatile novalac epoxy polyurethane hybrids that have fast cure times and flexibility of polyurethanes and increased chemical resistance of epoxies. They both are USDA Certified Biobased Products and ANSI 61 Certified.
AquataPoxy® A-6 & A-6 Thick, are solvent-free, 100% solids, corrosion resistant epoxy
coatings that can be applied to dry or damp surfaces. Formulated for broad range corrosion protection and certified safe for potable water.
As Raven continues to engineer solutions to protect infrastructures, it joined forces with
VersaFlex, Inc. on January 1, 2018, to provide a more robust portfolio of specialty coating technologies across a plethora of markets.
“We are excited to leverage each other’s strengths to continue providing the outstanding service our customers have become accustomed to over the past 30 years,” said Raven Lining Systems’ COO Rob Pawlak. “These two influential brands will pioneer a whole new era in the specialty coatings industry.”
Raven’s tag line is Protect with Confidence®! Visit their website for more information.
Industry News, trenchless people
A visit to No-Dig Live 2018 is free of charge and a must for anyone involved in the installation or refurbishment of underground utilities.
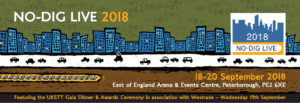
What’s on at No-Dig Live!
- Case study presentations from leading contractors
- Patrons Panel event
- Irish focus day featuring speakers from Irish Water, Northern Irish Water and Aecom
- Live indoor and outdoor demonstrations with over 120 exhibiting companies
- The UKSTT Gala Dinner & Awards Ceremony Wednesday 19th September
- Visitors from over 25 countries during the 3-day event
- Young Professional Trenchless Challenge
Learn more and register online here!
Industry News, trenchless projects
The City and County of Denver has designed the 33rd Street Outfall Storm Sewer to reduce flooding concerns between Downing Street and the Platte River along 33rd Street and the surrounding neighborhoods. The project is being released in four phases over three years, and BTrenchless has completed the first two phases, installing the storm sewer from the Platte River to the intersection of 33rd and Blake.
The pipeline is a combination of large box culverts, 120” HOBAS pipe, smaller reinforced concrete pipe, and steel casings. The highlight of the first phase was construction of a precast 11’ x 8’ concrete box culvert across Brighton Blvd. while maintaining a constant flow of traffic. The second phase included a 220’ long tunnel, ten foot in diameter, under the Union Pacific Railroad Yard and the RTD Commuter Rail. It also included side-by-side 96” diameter steel tunnels under Blake Street and a 450 foot long, 51” HOBAS storm lateral via a microtunnel method.
The diversity of this project allowed BTrenchless to utilize three different types of tunnels and capitalized on the vast resources of both people and equipment to successfully complete this complex and high profile project. In the course of the first two phases, nine different crews and four different superintendents had a part in the overall success of the project, each capitalizing on their various areas of expertise.
Click on photos to view larger images. Be sure to notice Morty the Tunnel Rat in the top photo supervising the project!
Industry News, trenchless projects
Massive Metro Project Will Improve Traffic and Rail Congestion in One of India’s Largest Cities
On June 11, 2018, a Robbins Crossover XRE destined for Line 3 of India’s Mumbai Metro arrived in Mumbai port following a successful factory acceptance test in April. The machine, combining features of a hard rock Single Shield TBM and an Earth Pressure Balance Machine, is one of two 6.65 m (21.8 ft) Crossover machines that will bore under contract UGC-01. Operation of these two machines will be carried out by Larsen & Toubro, part of the Larsen & Toubro -Shanghai Tunnel Engineering Co Joint Venture (L&T-STEC JV). The Robbins Company will provide key personnel for the initial boring phase. “During the factory acceptance testing, we observed that the machine and back-up system are robust enough for hard rock tunneling,” stated Palwinder Singh, Head of Tunnel Operations for L&T-STEC JV.
During the bores, consisting of parallel 2.8 km (1.7 mi long) tunnels, geologic conditions will include mixed ground and possible water pressures up to 2 bar. According to Singh, “A Crossover XRE was chosen because of the expected geology,” which includes basalt rock and transition zones consisting of black carbonaceous shale, tuff, and breccia. Rock strengths are anticipated to range between 15 MPa and 125 MPa (2,200 and 18,100 psi) UCS. The machines will bore with only 15 to 20 m (50 to 70 ft) of cover above the tunnel and the structure will be lined with reinforced concrete segments in a 5+1 arrangement.
The metro tunnels will run between the Cuffe Parade Station and Hutatma Chowk station, passing through the Vidhan Bhavan and Church Stations. Both Crossover machines will be launched from the same 25 m (82 ft) deep by 22 m (72 ft) long shaft at the Cuffe Parade Station. “The limited length of the shaft requires running the TBMs for the first 100 m (328 ft) with some or all the back-up decks at the surface,” said JP Bayart, Robbins Project Engineer. “The TBMs and back-up systems are connected with umbilical cables and hoses.”
The TBMs will begin their excavation in hard rock mode. “Each cutterhead is optimized for operation in rock, as this is what is expected. The machines can also operate in soft ground thanks to the screw conveyor with bulkhead gate and discharge gate,” said Bayart. “The Robbins Torque-Shift System, consisting of two-speed shifting gearboxes coupled to the main drive motors, allows for the high cutterhead torque required for soft ground operation.” The face of each machine is equipped with six muck buckets and six large internal muck loading plates. This design, in combination with the screw conveyor located at the centerline of each machine, will allow for the option of fully emptying the cutterhead chamber, resulting in minimal wear when EPB mode is not required. Muck will be removed from the tunnels via muck cars.
Assembly and launch preparations for the first XRE TBM began on 20 June and are estimated to take about six weeks. The second Robbins XRE TBM underwent factory acceptance testing at the end of May and will arrive at the jobsite at the end of July for its assembly. “Our target is to achieve an average of 250 m (820 ft) of boring per month,” said Jim Clark, Robbins Projects Manager India. “The target to complete the boring operations is 20 months, which includes the additional time required for the short start-up using umbilicals on the initial drives, dragging the machines and re-launching through three stations.” Contractor L&T plans to work crews on double shifts to cover a full day of operations in order to keep to this timeline. The machines will join two Robbins Slurry machines boring a separate contract of the Mumbai Metro Line 3. The first of those machines will be launching in August 2018. The Metro Line 3 project as a whole is estimated to be completed by 2021.
Image: Robbins and contractor personnel stand proudly in front of the first of two Robbins 6.65 m (21.8 ft) diameter XRE TBMs during the factory acceptance test.
Industry News, trenchless people
The Australasian Society for Trenchless Technology (ASTT) is offering the Cured-in-Place Pipe (CIPP) Good Practices Course in Hamilton, New Zealand prior to the start of the Water New Zealand Conference and Expo.
The course will be presented by expert in field, Chris Macey of AECOM in North America, and provides an in-depth overview of wastewater mainline and lateral pipe rehabilitation using CIPP and design to job completion.
Tuesday, September 18
8am – 5pm
Novotel Hamilton Tainui
7 Alma St
Hamilton, 3204
New Zealand
Course registration is NZ$530 for ASTT members and NZ$640 for non-members. (Please note, registration will be charged in AUD).
Visit the conference website for more details!