Blog, Industry News, trenchless people, trenchless products, trenchless projects
Highly Anticipated Photo Finish wraps up Tunneling at Massive Metro
On September 28, 2016, Bangalore’s last TBM for the city’s metro rail project broke through, marking the end of
TBM tunneling on the Namma Metro phase 1. The Robbins-operated machine, known as “Krishna”, bored a 750 m (2,460 ft) drive through challenging conditions between Chickpet and Majestic stations. Cleanup and final commissioning of the tunnel will be completed in 2017, and is the last obstacle before owner Bangalore Metro Rail Corporation Ltd. (BMRCL) can open the Malleswaram-Majestic link. The TBM’s sister machine, “Kaveri”, completed a parallel tunnel in June 2016.
The success follows a gauntlet of challenges on the two tunnel sites. Due to severe delays on the original tunnel drives, Robbins was approached and asked to take over the operations of the remaining two competitor-manufactured TBMs in February 2015. After obtaining agreement from the project owner and the contractor, Robbins took over the responsibility for all aspects of the underground operations. “We provided a team of over 60 staff including TBM operators, TBM technicians, ring builders, a grouting team, and more. We were also responsible for running surface installations and equipment such as the grout batching plant, gantry cranes and power supply. Contractor Coastal Projects Ltd. (CPL) provided a team of people including surveyors, QC engineers, and loco operators who reported directly to our site management team,” explained Jim Clark, Projects Manager for Robbins India. 
The Robbins crew carried out tunneling operations while the Chickpet station was being constructed around them to mitigate delays incurred before they took over project operations. The project’s most difficult challenges included a low overburden and unconsolidated ground along the alignment, and the discovery of several uncharted wells directly on the alignment. Difficult ground frequently prevented proper pressurization during cutting tool replacement, requiring a grout solution to be pumped in to fill voids and left to cure. Initially the curing process took up to 36 hours, but with improved application methods this was reduced to a 12-hour curing time.
Another challenge involved the sensitive building structures along the tunnel path. Issues with surface vibration, explained Clark, required that cutterhead speed be limited to 1.8 RPM during the day shift and 1.2 RPM during the night shift. Despite the obstacles, the TBMs advanced at rates of up to 50mm (2 in)/min in highly weathered rock.
“This is an industry first, wherein a TBM manufacturer has utilized their in-house expertise and knowledge to take on this level of responsibility for a project,” said Clark, addressing the magnitude of the successful breakthroughs. “The fact that it was ‘a first’ and we were successful in bringing this high-profile project back on track is a great achievement for The Robbins Company.”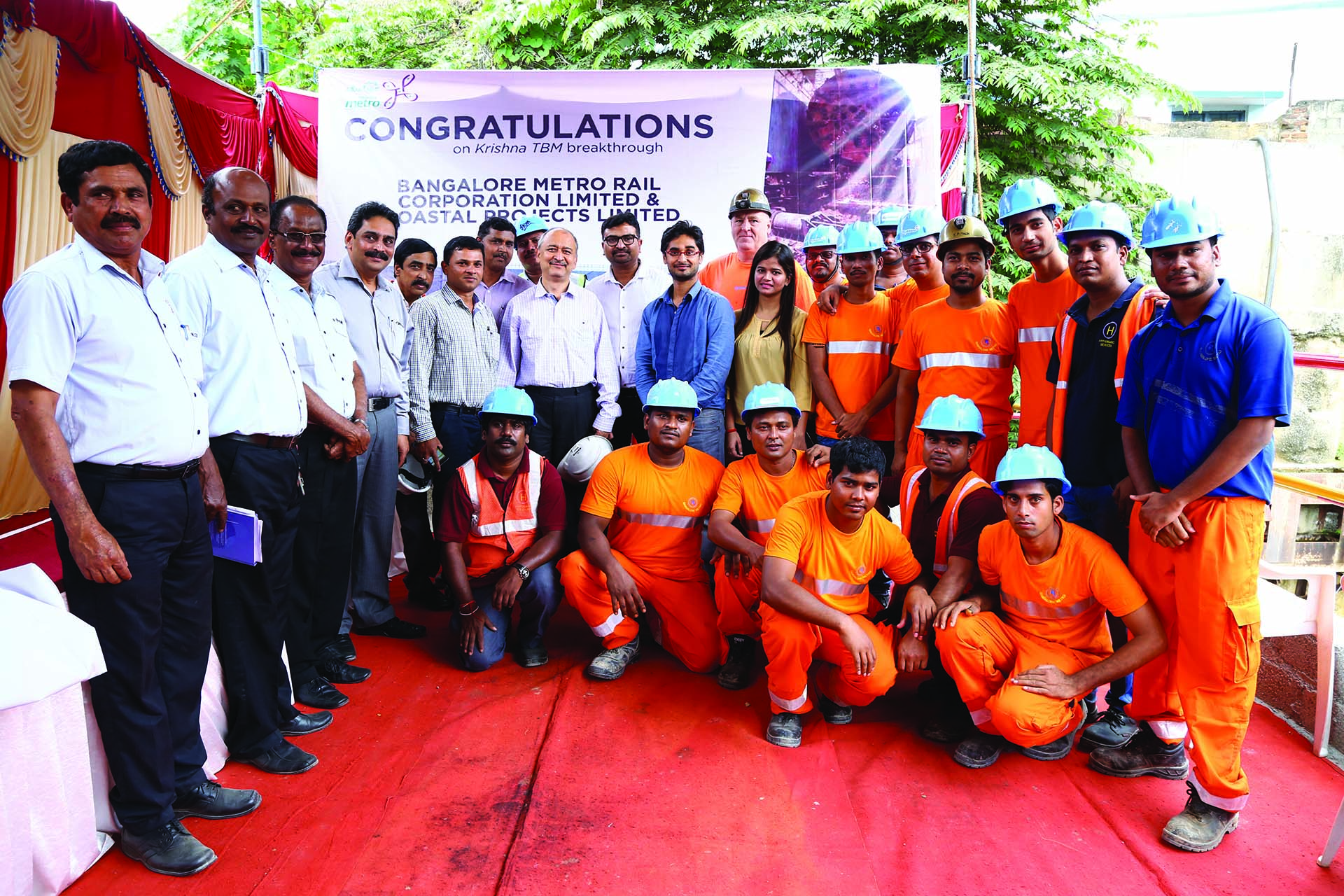
Now that tunneling is complete, the North and South runs of the Namma metro will be connected–a line that, once in service, will carry an estimated 40,000 passengers daily. It is anticipated that Phase One of the metro will be opened in its entirety in 2017.
Blog, Industry News, trenchless projects
Real time information on asphalt density and uniformity is a boon to construction quality efforts
By Roger Roberts, GSSI
Properly compacted asphalt is a major factor in the lifespan of roads, since inadequately compacted asphalt deteriorates at a more rapid rate than properly compacted material. With the billions spent on road construction and repairs each year, it has become a matter of urgency to find new technologies that can ensure the integrity of asphalt on newly paved roads. New radio wave technology is now available to nondestructively determine asphalt density during application.
Asphalt installation and compaction basics
The air void content within asphalt varies based on the amount of compaction during asphalt emplacement and variations in the asphalt mix composition. Asphalt with too many air voids (often considered to be more than 8 percent) deteriorates at a more rapid rate. Too few air voids (less than 3 percent) results from over-compacted asphalt, which is also undesirable. In either case, the asphalt is subject to early failure and the road’s lifetime is less than asphalt that contains the optimal air void content.
Construction engineers are looking for that “sweet spot” where the compaction of the asphalt when it is laid down is optimal. They typically assess asphalt by measuring density variations, which can be used to calculate the air void content.
To ensure optimal compaction, asphalt should be kept at a specific temperature range as it is being laid down. If the paving machine and transfer vehicles do not do a good job keeping the material uniformly hot, there can be “cold patch” areas. When the roller rolls over areas not within the optimal temperature range, it cannot properly compact the material. For example, such cold patches may occur if the asphalt paver is refilled from end-dump trucks, which cool the asphalt more near the metal sides and end of the truck than in the middle. Some poorly-paved roads have regularly spaced defects associated with end-dump truck refills.
One may not be able to notice these areas at first, but they may become obvious later. In fact, there are many roads where one can observe a cold patch every several hundred feet that is starting to deteriorate – turning into a raveled section in the road. If the work crew does not catch the problem during paving, the road may need to be repaved far sooner than if the material was properly applied.
Another compaction issue occurs when the established “rolling pattern” is not properly followed. The rolling pattern refers to the number of times, speed, and lap pattern rollers should employ when rolling new asphalt to achieve the optimum compaction. If the paving crew misses a section and does not compact the material with the proper number of rolls, they can create areas where compaction is faulty.
Discovering and correcting any rolling pattern issues during the first few days of a paving job benefits both the owner and contractor, since contract specifications may include requirements on how asphalt is laid down in terms of acceptable void content. Contracts may also include a bonus for getting to the specific asphalt void content range – or a penalty if the crew goes outside the specified void content range.
Options for measuring asphalt density and void content
There are several available methods that can be used to measure asphalt density variations, which are then used to calculate void content variation. One non-destructive testing (NDT) method is the nuclear density gauge, which consists of a radiation source that emits a cloud of particles and a sensor that counts the received particles that are scattered back by the test material. By calculating the percentage of particles that return to the sensor, the gauge can be calibrated to measure the density and inner structure of the test material. [1]
While quite accurate, the nuclear gauge has several disadvantages. The gauge is placed on asphalt and measurements are taken over a specific period of time, usually a few minutes or less. The method requires contact, with the device required to remain stationary at the measurement point. Due to the length of time required for the measurement, nuclear gauge measurements are taken sparsely, on the order of a few measurements per 100 lane feet. Collection of only these “spot” measurements does not adequately capture all the asphalt’s variability. Also, because it uses radioactive material, the nuclear gauge requires user training and secure storage. There are also special transportation requirements. Re-licensing, maintenance, and recalibration fees run about $2000 per year.
Similar to a nuclear gauge, the non-nuclear density gauge measures electrical impedance; a calibration procedure is then performed to correlate it to density [2]. Like the nuclear density gauge, the method is quite limited, because it samples only very small portions of the asphalt.
Because the nuclear and non-nuclear density gauges may collect only one value over a large area, they are unable to catch all the variations in void content that may be important to ensuring a quality paving job.
Another NDT option is the use of radio waves, which can be used to obtain real time measurements over a large swath of pavement in short periods of time. Radio wave reflections from the asphalt can be used to directly calculate the asphalt dielectric values, which are then correlated with the new pavement’s void content, a relative indication of density.
One other method that should be mentioned is “coring,” a destructive method in which one physically extracts a core from the asphalt and measures its properties. Coring is used as a primary asphalt compaction evaluation method and is always used to “ground truth” measurements from other methods. Coring is done on a very limited basis, so it often under-represents the true variability in asphalt void content.
New radio wave technology used to help improve asphalt mixture quality
The initial relationship between void content and road condition has been known for a long time. In the late 1990s, researchers at the Texas Transportation Institute (TTI) discovered the relationship between the dielectric calculated by ground penetrating radar (GPR), an application-specific use of radio waves, and void content.
Researchers later developed a working methodology for use of infrared and radio wave technologies for improving the assessment of asphalt mixture and compaction quality. They then looked for a way to commercialize it so it could be easily used by state departments of transportation.
Previously, use of the GPR technique required specialized equipment, a great deal of data interpretation, and a number of manual steps. In 2013, TTI began working with GSSI to package the device components into a streamlined and operator-friendly device that would provide real time profiling of asphalt mixture uniformity. The work was done as part of the Federal Highway Administration’s Strategic Highway Research Program (SHRP 2). [3]
Over the next few years, GSSI developed the technology into the PaveScan RDM, which TTI used in several pilot studies. The non-contact PaveScan technology uses a sensor that typically outputs a measurement each half-foot along the lane traveled, so a mile’s worth of data includes roughly 10,000 measurements for each sensor used.
TTI found that the new PaveScan system overcomes hardware, data processing, and staff expertise hurdles that existed in the past. According to TTI, “The utility of GPR was realized on all pilot projects, where the radar results provided quantitative assessment of density and uniformity.”[3]
GSSI later developed a three-channel system that can be vehicle-mounted to obtain moving void content measurements in one pass, covering both wheel paths and between the wheel paths. One sensor is located in one wheel path, one in the middle and one in the other wheel path – so three measurements are output for each half-foot along the lane traveled. In this way, a mile’s worth of data includes roughly 30,000 measurements – all collected in a mere 20 minutes.
The PaveScan RDM system has a number of benefits. First of all, it is a way of ensuring asphalt integrity of newly paved roads. Now, when a contractor lays down a new road, the asphalt void content over the entire area paved is accurately calculated, so both contractors and the owner of the road are satisfied. Secondly, the system is easy to use, bringing down the level of expertise needed to a manageable level. Thirdly, it is a very rapid method, adaptable to being put on a vehicle. The safety benefits of not having someone standing in a lane next to moving traffic are huge.
Previously, the prototype PaveScan unit developed by GSSI was used in the evaluations done as part of the SHRP 2 project. This year, GSSI delivered a production 3-channel unit to TTI, which is being used to further its research. Additional production units have been purchased with SHRP 2 funding by the Minnesota Department of Transportation, the Maine Department of Transportation, and the Nebraska Department of Transportation. By June 2016, there will be four units in the field, working to ensure that tax dollars allocated for road construction are being used wisely.
References
[1] Nuclear density gauge, https://en.wikipedia.org/wiki/Nuclear_density_gauge#cite_ref-Radioisotope_Gauges_for_Industrial_1-0, retrieved 4/26/16.
[2] Non-Nuclear Methods for HMA Density Measurements, MBTC 2075 Final Report, Williams, Stacey, G., 2008, http://arkansastrc.com/MBTC%20REPORTS/MBTC%202075.pdf
[3] Pre-Implementation of Infrared and Ground-Penetrating Radar Technologies for Improving Asphalt Mixture Quality, Strategic Highway Research Program, Transportation Research Board of the National Academies, Stephen Sebesta and Tom Scullion, Texas A&M Transportation Institute, The Texas A&M University System, College Station, Texas, © 2014 National Academy of Sciences. All rights reserved.
Blog, Industry News
Geotechnics for Trenchless Construction
November 1-3, 2016 (November 4 half day field demonstrations)
Colorado School of Mines, Golden, CO USA
This course provides an in-depth, comprehensive review of geotechnical engineering and design required for successful trenchless construction projects.
The course will focus on the following topics: trenchless technology and microtunneling fundamentals; soil characterization for trenchless methods; rock characterization for trenchless methods; groundwater conditions; ground settlement and heave; problematic ground conditions and improvement techniques; and geotechnical data and baseline reports.
Activities will include: soil and rock characterization and behavior; soil conditioning and slurry; rock cutting; and abrasivity and wear. Please visit the web site for further details.
Blog, Industry News, trenchless people, trenchless projects
Want to see something cool? Watch this time lapse video of a Tunnel Boring Machine (TBM) launch for the Michigan Ditch Tunnel Project in the City of Fort Collins, Colorado, put together by Lithos Engineering.
https://youtu.be/RAiZYRgbyo0
Project information:
Owner – City of Fort Collins Utilities
Prime Engineer – Stantec
Tunnel Engineer & Construction Management – Lithos Engineering
Tunnel Contractor – BT Construction
Site Work Contractor – Hydro Construction
Survey – Acklam
TBM – Akkerman
Blog, Industry News, trenchless products
October 6, 2016 – LAKE MILLS, Wisc. – HammerHead Trenchless Equipment, a Charles Machine Works
company, has introduced the powerful, new HammerHead HydroGuide® HG1200 winch optimally designed to be more efficient and easy to use in pipe-bursting, slip-lining or slitting applications. This new iteration of the popular HydroGuide line of winches features a patented, self-deploying hydraulic downrigger, improved performance and additional safety features.
While other winches on the market require manual assembly of heavy, bulky components, the HG1200 makes setup easy with its industry-changing hydraulic downrigger. With the touch of a button, users are able to automatically deploy the boom down hole and can fine-tune the depth up to 18 feet without having to jack up the machine. With the hydraulic boom, setup and teardown take just minutes, which saves valuable time on a job site.
A key feature of the new HG1200 winch is its precision controls. Not only can users adjust the boom to any depth, but they also have total control of the line speed and pressure. Pull force can be set anywhere between 0.5 to 12 tons, and the line speed can be set anywhere between 0 to 111 feet per minute.
“We know job conditions and specifications can vary greatly so we created a machine that can be infinitely adjusted within its parameters to fit each individual job exactly,” said Josh Hood, HammerHead product line manager. “This level of control is critical to the success of gasline slitting applications, which was a driving factor in the improvements we made from the previous version. We worked to create a winch with the necessary power and agility for a wide range of situations to ensure customer success.”
The HG1200 winch is powered by the Kubota D1105, a vertical, water-cooled, four-cycle diesel engine that complies with Tier 4 emission regulations. This lightweight, dependable engine increases the unit’s performance and fuel efficiency. The radial piston motor provides a smoother, more consistent pull.
The HG1200 has several configuration options available from the factory to meet specific customer needs:
- Optional Tracks – The optional track-mounted HG1200AT reaches difficult areas on your job site that the standard, wheel-mounted units cannot.
- Electrical Strike Identification system (ESID) – The optional ESID system is designed to provide additional safety on the job site when working near adjacent underground utilities.
- Hydraulic levelling jacks – The hydraulic option allows users to easily adjust downhole access, improving project efficiency.
The HammerHead HydroGuide HG1200 winch is available directly from HammerHead Trenchless Equipment or from authorized dealers worldwide. Authorized dealers can be found on the web at www.hammerheadtrenchless.com or by calling 800.331.6653. (International: + [1] 920.648.4848).
Photo 1: New HammerHead HydroGuide HG1200 winch.
Photo 2: Optional track-mounted HG1200AT.
Blog, Industry News, trenchless products
Electro Scan Inc. has completed data integration between its flagship sewer condition assessment solution and the
Innovyze® InfoMaster for Sewer product.
Electro Scan’s breakthrough technology evaluates 360-degrees of a pipe wall to accurately locate and measure defects in gallons per minute (GPM) or liters per second (l/s).
Recent studies indicate that 70-100% of defects are typically not found by legacy inspection techniques, such as closed-circuit television (CCTV) inspection, smoke testing, dye flood testing, laser profiling, and acoustic sensors.
Recommended to assess and certify pre- and post-rehabilitated pipes, a new chapter was recently added on Electro Scanning Inspection to the industry’s leading training manual, Operation and Maintenance of Wastewater Collection Systems, Seventh Edition, Volume One (2015), in accordance with ASTM F2550.
“We are delighted to integrate our game-changing pipe condition assessment solution with the leading business analytics solution for the wastewater industry,” states Chuck Hansen, Founder and CEO, Electro Scan Inc.
“The Innovyze® family of smart network modeling and asset management solutions continues to be the standard platform for existing and emerging diagnostic tools,” said Paul F. Boulos, Ph.D., BCEEM, Hon.D.WRE, Dist.D.NE, Dist.M.ASCE, NAE, President, COO and Chief Innovation Officer of Innovyze.
“We look forward to offering this new layer of condition assessment data to help our clients in their sewer rehabilitation decisions,” continues Boulos.
Electro Scan’s Critical Sewers® cloud application allows for up-to-the-minute monitoring of sewer evaluations, lining projects, point repairs, and new construction projects, while crews are still in the field.
Clients can easily identify pipe-specific problems before rehabilitation project acceptance.
Wirelessly transmitted to the Company’s award winning cloud application, defect flows are reported in minutes and incorporated into Innovyze® InfoMaster for Sewer product for display and analysis.
Since Electro Scan’s advanced low voltage conductivity technology does not rely on operator interpretation, third-party data analysis, or independent judgment, a key advantage is its ability to automatically provide specific location, size, and estimated flow for each defect and total pipe.
Customers wishing to utilize Electro Scan’s decision support data must be licensed users of Innovyze® InfoMaster for Sewer and Electro Scan’s Critical Sewers® cloud application, including associated integration module.
Once data is accessible, Electro Scan defect flows may be highlighted by location and severity by Innovyze® InfoMaster for Sewer, including the identification of defective joints, cracks, and leaking service connections, compared to CCTV inspection results.
Electro Scan and Innovyze® users can show pipe defects ranked by highest GPM and gallons per day per inch diameter mile (GPD/IDM), utilizing Innovyze’s 1D and 2D modeling and mapping features within Innovyze® InfoMaster for Sewer product.
Plans include the integration of Electro Scan’s 4-in-1 water leak detection probe with Innovyze® InfoMaster for Water to assess pressurized water mains.
About Innovyze
Headquartered in Broomfield, Colorado, Innovyze® is a leading global provider of wet infrastructure business analytics software solutions designed to meet the technological needs of water/wastewater utilities, government agencies, and engineering organizations worldwide. Its clients include the majority of the largest UK, Australasian, East Asian and North American cities, foremost utilities on all five continents, and ENR top-rated design firms.
About Electro Scan
Headquartered in Sacramento, California, Electro Scan develops and markets advanced pipe condition assessment products, field services, and cloud applications that automatically locate, measure, and report defects in sewer, water, and gas pipelines.
Contact:
Carissa Boudwin
(916) 779-0660
info@electroscan.com