Industry News, trenchless products
THOMPSON, CONNECTICUT USA:
Numa, the world’s leading drilling technology provider, announces the release of two new videos spotlighting the company’s capabilities and its industry leading Super Jaws® Overburden Bits. The videos are available on the Numa YouTube site.
The new corporate video highlights the many benefits Numa provides the DTH drilling industry. For over 30 years, Numa has demonstrated its leadership by designing innovative products, diversifying across multiple industry segments, and focusing on serving a global marketplace. The company has hundreds of years of combined rock drilling expertise encompassing all aspects of design, manufacturing, sales, and service. Numa’s expertise and commitment to drillers has led to the development of over 110 rock drilling products and 13 patents to better serve customers. Products are in use in 105+ countries with customers drilling vertical, horizontal, and reverse circulation holes from 3½ to 50½ inches (89 – 1283 mm) in all types of hard rock, overburden, or loose strata formations.
The product video details how Numa’s Super Jaws Overburden Bits are the best method for simultaneously drilling and casing 5½” to 42” (139 – 1067 mm) holes in unconsolidated ground conditions of overburden, boulders, or bedrock. The unique design utilizes wings that extend out to drill a full diameter hole. Upon completion, the wings retract back into the bit body and all tooling is brought back to the surface while leaving the casing in place. There is no reverse rotation required, nor any expensive rings, saving drillers time and money.
“We are excited to release two new videos that highlight Numa’s industry leading capabilities and technology”, said Numa Vice President, Dave Gorman. “The videos demonstrate a few of our key differentiators in the market including our deep experience as drilling experts, our dedication to customer service, and our technological innovation. All of which are crucial factors in maintaining our presence as market leaders and “go to” resources for drillers worldwide.”
ABOUT NUMA
Numa provides the world’s leading drilling technology with over 100 DTH Hammer and Bit products serving 11 different industries. Our products are capable of drilling vertical, horizontal, and reverse circulation holes from 3½ to 50½ inches (89 – 1283 mm) in diameter in hard rock and unconsolidated formations. With customers located in 105+ countries, we have built our customer-centric reputation on providing the highest value in products, performance and personal service available in the rock drilling industry.
Industry News
April 26, 2018 – Kitchener, ON – Ontario’s Water Conference is the premiere drinking water event in Ontario, bringing together operators, manufacturers, academics and regulators to represent the water industry. This year, Deep Trekker will attend the show in Niagara Falls, showcasing its latest robotic systems, designed to improve the water industry. With the recent release at GLOBE Forum 2018, WaterTAP’s latest report, Water: The Next Frontier on the Path to a Low Carbon Economy, notes that clean water technology is critical to meeting GHG emissions targets. Ontario’s water technology sector, including Deep Trekker’s remotely operated vehicles (ROV), is working on creating new solutions across the globe and here in Canada.
WaterTAP’s report recommends a significant focus on clean water technology as a reliable, cost-effective way to lower GHG emissions and create energy savings. Water and wastewater services can consume as much as one-half of a municipality’s total electricity use. The energy used results in substantial greenhouse gas emissions that can be minimized through application of clean water technology across the full spectrum of water services – from wastewater treatment to stormwater management.
Water is of utmost importance to the continued existence of life and for that reason, there are facilities in place with processes to treat and remove contaminants and other harmful bacteria. Regular maintenance and inspection of water tanks is vital to the long-term success of the treatment plant and to the quality of portable water flowing through it.
Deep Trekker’s ROVs allow for frequent, routine inspections at an affordable price. Its portable, compact design and onboard battery source allows operators to quickly deploy the unit without the hassle of additional equipment at the treatment facility. A rotating camera head provides detailed images for inspection diagnosis below, above, behind or in front of the ROV as it navigates throughout the water tank.
Deep Trekker provides significant value to the water industry with its fully submersible remotely operated vehicles, providing clean technology and new environmental solutions.
The team welcomes those attending Ontario’s Water Conference to join us at Booth 332 to hear more about how our robotic systems are improving the water industry, to meet our GHG emissions targets.
Can’t make it to Niagara Falls? Contact Deep Trekker today to chat.
About Deep Trekker Inc.
Deep Trekker Inc. was founded in 2010 with a mission to create portable, affordable, and easy to use harsh environment robotic inspection tools. The company is headquartered in Ontario Canada, with engineering and manufacturing all completed in house. Based on a clean sheet design, the premiere product, the DTG2 ROV was introduced in August 2011. Since that time, Deep Trekker Inc has developed 5 robot lines including 2 ROVs, 2 submersible crawler systems and subsurface surveillance cameras. With sales in over 80 countries, Deep Trekker robots can be found in industries ranging from aquaculture to municipal contracting, military, search and rescue, shipping, infrastructure and more.
For media inquiries, please contact:
Shannon Regan
Communications Specialist
sregan@deeptrekker.com
T: 1-519-342-3177
C: 1-289-879-0188
www.deeptrekker.com
Industry News, trenchless people
Brad Moore is a Principal Engineer with extensive experience as a civil/water resources engineer with project management experience on numerous, multi-disciplined teams for municipal infrastructure projects including planning, design and construction of waterlines, storm and sanitary and CSO conveyance systems.
He has experience in managing multi-disciplined pipeline design teams including conventional open excavation and trenchless construction methods. Brad has 30+ years of experience with over 25 of those years working on numerous public infrastructure projects including over 15 major pipeline projects in Oregon and Washington. Brad is a trusted leader in trenchless technology design and is well-respected by Owners in the Pacific Northwest. His breadth of experience on pipeline projects with trenchless elements make him an asset to any pipeline design team.
Brad loves college hoops and you can always count on a lively conversation about the Sweet 16 with him. He enjoys attending live sporting and music events. Brad also loves spending time with his beautiful family, including two darling grand-sons who always make him smile.
Brad works out of both our Lynnwood, Washington and Portland, Oregon offices.
Staheli Trenchless Consultants (STC) is a specialty engineering firm that focuses on the reduction of trenchless risk through trenchless engineering services including feasibility studies, geotechnical investigations, design and bid services as well as construction management and inspection services. STC provides these services for projects which include microtunneling, horizontal directional drilling, guided boring, auger boring, pipe ramming, pipe bursting, EPB tunneling and in-place rehabilitation such as sliplining and CIPP. STC is a certified WBE in Washington and Oregon.
Industry News, trenchless people
GeoEngineers, Inc. is proud to announce that Principal Jonathan L. Robison, PE has been chosen by the American Society of Civil Engineers (ASCE) to lead the Task Committee creating a Manual of Practice about the trenchless method Direct Pipe®. The committee will be comprised of engineers, contractors, and equipment manufacturers and suppliers from across North America and Europe.
A manual in this ASCE series contains information useful to the average engineer in his or her everyday work, in this case Direct Pipe. Robison has been providing geotechnical, trenchless, geohazard, construction and geophysical project management and engineering services since 1997, and he is a registered Professional Engineer in 15 states. He has led the development of GeoEngineers’ Direct Pipe design process since the technology emerged. GeoEngineers staff, led by Robison, has completed engineering and construction services on numerous successfully completed Direct Pipe projects in the United States and Mexico. He is a member of ASCE and has presented seven technical, peer-reviewed papers on Direct Pipe engineering topics at industry conferences.
Robison is also involved in the trenchless pipeline industry as a member of the North American Society for Trenchless Technology, in which he also serves on the annual No-Dig Conference Program Committee. In addition, he currently represents GeoEngineers on the Industrial Advisory Board for the Trenchless Technology Center at Louisiana Tech University. He works from GeoEngineers’ location in Springfield, Missouri, and he earned his master’s and bachelor’s degrees in civil engineering at University of Missouri, Rolla (now the Missouri University of Science & Technology or Missouri S&T).
GeoEngineers, founded in 1980 and headquartered in Seattle, Washington, is an integrated earth science and technology firm with 12 offices in Missouri, Idaho, Washington, Oregon, California, North Carolina and Louisiana. GeoEngineers specializes in crafting unique environmental, geotechnical, and ecological solutions for the energy, transportation, water and natural resource, federal, and development sectors, and it is currently ranked #223 in the 2017 Engineering News Record Top 500 National Design Firms survey and 23 of the 2017 Trenchless Technology Top 50 Engineering Firms.
GeoEngineers’ pipeline services include the entire life cycle of trenchless projects. This includes geohazards analysis and geological desktop studies; pipeline route selection assistance; feasibility analysis of trenchless methods, including geometry, workspace and constructability; and geotechnical investigations before engineering and construction begins. GeoEngineers also assists in pipeline projects with trenchless design engineering, bid specification preparation and pre-construction support, permitting, construction observation with detailed daily reporting, and post-construction documentation.
For more information, please visit www.geoengineers.com.
Industry News, trenchless people
April 12, 2018 – LAKE MILLS, Wisc. – HammerHead Trenchless of Lake Mills, Wisconsin, a Charles Machine Works company, has promoted three of its top personnel to newly created management positions. HammerHead President Kevin Smith said the new positions are part of an internal expansion initiative that strengthens the company’s existing focus on customers and users.
Smith said: “As we grow, we look to the leaders within our company to step up and help us continue the expansion of all our business areas. These new positions reflect the need to provide dedicated and specialized oversight to those areas of our business that most directly impact the growth and profitability of our customers. The people we’ve chosen have 54 years of industry experience between the three of them, and are known within the industry for their leadership. We look forward to even more success as they help us continue moving our company and industry forward.”
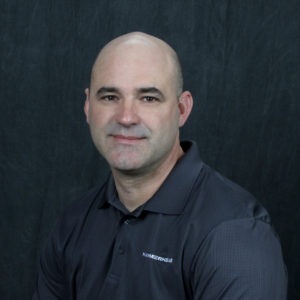
Ryan Boldan is now Director of Support Services. His responsibilities include Marketing & E-Commerce, Inside Sales, Customer Service, Service, and Training & Technical Services teams.
Brian Kenkel is now Director of Rehabilitation and Replacement. In this position Kenkel leads sales teams and provides product management for the HammerHead Trenchless Rehabilitation and Replacement division.
Jeff Urbanski is now Training & Technical Services Manager. In his new position Urbanski and a team of seven technicians are tasked with building HammerHead University – an education center dedicated to the trenchless industry. He will oversee the training facility and direct creation of all e-Learning and testing solutions.
All three promotions were effective immediately.
Photo 1: Ryan Boldan is now Director of Support Services at HammerHead Trenchless.
Photo 2: Brian Kenkel is now Director of Rehabilitation and Replacement at HammerHead Trenchless.
HammerHead® Trenchless, a Charles Machine Works Company, of Lake Mills, Wisconsin, USA manufactures and delivers a unique combination of rehabilitation, replacement and installation equipment and consumables for the underground construction market. Besides being a full solutions provider in rehabilitation and replacement, HammerHead also offers unmatched field support and project consultation to its customers worldwide. HammerHead products are proudly made in the U.S.A. and sold and serviced in more than 63 countries. For more information visit www.hammerheadtrenchless.com.
Industry News, trenchless people
GSSI, the world’s leading manufacturer of ground penetrating radar (GPR) equipment, proudly announces a new territorial sales restructuring designed to better serve customers. GSSI has reorganized its sales department into four regional territories to support further growth in its concrete inspection, non-destructive testing, and utility locating markets. With the new structure, application specialists will be based in the Northeast, Southeast, Northwest, and Southwest, making sales staff closer in proximity to customers. Customers can continue to expect best-in-class products and service support during 2018. Look for increased support staff and enhanced training class offerings in the coming year.
In the Northeast territory, Peter Masters will serve as application specialist. Peter has worked in the concrete and utility markets since 2005 and has been instrumental to the success of the StructureScan and UtilityScan products. He is actively involved in key industry associations, including the ASNT, ACI, CGA and NULCA. Based in the Greater Boston Area, Peter will be responsible for sales in Connecticut, Delaware, Illinois, Indiana, Massachusetts, Maryland, Maine, Michigan, New Hampshire, New Jersey, New York, Ohio, Pennsylvania, Rhode Island, Virginia, Vermont, Washington, DC, Wisconsin, and West Virginia.
The Southwest territory will be served by Michael Phillips, who recently joined GSSI as an application specialist. Mike brings nearly a decade of experience in concrete construction product sales. He will be based out of the Las Vegas area and will serve customers in Arizona, California, New Mexico, Nevada, and Utah.
The Northwest territory will be served by Tom Timperman, who has been with GSSI for two years as the Search & Rescue Product Specialist. Tom brings 20+ years of senior level sales experience and is excited to expand his responsibilities into the concrete and utility markets. Tom is based in Spokane, Washington and will handle customers in Alaska, Colorado, Hawaii, Idaho, Iowa, Kansas, Minnesota, Montana, Nebraska, North Dakota, Oklahoma, Oregon, South Dakota, and Washington.
Bruno Silla will serve the Southeast territory. Bruno has been a concrete application specialist with GSSI for four years. Based out of Fort Meyers, Florida, Bruno is actively involved in the Concrete Sawing and Drilling Association (CSDA), serving as the GPR Committee Vice Chair and Next-Gen Committee Vice Chair. His responsibility includes Alabama, Arkansas, Florida, Georgia, Kentucky, Louisiana, Missouri, Mississippi, North Carolina, South Caroline, Tennessee, and Texas.
About GSSI
Geophysical Survey Systems, Inc. is the world leader in the development, manufacture, and sale of ground penetrating radar (GPR) equipment, primarily for the concrete inspection, utility mapping and locating, road and bridge deck evaluation, geophysics, and archaeology markets. Our equipment is used all over the world to explore the subsurface of the earth and to inspect infrastructure systems non-destructively. GSSI created the first commercial GPR system over 45 years ago and continues to provide the widest range and highest quality GPR equipment available today.