Industry News
The ASTT Technical Forums are back in 2018!
After a successful year of forums in 2017, the Australasian Society for Trenchless Technology (ASTT) are pleased to be again offering the following Technical Forums to start 2018:
VIC – Thursday 8 March – 3 to 6.30 pm – Woodward Conference Centre, Carlton
NSW – Thursday 22 March – 3 to 6.30 pm – Sydney Water, Parramatta
For further information on who will be speaking at each forum, please visit the event website.
The forums will be attended by key industry decision makers, contractors and manufacturers, with plenty of opportunities to network over canapés and drinks after the presentations.
Event registration for ASTT members is just AU$45. Registration for non-members is AU$65.
Did you know they also have forums throughout New Zealand in Auckland, Christchurch and Wellington? If you would like further information on these please visit the New Zealand Trenchless Technology Roadshow website.
Interested in presenting or sponsoring any of the ASTT Technical Forums? Please contact Rebecca Burns at rburns@gs-press.com.au.
Industry News, trenchless people, trenchless products
Jacksonville, FL – SIPP Technologies LLC. (SippTech) CEO/CTO Kent Weisenberg announced recently an agreement with SAK Construction, LLC. (SAK) for exclusive installation rights of its SippSteel™ robotic lining technology. Pursuant to the agreement, SAK is the sole national installation contractor for SippTech’s multidimensional, robotically installed, composite pressure pipe lining system.
“SippTech is honored to partner with SAK. Their knowledge, experience, and innovative thinking in the pipeline rehabilitation industry offers the ‘perfect storm’ of opportunity for SippSteel™. SAK has been expertly delivering the most advanced, field proven products to rehabilitate pipes globally for years.” Mr. Weisenberg stated.
SippSteel™ is a novel, three-component composite lining system that entirely overcomes the limitations and inconsistencies present in prior SIPP technologies. This is made possible by utilizing a combination of specific and cooperative machine learning technologies, including computer-vision, LIDAR ultrasound, RF, Wi-Fi, gyroscope, and accelerometer, to precisely navigate and apply the SippSteel™ composite inside of the pipe. The result is the installation of a structurally independent lining system with reduced construction time, minimal consumer disruption, lower costs, and a small environmental footprint.
“This unique, cutting-edge technology truly has the capability to change the entire dynamic of the pressure pipe rehabilitation industry,” stated Charlie Kuhnmuench, V.P. of Business Development for SAK. “We look forward to working together with SippTech to expand this technology throughout the United States. To date, we have not seen a trenchless rehabilitation technology possessing such efficacy and versatility for the pressure pipe industry,” added Jerry Shaw, President of SAK.
Based in O’Fallon, Missouri, and with additional regional offices in Arbutus, Maryland; Sacramento, California; and Nashville, Tennessee, SAK is active across the U.S. The company solves the challenge of maintaining and restoring aging water and sanitary infrastructure for the municipal, energy and industrial markets. With industry-leading experience and a commitment to service excellence, SAK is a trusted partner helping customers worldwide renew, protect and expand their pipeline infrastructure.
SippTech is truly unique in that they are the only SIPP company to conceptualize, design, engineer and manufacture robotic lining systems and develop and manufacture propriety lining polymerics. The result is a synergistic collaboration providing revolutionary, reliable robotic and polymeric systems to the marketplace.
Please visit www.sipptech.com for more information on Spray in Place Pipe technology.
Contact:
Tiffany Laufer
SippTech Technologies, LLC.
tiffanyl@sipptech.com
904.374.5606
Industry News, trenchless products
Compact and high productivity for everyday applications
PELLA, Iowa, February 13, 2018 – Vermeer expands its line of utility installation equipment with the launch of the D8x12 Navigator® horizontal directional drill. This new compact and highly productive drill is sized for working in tight spaces, features straightforward controls and delivers quiet operation. With two drill rod options for added versatility, the Vermeer D8x12 is well suited for small service installations, including gas distribution, power, water and telecommunication networks.
“From fiber-to-the-home projects to residential utility upgrades, there is a growing demand for compact horizontal directional drills that can easily access residential backyards, are lightweight to help reduce turf damage and quiet to minimize neighbor disturbances,” explained Tod Michael, product manager of trenchless products at Vermeer. “With the D8x12, we were able to exceed contractors’ expectations in all of those areas and more. It’s an affordable service-oriented machine that is over 29 percent more powerful than similarly sized drills on the market today.”
The Vermeer D8x12 horizontal directional drill is equipped with a 48 hp (35.8 kW) Kohler diesel engine and offers 1,000 ft-lb (1,355.8 Nm) of spindle torque and 7,850 pounds (34.9 kN) of thrust/pullback. It features basic hydraulic pilot joystick controls with only essential electrical components, simplifying operation and routine maintenance.
With a low noise emission level of 85 dBA at the operator’s ear and guaranteed sound power of 104 dBA, the D8x12 is an excellent machine for working in urban environments. It can fit through a 36-inch (91.4 cm) gate or onto a trailer with other jobsite essentials.
While on the job, the D8x12 drill’s tracks provide optimized traction for operations with little ground disturbance. With a forward travel speed of 2.8 mph (4.5 km/h), this compact drill can quickly be repositioned between bores.
The Vermeer D8x12 also gives contractors multiple drill rod options. Choose a 1.31” (3.4 cm) diameter Firestick® drill rod when tight steering is required, or 1.66” (4.2 cm) diameter drill rod for more demanding ground conditions and longer drill shots. In addition, it can share tooling with several current and previous Vermeer drill models, including the D6x6, D7x11 Series II, D9x13 S3 and D10x15 S3 Navigator horizontal directional drills.
For more information about the Vermeer D8x12 Navigator horizontal directional drill, visit Vermeer.com or contact your local Vermeer dealer.
ABOUT VERMEER
Vermeer Corporation delivers a real impact in a progressing world through the manufacture of high-quality tree care, environmental, underground construction, surface mining, and agricultural equipment. With a reputation for durability and reliability, that equipment is backed by localized customer service and support provided by independent dealers around the world. To learn more about Vermeer Corporation, products, the dealer network and financing options, visit Vermeer.com.
Industry News, trenchless people
Staheli Trenchless is excited to announce the addition of Mark Hutchinson to their team!
Mark Hutchinson is a Senior Technical Advisor with over 38 years of experience in design and construction of municipal storm water, waste water, and CSO projects. He has developed, lead or facilitated teams of engineers, technicians, and inspectors to safely deliver high quality, functional projects under budget and on time. Mark uses his experience to mentor and problem solve – drawing on a variety of trenchless projects he has worked on including microtunneling, pipe bursting, CIPP, large diameter tunneling, hand tunnels, jack & bore, pilot bore, and HDD projects. He is also well versed in shafts, shoring & ground improvement design & construction utilizing slurry wall, secant piles, jet grout, caissons, H-pile, sheet pile, stone columns, compaction, and permeation grouting.
As Construction Division Manager for the City of Portland for over 13 years and project manager for another 20 years he oversaw completion of their CSO program and the transition to 20 plus miles a year of pipe rehabilitation utilizing CIPP, pipe-bursting, slip lining, open cut and spot repair from 6-inch to 120-inch diameter on a variety of pipe materials from brick pipe to cast iron. He has also used a variety contracting methodologies to achieve project goals, as well as dispute resolution methodologies to reduce construction claims and litigation costs. He is well known by most construction contractors in the Northwest and respected in all manners of construction management and inspection.
Mark’s energy, passion for trenchless technology and zest for life make him a pleasure to work with. He is a big family man with three children, and six grandchildren. He is active in his church and an avid fisherman and gardener. If you were to ask him where the fish are biting, he could easily tell you where and when he plans to go fishing next in one of his boats.
Mark will be working out of both of Staheli’s Lynnwood, Washington and Portland, Oregon offices.
Staheli Trenchless Consultants (STC) is a specialty engineering firm that focuses on the reduction of trenchless risk through trenchless engineering services including feasibility studies, geotechnical investigations, design and bid services as well as construction management and inspection services. STC provides these services for projects which include microtunneling, horizontal directional drilling, guided boring, auger boring, pipe ramming, pipe bursting, EPB tunneling and in-place rehabilitation such as sliplining and CIPP. STC is a certified WBE in Washington and Oregon.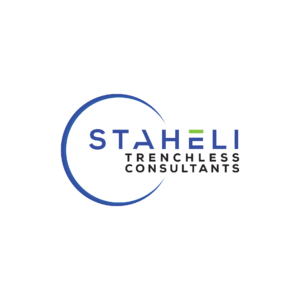
Industry News, trenchless products
January 22, 2018 – LAKE MILLS, Wisc. – HammerHead Trenchless, a Charles Machine Works Company, has released the first model of its new XPR series of high-performance pneumatic hammers for pipe ramming and pipe bursting applications. The XPR series features a newly designed high-flow valve system that produces a more powerful impact. The first model to utilize this new technology, the 26XPR, is the most powerful pneumatic hammer in its class.
The XPR technology is a modification of the patented Air Reverse (AR) valve system standard on all HammerHead pneumatic hammers larger than 7 inches (180 mm). Both systems allow for the reverse function to be controlled above ground, greatly simplifying tool removal from pushing collets and burst heads, saving valuable time on the job.
The 26XPR, a 26-inch hammer, is the first model to be equipped with the performance-enhancing XPR technology. It has replaced the 24-inch AR model in the HammerHead line of pneumatic hammers.
“While our 24-inch hammer has proven to be durable and effective, we identified a need for a more versatile and higher performing tool,” said product manager, Josh Hood. “By designing a system that maximizes the air flow, we were able to increase forward horsepower while maintaining the highly desired functionality of the Air Reverse feature. We chose the 26XPR to be the first model to utilize the new technology to better bridge the gap between our 20- and 34-inch AR models.”
The 26XPR is capable of installing casing 24 to 84 inches in diameter and is suitable for use in drainage culverts, pipeline work, and HDD assist methods such as wash over casing installations, pipe assist or pipe extraction, and guided pilot bore ramming.
It is also effective in pneumatic pipe bursting applications of pipes ranging from 15 to 36 inches in diameter.
The hallmark of all HammerHead Trenchless pneumatic hammers, including the new 26XPR, is easy serviceability to minimize costly downtime due to tool maintenance. It features HammerHead’s patented clamped rear anvil and tail bolt designs, one-piece body and striker, and high-temperature replaceable wear rings.
HammerHead Trenchless produces 11 models of pneumatic hammers ranging from 4 to 34 inches, capable of ramming pipe diameters ranging from 4 to 180 inches or bursting pipe diameters from 4 to 36 inches.
While the 26XPR is the first model of the new XPR series, HammerHead Trenchless plans to expand the series in the future by equipping other sizes of hammer with the high-performance technology.
The 26XPR hammer is available from HammerHead Trenchless or from authorized dealers, worldwide. Authorized dealers can be found on the web at www.hammerheadtrenchless.com or by calling 800.331.6653. (International: + [1] 920.648.4848).
Photo Caption: The new 26XPR hammer features high flow technology increasing both power and productivity.
Industry News, trenchless people
Are you an engineering or construction management student? Is trenchless technology your passion or something you’re interested in learning more about? Networking is an important step in establishing relationships within the trenchless community. What better way to begin your trenchless career than to become an NASTT Student Non-Affiliated Member. NASTT is excited to offer this brand new student membership opportunity for you.
This student membership is open to any student actively enrolled full-time in a North American university or college that does not currently host an NASTT Student Chapter. The cost for this Student Membership is just $50.00 USD per year and grants you access to the full spectrum of member benefits, including unlimited technical paper downloads!
Join us and learn how you can broaden your network! For more information or if you have any questions, please contact Renee Corea, NASTT Membership Administrator.