Industry News, trenchless products
Vac-Tron Equipment hosted a Red Carpet event to celebrate their 6,000th unit being built, along with their Low Profile trailer mounted industrial vacuum unit debuting in Logan Lucky, a new hit comedy. The event was held in the Villages, FL where Vac-Tron hosted the screening and was a chance for its employees and their families to celebrate this monumental event. Also in attendance was Vac-Tron’s customer Echo Utility Engineering and Surveying, who recently purchased the 6,000th unit, along with Vac-Tron’s dealer, Vermeer Southeast.
‘Lucky’ doesn’t begin to describe the amazing product placement that Vac-Tron received on the big screen. The movie showed the true power of the Vac-Tron units as actors Channing Tatum, Daniel Craig, and Adam Driver used the unit to suck money out of an underground vault and into the vacuum unit for the big heist.
The Vac-Tron unit made its ‘star’ appearance within a few minutes of the movie starting. It was a surreal experience to see the Vac-Tron unit live and in action with the loud cheers from the crowd. The movie showcased the unit at least 10 times with extended periods during each shot and the crowd’s enthusiasm increased every time. This was a humbling experience for the employees of Vac-Tron to see a unit that they built in the little city of Okahumpka, FL make it to the big screen. Vac-Tron units have been built in Central Florida for over 20 years and shipped all around the world.
A reporter with The Daily Sun interviewed Vac-Tron’s Founder Don Buckner and President Tim Fischer. “We never thought that we’d make it on the big screen and we are excited for all of our employees. We have a great team and to be able to celebrate this event and our 6,000th unit is a true honor”, said Fischer.
“I started Vac-Tron in my two-car garage more than 20 years ago. We started with nothing and built it to the organization it is today,” said Buckner. “It’s just surreal to me to imagine that we had this kind of success with our equipment.”
It’s no wonder the director decided to use a Vac-Tron unit when looking for a versatile way to safely dig and suck material up quickly for a project, even if it was just for a movie. While Vac-Tron does not list “robbing a NASCAR race”, as an application for its product, there are many highly efficient applications for a Vac-Tron unit, i.e. locating utilities, potholing, directional drilling, controlled excavation, industrial cleanup and many more.
Vac-Tron Equipment is the industry’s innovative leader and one of the world’s largest producers of industrial vacuum equipment and vacuum excavation equipment. Vac-Tron Equipment, which has more than 30 industrial vacuum products and more than 50 wet and dry uses, has 115 dealer locations in North America.
Contact vactron.com for a demo in your area.
trenchless products
THOMPSON, CONNECTICUT USA, August 31, 2017:
Numa, the world’s leading drilling technology provider, is proud to announce the addition of Mudlogic as its new distributor in Australia, New Zealand, Papua New Guinea, Indonesia, Philippines, and Malaysia. Mudlogic supplies drilling fluids, muds, and specialty products to the mining, water well, foundation, construction, tunneling, and HDD industries in Australia and SE Asia.
Mudlogic offers a growing line of drilling products combined with on-site technical support to help customers in the region reduce overall cost of operation. Mudlogic is renowned for its expertise developed through years of experience working in the field with customers to support their needs.
“Mudlogic keeps abreast of advancements in new technology and changes in the industry so they can provide the region with the best products and advice for the task at hand,” said Ralph Leonard, President of Numa. “Numa is very excited to have teamed with Mudlogic who takes great pride and care in the product line and service they deliver”.
Geoff Wood, General Manager of Mudlogic added, “We are delighted to join the Numa family of distributors. Numa’s world’s leading DTH hammers and bits are the perfect solution for customers in our region looking for the best way to handle any rock drilling needs.”
For more information please visit their website mudlogic.com.au
ABOUT NUMA
Numa provides the world’s leading drilling technology with over 110 DTH Hammer and Bit products serving 11 different industries. Our products are designed to drill vertical, horizontal, and reverse circulation holes from 3½ to 48 inches (89 – 1219 mm) in diameter in hard rock, overburden, or loose strata formations. Having customers in 105+ countries, we have built our customer-centric reputation on providing the highest value in products, performance, and personal service available in the rock drilling industry.
ABOUT MUDLOGIC
The Mudlogic Group is an independent, privately owned specialty drilling fluid and consumables supplier. We have a focus on the Australian and South East Asian region with strategically located offices in Brisbane, Perth, Kalgoorlie and Singapore. Our systems, combined with our on-site technical support and our commercially competitive pricing, will reduce overall cost of operation. We are committed to enabling better processes, offering innovative products for all drilling and special foundation applications as a genuine alternative supplier. This all means that we do better and go further to not only meet, but exceed our customer expectations.
Industry News, trenchless products
Armadrillco High-Flow/Side-Load Housing Adapted to the RockEye
(Hutchinson, Kansas) – The spring 2017 acquisition of Armadrillco® solidified StraightLine HDD’s position as a leader in hard condition tooling. The announcement today of the adaption of the patented Armadrillco transmitter housing to the RockEye® Hammer System is a significant step in diffusing Armadrillco technology throughout StraightLine HDD tooling platforms.
Adapting Armadrillco side-load housing technology gives users easy access to electronics, larger capacity fluid/air passages and improved durability. The housing’s patented Arma-Loc® system is a field-proven design that gives users quick access to electronics by virtue of removing a single pin. Free from threads, the Arma-Loc system virtually eliminates problems associated with damaged or over-torqued bolts, as well as vibration-induced lid failure.
The industry’s most secure lid retention system is also the most protected. Working in tandem with the Arma-Loc lid security system, a patented urethane and O-ring system is designed to seal and protect the sonde cavity from fluid/debris infiltration. The system also forms a cushioned platform that shields valuable electronics from punishing vibration and heat produced by a hammer working in harsh rock environments.
Large internal passages, up to 1-inch in diameter, represent a significant improvement in air/fluid flow. The larger passages are capable of delivering air volume up to 1,200 CFM and fluid volume of 300+ GPM.
Visit www.straightlinehdd.com and www.sourcehdd.com for more information.
Industry News, trenchless products
GSSI, the world’s leading manufacturer of ground penetrating radar (GPR) equipment, announces a new engineering initiative focusing on using GPR to solve difficult problems that cannot be solved with any other technologies. Led by newly appointed Vice President of Research and Development David Cist, GSSI’s expert engineering team is focusing on new products for agriculture, manufacturing, robotic inspection, industrial quality assurance/quality control, power systems preventative maintenance, and unmanned autonomous vehicle applications. GSSI’s custom solutions create completely new products, different models of existing products, or a combination of the two.
“GSSI has a long established history of developing products based on custom needs, and has commercialized several that meet broader market needs,” said Cist. “The custom solutions engineering team brainstorms with customers who are looking for novel ways of handling problems. Often enough, GPR can offer a real solution to difficult problems that can’t be solved any other way. One recent outcome is the creation of a new GPR product line with a sensor that can be integrated into a variety of robots, drones, and other equipment.”
GSSI’s PaveScan® RDM asphalt density assessment tool, which provides accurate real-time measurements to ensure pavement life and quality, was originally developed based on work commissioned by the Texas Transportation Institute (TTI) as part of the Federal Highway Administration’s Strategic Highway Research Program (SHRP2). The commercial version is now being used by state departments of transportation in Minnesota, Alaska, Maine, and Florida, as well as globally in transportation research projects conducted by universities.
Other custom products commercialized by GSSI include the LifeLocator® TRx survivor detection system, which was originally developed in response to post-911 Homeland Security market needs. GSSI also developed one of the sensors used by the RABIT™ bridge deck assessment tool to determine bridge quality and bridge deterioration. RABIT™, developed by the Rutgers Center for Advanced Infrastructure and Transportation, is an autonomous robot that gathers quantitative data using several nondestructive evaluation technologies. The StructureScan Mini system was developed based on a specific request from one of GSSI’s largest customers in Japan, which years later was seeking a new software solution that would allow them to use the system to analyze insulated concrete forms.
The GSSI custom solution applications engineering team has developed GPR systems for golf course irrigation inspection, tree root inspection, horizontal drilling, detecting the porosity of bricks, and border patrol tunnel inspection systems. Applications under development include use of GPR to establish precise soil elevation and inspection of large and expensive equipment tires used in mining.
For more information on custom solutions and products based on GSSI’s GPR technology, contact sales@geophysical.com.
About GSSI
Geophysical Survey Systems, Inc. is the world leader in the development, manufacture, and sale of ground penetrating radar (GPR) equipment, primarily for the concrete inspection, utility mapping and locating, road and bridge deck evaluation, geophysics, and archaeology markets. Our equipment is used all over the world to explore the subsurface of the earth and to inspect infrastructure systems non-destructively. GSSI created the first commercial GPR system nearly 50 years ago and continues to provide the widest range and highest quality GPR equipment available today.
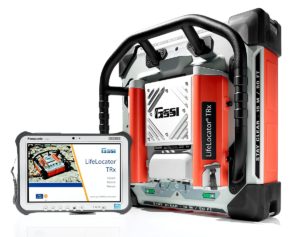
Blog, Industry News, trenchless products
XL-I Series Hole Openers Are Designed From the Ground Up For HDD
(Hutchinson, Kansas) – StraightLine HDD recently expanded its hole opener offering with the introduction of the XL-I Series. Designed from the ground up for horizontal directional drilling, the XL-I Series is positioned as a cost-effective alternative to “split-bit” hole openers.
At the core of the design are proprietary cones—available in six sizes, in either Tungsten Carbide or Mill Tooth configurations. Mounted to a purpose-built platform, the design facilitates load transfer to the shaft and bearing, with minimal radial load. The result is a dramatic improvement in production, service life and consistency, bore after bore.
Next, designers set out to address wear and performance characteristics by re-examining the interplay between cone diameter, height and carbide placement. Cones are sized and attached to the baseplate at an angle that protects vulnerable surfaces. Shortened cone height further improves wear resistance. Carbides placed to cut independent paths yield higher efficiency and longer service life.
Internally, the cone’s proprietary sealing and bearing system mitigates fluid intrusion, yielding a myriad of user benefits, from reduced torque and fuel consumption to extended tool life.
As a platform, the XL-I Series incorporates design characteristics that ensure the tool’s original geometry is maintained—even after rebuild. This approach yields consistent and repeatable performance.
The XL-I Series includes six sizes, from 12.75- to 24-inches with IF Box x Box shafts.
About StraightLine HDD
Since 1984, StraightLine has produced drilling solutions” to the trenchless industry. It’s full line of down-hole tools, wear parts and accessories are known for their innovative and rugged design. The portfolio now includes the full array of hard condition tools under the Armadrillco brand. In 2015, StraightLine HDD merged operations with Source: HDD, Inc., a leading provider of used HDD rigs and support equipment. Together, the merger created a company offering total HDD solutions—from rig to bit. Call 620.802.0200 or visit www.straightlinehdd.com for details.
Blog, Industry News, trenchless products
THOMPSON, CONNECTICUT USA, Jun 27, 2017:
Numa, the world’s leading drilling technology provider, has announced an expansion of manufacturing capabilities at its US plant to keep up with growing demand for its DTH hammers and bits.
Over the past several years, Numa has heavily invested in its manufacturing capabilities to tackle the demands of building the world’s leading DTH equipment. The latest addition is a Doosan Puma 3100 which is a composite turning center that combines the functions of both a lathe and a machining center. By integrating the capabilities of multiple machines into one system, the turning center minimizes machining time and the number of machining operations. Complicated parts that previously required multiple machines and setups can now be completed by just one unit and one setup. The new equipment will improve productivity, precision, and ease of operation for the company and further improve its ability to manufacture quality products in a timely manner for its customers.
“The expansion of Numa’s manufacturing capabilities supports our vision for growth and puts us in the best position to build the world’s leading down hole hammers and bits,” said Ralph Leonard, President of Numa, “The new multi-tasking turning center offers higher productivity, greater accuracy, and enhanced user convenience which is instrumental to support the growth of our customers.”
ABOUT NUMA
Numa provides the world’s leading drilling technology with over 110 DTH Hammer and Bit products serving 11 different industries. Our products are designed to drill vertical, horizontal, and reverse circulation holes from 3½ to 48 inches (89 – 1219 mm) in diameter in hard rock, overburden, or loose strata formations. Having customers in 105+ countries, we have built our customer-centric reputation on providing the highest value in products, performance, and personal service available in the rock drilling industry.