Industry News, trenchless people, trenchless products
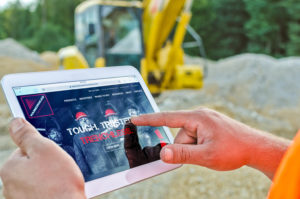
May 7, 2018 – LAKE MILLS, Wisc. – The launch of the newly redesigned HammerHeadTrenchless.com website now gives customers in a wide range of industries even faster, easier access to in-depth information and resources regarding trenchless methods, products and consumables.
Jason Haas, Marketing & e-Commerce Manager at HammerHead Trenchless, a Charles Machine Works Company, said the website redesign was driven by the company’s commitment to providing unsurpassed customer support.
“The focus of our business is always on keeping our customers as productive as possible,” Haas said. “Improving user experience of our website is simply an extension of our dedication to their productivity.”
Haas said the guiding principle of the redesign was twofold: “We set out to create a site with easy-to-navigate, comprehensive content about trenchless methods and the broad suite of solutions we offer, keeping it as efficient as possible.”
Users of the new site navigate to HammerHead products and educational materials by the trenchless method and the industry served. The site’s responsive design has been optimized for desktop, mobile and tablet devices, so it can be conveniently accessed from any platform, anywhere.
Improved navigation and modern design are not the only changes, however. Additional new features include:
- A dealer Locator tool to quickly find sales, service and contact information
- Enhanced product pages, including updated descriptions, specifications and media galleries
- Links to purchase product on the HammerHeadShop.com e-commerce site
- Industry-specific content that helps users find trenchless solutions matching their unique needs
- Access to the HammerHead resource library containing user manuals, product literature and more
Explore all the new features of the site at www.HammerHeadTrenchless.com.
Industry News, trenchless products
THOMPSON, CONNECTICUT USA:
Numa, the world’s leading drilling technology provider, announces the release of two new videos spotlighting the company’s capabilities and its industry leading Super Jaws® Overburden Bits. The videos are available on the Numa YouTube site.
The new corporate video highlights the many benefits Numa provides the DTH drilling industry. For over 30 years, Numa has demonstrated its leadership by designing innovative products, diversifying across multiple industry segments, and focusing on serving a global marketplace. The company has hundreds of years of combined rock drilling expertise encompassing all aspects of design, manufacturing, sales, and service. Numa’s expertise and commitment to drillers has led to the development of over 110 rock drilling products and 13 patents to better serve customers. Products are in use in 105+ countries with customers drilling vertical, horizontal, and reverse circulation holes from 3½ to 50½ inches (89 – 1283 mm) in all types of hard rock, overburden, or loose strata formations.
The product video details how Numa’s Super Jaws Overburden Bits are the best method for simultaneously drilling and casing 5½” to 42” (139 – 1067 mm) holes in unconsolidated ground conditions of overburden, boulders, or bedrock. The unique design utilizes wings that extend out to drill a full diameter hole. Upon completion, the wings retract back into the bit body and all tooling is brought back to the surface while leaving the casing in place. There is no reverse rotation required, nor any expensive rings, saving drillers time and money.
“We are excited to release two new videos that highlight Numa’s industry leading capabilities and technology”, said Numa Vice President, Dave Gorman. “The videos demonstrate a few of our key differentiators in the market including our deep experience as drilling experts, our dedication to customer service, and our technological innovation. All of which are crucial factors in maintaining our presence as market leaders and “go to” resources for drillers worldwide.”
ABOUT NUMA
Numa provides the world’s leading drilling technology with over 100 DTH Hammer and Bit products serving 11 different industries. Our products are capable of drilling vertical, horizontal, and reverse circulation holes from 3½ to 50½ inches (89 – 1283 mm) in diameter in hard rock and unconsolidated formations. With customers located in 105+ countries, we have built our customer-centric reputation on providing the highest value in products, performance and personal service available in the rock drilling industry.
Industry News, trenchless products
Chicago’s Albany Park Diversion Tunnel to go online this spring
In Chicago, Illinois, USA Kenny Construction is nearing completion on the Albany Park Stormwater Diversion Tunnel. The project, owned by the Chicago Department of Transportation, will divert water from the Albany Park neighborhood, which has long been plagued by flooding. Plans for the tunnel began in 2013, after flood conditions became so severe that residents had to be evacuated from the area by boat. The tunnel is expected to be functional by April 2018.
A Robbins Main Beam Hard Rock TBM bored the tunnel and broke through at the end of August 2017, bringing the project one step closer to completion. The TBM, also known as “Keri,” has been owned by project contractor Kenny Construction since the 1990s and has been used on several projects prior. “The machine holed through into the inlet shaft,” said Clay Spellman, Project Manager for Kenny Construction. “We excavated the shaft as part of the project. The machine has since been disassembled and removed.”
For the Albany Park Project, Keri was rebuilt by Kenny Construction with size modifications designed by Robbins. Robbins took an existing cutterhead, repaired it, and then added segments, taking it from 5.2 m (17.2 ft) to 6.2 m (20.4 ft) in diameter. “Extensive modifications were also made underground to the machine to be able to install rock dowels and stand the ring steel under the roof shield,” added Spellman.
“Rebuilding TBMs has always been a core part of Robbins’ business. Most customers immediately recognize that a rebuilt machine with updated systems can offer exceptional value without increasing risk, and a rebuilt machine can usually be delivered faster,” said Robbins Engineering Manager Steve Smading. “While the financial and schedule advantages are obvious, the flexibility of used equipment may be less obvious. Boring diameters can be increased or decreased and machine configurations can even be changed. For example, a Single Shield can be reconfigured as a Double Shield or vice versa, and a Main Beam TBM can be reconfigured as a shielded machine. Soft ground machines can be configured for different geologies and can be set up as either Slurry or EPB.”
Over 50 percent of all Robbins Main Beams ever manufactured have been used on three or more projects. Incredibly, many Robbins TBMs that have been used on multiple projects are approaching over 50 km (31 mi) of use. Prior to its ownership by Kenny, Keri has successfully bored tunnels in the Dominican Republic, Saudi Arabia, New York, and Chicago—totaling at least 19.5 km (12 mi) of tunnel.
Due to the project location in a residential neighborhood, there were restrictions in place as to when the machine could operate and the frequency at which blasting would be allowed per day. Despite these limitations, the TBM achieved a best day of 39.5 m (129.7 ft) and a best week (5 days) of 146.4 m (480.4 ft). The machine bored through dolomite with an average compressive strength of 64 MPa UCS (9,300 psi). “During boring we encountered approximately 30.4 m (100 ft) of fractured ground that had to be supported with rolled channels, straps, and 19 full circle steel rings,” said Spellman.
The drainage tunnel starts in Eugene Park and extends for approximately one mile under Foster Avenue to the North Shore Channel. When the Chicago River’s water levels reach flood stages—exceeding 2 m (7 ft)—the tunnel will divert a flow of 65 cubic meters (2,300 cubic ft) of water per second, avoiding Albany Park, then deposit it into the Channel. The tunnel will essentially be transferring the water where it would have ended up, without damaging the residential area or adversely affecting the river’s wildlife.
Image 1: The 6.2 m (20.4 ft) diameter Robbins Main Beam TBM broke through in August 2017 on Chicago, USA’s Albany Park Diversion Tunnel, which will go online this April.
Image 2: The resilient machine was rebuilt by Kenny Construction with size modifications designed by Robbins.
Industry News, trenchless products
GSSI, the world’s leading manufacturer of ground penetrating radar (GPR) equipment, has launched its dynamic new website. With a completely redesigned look and feel that makes it easier than ever to use, the website’s homepage is designed to help customers explore GSSI’s product range. It features a helpful and easy to use product configurator, quick access to the training class calendar, and all the latest news and updates, including the most recent case studies and videos.
The new Innovation Lab section spotlights GSSI’s most recent engineering initiatives and custom solutions. Learn about GSSI’s approach to developing customer solutions and examples of successful processes used to meet customers’ challenges.
The product pages feature a wealth of pictures showing the equipment in action and clear explanations of applications for which it is most useful. Users will also find data examples for each application and product, detailed product specifications, and a host of support material to help users get the most out of the equipment.
The expanded training section – now called GSSI Academy – includes an enhanced class schedule, trainer bios, training request form, and easy to understand explanations about GPR and electromagnetic induction (EM) technology.
The new website also features a greatly expanded support page, which now includes direct access to user manuals and software updates.
For more information on GSSI and to see the new website in action, visit www.geophysical.com.
About GSSI
Geophysical Survey Systems, Inc. is the world leader in the development, manufacture, and sale of ground penetrating radar (GPR) equipment, primarily for the concrete inspection, utility mapping and locating, road and bridge deck evaluation, geophysics, and archaeology markets. Our equipment is used all over the world to explore the subsurface of the earth and to inspect infrastructure systems non-destructively. GSSI created the first commercial GPR system over 45 years ago and continues to provide the widest range and highest quality GPR equipment available today.
Industry News, trenchless products
Challenging Ground Conditions are No Match for Talented Team and their TBM
In Jilin, one of the three provinces of Northeast China, a 7.9 m (26 ft) diameter Robbins
Hard Rock Main Beam TBM has achieved a national record for 7 to 8 meter (23 to 26 ft) machines: 1,423.5 m (4,670 ft) in one month. The record tops a previously-set achievement on the same project from earlier in 2017, when the TBM advanced at a rate of 1,336.8 m (4,386 ft) in one month.
The world record for the size class is held by another Robbins machine, set more than 20 years ago at the Tunnel and Reservoir Plan (TARP) in Chicago, Illinois, USA, for 1,482 m (4,862 ft) in one month. However, given the differences in rock conditions this Jilin project record is very significant. At TARP the rock was relatively homogeneous dolomitic limestone averaging 145 MPa/21,100 psi with occasional rock bolts; at Jilin the rock types were rated from 35 to 206 MPa UCS (5,100 to 30,000 psi), and identified as tuff, granite, sandstone, and andesite with multiple fault zones—conditions requiring nearly continuous ground support.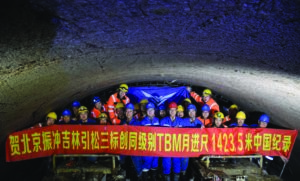
Despite the difficult conditions, the Jilin machine has achieved an average monthly advance rate of 708.3 m since the start of boring in March 2015—more than three times the average monthly rate of a Drill & Blast operation on another section of the project. “It is now very evident that well-equipped, open-type Main Beam TBMs with specialized features for difficult ground can traverse faults and large water inflows much faster than conventional tunneling methods. This fact, coupled with the high performance capabilities as demonstrated at Jilin, lowers the cost and time to complete long tunnels in difficult ground,” said Robbins President Lok Home.
The Jilin Lot 3 tunnel, which is being bored as part of a water conservation project, will be 24.3 km (15 mi) long when complete. Under contractor Beijing Vibroflotation Engineering Co. Ltd. (BVEC), the machine has excavated 14 km (8.7 mi) of the tunnel as of January 2018.
Throughout its bore, the Main Beam is expected to traverse a total of 24 fault zones. The TBM was designed accordingly, and is equipped with four rock drills, McNally pockets in the roof shield for the ability to install McNally slats, a ring beam erector, and a shotcrete system. The McNally slats were used in difficult ground encountered in the tunnel.
The McNally Roof Support System was designed and patented by C&M McNally and licensed for exclusive use on Robbins TBMs in certain markets. By replacing the roof shield fingers on a Main Beam TBM, the McNally system prevents movement of loose rock in the critical area immediately behind the cutterhead support. The system has been tested and proven on projects worldwide—including the world’s second deepest civil works tunnel, the 2,000 m (1.2 mi) deep Olmos Trans-Andean Tunnel in Peru—to increase advance rates while still maintaining worker safety on Main Beam machines in difficult rock conditions.
The Jilin TBM’s first fault zone was encountered after just 87 m (285 ft) of boring, requiring cooperation between the owner, Jilin Province Water Investment Group Co., Ltd., contractor BVEC, and Robbins field service. Water inflows and collapsing ground in a section measuring 1,196 m (3,926 ft) long were resolved with a combination of McNally slats, grouting, and consolidation of the ground ahead of the machine. Ground support overall consists of wire mesh and shotcrete. Tunnel Reflection Tomography (TRT)—a method of ground prediction using seismic waves—is also being used to detect changing conditions ahead of the TBM.
Despite the initial challenges, the TBM is now achieving between 40 and 60 m (130 to 197 ft) advance per day. “My colleagues and I all feel that the Robbins TBM is very easy to operate. All components of the system work well during operation, which has ensured our good progress,” said by Tao Yong, BVEC Jilin Lot 3 TBM Site Manager.
The Jilin Lot 3 tunnel is part of the Jilin Yinsong Water Supply Project, which will convey water to the central cities of Jilin Province. The large-scale, trans-regional water diversion project is the longest water supply line, measuring 263.5 km (163.7 mi), with the largest number of recipients benefiting from it in the history of Jilin Province. The construction project will divert the water from Fengman Reservoir at the upper reaches of Di’er Songhua River to central regions of Jilin Province experiencing chronic water shortages. These regions include the cities of Changchun and Siping, eight surrounding counties, and 26 villages and towns under their jurisdiction. Tunneling is expected to be complete in late 2018.
Image 1: The 7.9 m (26 ft) Robbins Main Beam TBM achieved a national record for its size class, excavating 1,423.5 m (4,670 ft) in one month.
Image 2: The crew celebrates the national-record-setting Robbins TBM for China’s Jilin Lot 3 tunnel. The machine excavated in far more difficult ground at a higher rock strength than the current world record holder—also a Robbins TBM.
Image 3: The Robbins TBM was designed with pockets in the roof shield, allowing it to install the McNally Roof Support System while boring.
Industry News, trenchless people, trenchless products
Expanded access and support for HDD rock tooling
PELLA, Iowa, February 15, 2018 – Two of the horizontal directional drilling (HDD) industry’s leading equipment and tooling manufacturers, Vermeer Corporation and Mincon Group PLC, have formed a distribution alliance to expand contractors’ access to quality rock tooling worldwide. As part of the agreement, Vermeer dealers are now the exclusive channel for Mincon HDD air hammer systems, HDD pull reaming hammers and HDD support equipment, including HDD support stations and oilers.
“Mincon has pioneered HDD rock drilling solutions and when paired with Vermeer drills are productive in hard rock environments,” said Jason Zylstra, product manager, Lifecycle at Vermeer. “With the responsive support provided by Vermeer dealers and quality Mincon tooling, contractors have everything they need to take on challenging rock bores.”
Mincon hard rock hammer systems utilize high-frequency cycle technology that aids in the faster removal of drill cuttings from the bit face while providing the smallest possible chips. This design also improves steering capabilities and causes less vibration in the drill string.
For more information about Vermeer HDD equipment and Mincon HDD tooling, please consult your local Vermeer dealer.
ABOUT VERMEER
Vermeer Corporation delivers a real impact in a progressing world through the manufacture of high-quality tree care, environmental, underground construction, surface mining, and agricultural equipment. With a reputation for durability and reliability, that equipment is backed by localized customer service and support provided by independent dealers around the world. To learn more about Vermeer Corporation, products, the dealer network and financing options, visit Vermeer.com.
ABOUT MINCON
Mincon Group PLC was founded in 1977 in Shannon, Ireland. Mincon manufactures and distributes a range of precision engineered hard rock drilling tools for a variety of industries including mining, exploration, waterwell, geothermal, construction, horizontal directional drilling, oil-gas and energy. Mincon Group PLC has a worldwide presence with offices in Ireland, UK, Sweden, Finland, USA, Canada, Australia, South Africa, Namibia, Tanzania, Senegal, Chile and Peru. For more information about Mincon Group PLC, visit Mincon.com.