Blog, Industry News, trenchless projects
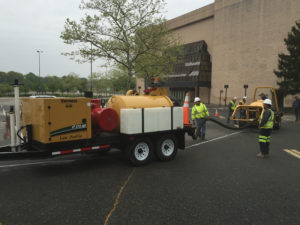
OKAHUMPKA, Fla., February 24th, 2016 – Micro Trenching is one of the installation methods being utilized by contractors to bring fiber networks to consumers. Micro Trenching is an installation method in which a narrow and relatively shallow trench is cut, usually on an asphalt roadway. Trench dimensions can range from .75 to 2.24 inches wide and 8 to 16 inches deep. While cutting, a vacuum system connected to the cutter wheel cleanly diverts and transports debris away from the worksite. Once the conduit is laid, the trench is backfilled with a grout compound.
Advantages of Micro Trenching include minimal cutting width that boosts installation production, reduce costs of backfill, shallow depth placement which helps avoid encounters with existing utilities and jobsite cleanliness thanks to the vacuum spoil that removes debris.
Vac-Tron Equipment has gone one step further in the cleanup process by developing a solution to micro trenching using a specialized in-tank filter (patent pending) inside the vacuum excavation unit’s debris tank. In most cases, the in-tank filter eliminates the need to add water to the micro trenching process and eliminates excessive material from reaching the cyclone separator. By using this filter, it will reduce the cleanup time during the trench run because there will be no need to stop and cleanout the cyclone or unclog the exit hose from debris tank due to caked material. Ultimately this will increase overall efficiency onsite.
David Donohue of Vermeer Mid Atlantic says “The Vac-Tron LP 573 SGT is the ideal vacuum for micro trenching, the high cfm’s and low noise output made communication and productivity simple.” David and Pfeiffer Enterprise Inc were demonstrating Vermeer’s micro trenching equipment and Vac-Tron’s LP SGT high cfm unit in Glen Bernie, MD in this photo.
For more info visit www.vactron.com or call Vac-Tron at 1-352-728-2222.
Blog, Industry News, trenchless projects
The Ontario Public Works Association (OPWA) 2016 Project of the Year: Environment, Greater than $50 Million Category was awarded to project owner, Regional Municipality of Halton along with lead consultant, Dillon Consulting Limited, consultant, R.V. Anderson and contractors; Dibco Underground Ltd and Varcon Construction Corporation for the Boyne Trunk Sanitary Sewer project. The awards luncheon was held on January 26 during the 2017 OPWA Annual Conference.
The South Halton Water and Wastewater Master Plan Update identified the need for a trunk sanitary sewer that could provide service for approved growth and future development within the Halton region. Dillon has been assisting Halton with contract administration and field services during construction starting in January of 2014 through July of 2016.
Congratulations to Halton Region Project Manager and NASTT Board Member, Brenda Kingsmill, and the rest of the crew on the success of such a large undertaking!
Blog, trenchless people, trenchless projects
Recently, 12 students from NASTT’s Student Chapter at UMASS Lowell attended a Horizontal Directional Drilling (HDD) site visit on location with Liberty Utilities in Somerset, Massachusetts. The students observed an HDD river crossing project. A safety briefing was held and all the necessary PPE was donned prior to the students entering the job site.
Everyone in attendance thoroughly enjoyed the visit and found it to be very educational on the HDD process and how trenchless technology is used in utility work.
Many thanks to Liberty Utilities for hosting the students and helping to educate the future of trenchless!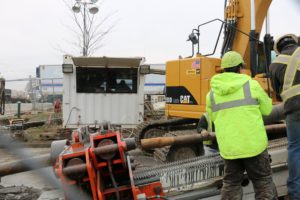
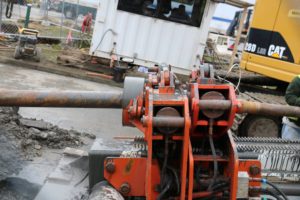
Blog, Industry News, trenchless projects
Rock Machine surmounts challenges on High-Cover Los Condores HEPP
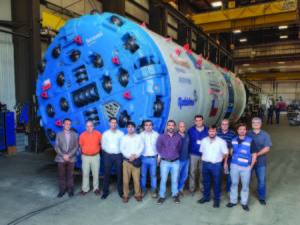
Project officials and Robbins team members celebrate the impending launch of the Double Shield TBM on 10.4 km (6.4 mi) of tunnels for the Los Condores Hydroelectric Project.
Chile’s Los Condores HEPP is a high cover, hard rock challenge, with 500 m (1,640 ft) of rock above the tunnel and a high-altitude jobsite 2,500 m (8,200 ft) above sea level. As of January 2017, a 4.56 m (15.0 ft) Robbins Double Shield TBM had completed boring its 900 m (2,950 ft) long access tunnel and was well on the way to boring the first section of headrace tunnel. The machine embarked on its journey on May 27, 2016, and has since excavated over 1,300 m (4,270 ft) of tunnel in total.
The journey to machine launch was an arduous one, requiring shipment of TBM components and vehicle transport on unpaved, mountainous roads. Contractor Ferrovial Agroman is responsible for the intake tunnel at the Los Condores Hydroelectric Project, and was well aware of the challenges associated with machine launch: “The location of the work is a big constraint due to its rugged terrain and geographical location in the Andes. With all this, we are anxious to perform work in an efficient manner,” said Pello Idigoras, Tunnel Production Manager for Ferrovial Agroman.
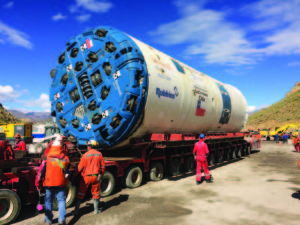
As of January 2017 the Robbins TBM had completed the 900 m (2,950 ft) long access tunnel and was boring its first section of headrace tunnel at rates of up to 25 rings per day.
The jobsite, located 360 km (224 mi) south of Santiago, Chile, is part of a new 150 MW power plant and intake tunnel. The Robbins Double Shield TBM is boring two sections of the intake tunnel, the first measuring 6 km (3.7 mi) and the second measuring 4.4 km (2.7 mi). A section between the two tunnels will be excavated by drill and blast to connect them, making the intake tunnel about 12 km (7.5 mi) in length. “This project brings an increase in energy production in the country, thus contributing to the overall improvement in the welfare of its citizens,” said Idigoras of the effect the completed hydropower project will have on surrounding areas.
The tunnel, located in the mountainous Maule Region of Chile, is being bored in two types of rock: sedimentary and volcanic. The rock has been tested at strengths up to 100 MPa (14,500 psi) UCS, with at least two fault zones—the first of which has already been traversed in rhyolite, andesite, tuff, and breccia. For Idigoras, the conditions are well-suited to Double Shield tunneling: “We have good quality medium to hard rock for Double Shield excavation overall,” he said. Despite that, some areas of challenging ground persist. To cope with the conditions, including steadily increasing water inflows at rates of up to 3,500 l/min (925 gal/min), the contractor is utilizing cementitious grouting and chemical grouting with polyurethane and foam. Such ground conditioning techniques were anticipated and the Robbins Double shield was designed to effectively apply these techniques.
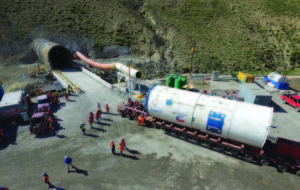
The challenging launch of the Robbins TBM at the remote jobsite 2,500 m (8,200 ft) above sea level.
As the TBM excavates, it is lining the tunnel with 250 mm (10 in) thick, 1.2 m (3.9 ft) long concrete segments in a 4+1 arrangement. The machine is currently progressing at a rate of up to 25 rings per 20 hours of boring. Crews are operating in two 10-hour shifts with one 4-hour shift dedicated to maintenance. Idigoras sees the TBM performance and completion of the access tunnel as huge project milestones, though much work remains to be done. “After many months working in engineering, manufacturing, installation, and commissioning, we are proud to see this result. It would be impossible to name all the people who participated in this project thus far but they, as a whole, have managed to get the TBM started digging and boring well.”
Blog, Industry News, trenchless products, trenchless projects
Swiftly-Assembled Machine to bore Emergency Water Supply Tunnel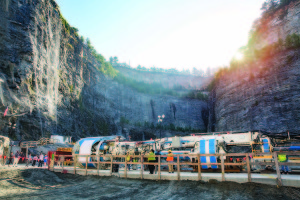
After an Onsite First Time Assembly (OFTA) lasting just 2.5 months, Atlanta Georgia, USA’s newest TBM, dubbed “Driller Mike”, made its initial startup on October 13, 2016 and ramped up to full production two weeks later. Atlanta’s Mayor Kasim Reed and city officials gathered with local and national media to celebrate the occasion. The 3.8 m (12.5 ft) diameter Robbins Main Beam TBM is now boring the 8.0 km (5.0 mi) Bellwood Tunnel after being walked forward 100 ft into a starter tunnel. The Bellwood Tunnel path will travel from an inactive quarry and run below a water treatment plant and reservoir before ending next to the Chattahoochee River.
The project was green-lighted by the City of Atlanta’s Department of Watershed Management due to the city’s
current emergency water supply shortage. The PC/Russell JV, the project’s construction manager at risk, sub-contracted with the Atkinson/Technique JV to operate the TBM and will oversee construction of various intake and pumping shafts as well as final lining operations. The project is of utmost importance for the City of Atlanta, explained Bob Huie, Sr. Project Manager for the PC/Russell JV. “Right now, the downtown area’s emergency water supply is approximately three days. With the tunnel the supply will increase to between 30 and 90 days. To be a part of the city’s emergency water supply solution is huge. This tunnel will protect the city for a very long time.”
With the tunnel on the fast track, swift TBM assembly was key. The OFTA process involved coordination by multiple
crews at the large quarry site. “The OFTA went very well. The overall assembly process was well organized and supervised by the Atkinson/Technique JV and Robbins. We had a good team of folks to put it all together,” said Huie. He continued: “This is a unique job where there’s a lot of people with a variety of backgrounds, but everyone came together to make the OFTA happen.”
The Robbins TBM is now excavating in granite, with at least 300 m (1,000 ft) of zones in three separate areas that will require continuous probing. In a section directly below an existing reservoir, monitoring will be particularly crucial to ensure no water inflows occur. The Robbins machine will also be required to negotiate several curves: “We have one curve in the first 300 m (1,000 ft) and the main 370 m (1,200 ft) radius curve is 1,800 m (6,000 ft) in. We plan to do short TBM strokes in this section—about 20 cm (8 inches) to 30 cm (1 ft) shorter than normal to get through the curves,” said Larry Weslowski, Tunneling Superintendent for the PC/Russell JV.
Excavation is scheduled to be completed in the first quarter of 2018. After final lining, the tunnel will be filled with
water and the quarry site will become Atlanta’s largest reservoir and park, totaling hundreds of acres. While the park site is a bonus for residents, the water storage capacity it will provide is critical. Nearly 1.2 million customers, including 200,000 passengers who pass through the world’s busiest airport every day, count on the water supply each time they turn on the tap. “If the city were to lose water supply for a day, the estimated economic impact would be at least USD $100 million per day. If you consider that this is a USD $300 million project, that seems a pretty good investment in comparison to what could happen,” said Huie.
Image 1: The Robbins Main Beam TBM, dubbed “Driller Mike”, was launched on Atlanta, Georgia, USA’s Bellwood Tunnel in October 2016.
Image 2: Robbins Field Service stand proudly in front of the completed Main Beam TBM after an Onsite First Time Assembly lasting just 2.5 months.
Image 3: The 3.8 m (12.5 ft) diameter Robbins Main Beam TBM will bore the 8.0 km (5.0 mi) Bellwood Tunnel through granite rock with potential zones of water inflows.
Image 4: Atlanta Mayor Kasim Reed (left) and Atlanta City Councilman Andre Dickens (right) attend the TBM’s launch ceremony to kick off the Bellwood Tunnel excavation.
Desiree Willis
Technical Writer
Email: willisd@robbinstbm.com
Direct: 253.872.4490
Blog, Industry News, trenchless people, trenchless products, trenchless projects
Highly Anticipated Photo Finish wraps up Tunneling at Massive Metro
On September 28, 2016, Bangalore’s last TBM for the city’s metro rail project broke through, marking the end of
TBM tunneling on the Namma Metro phase 1. The Robbins-operated machine, known as “Krishna”, bored a 750 m (2,460 ft) drive through challenging conditions between Chickpet and Majestic stations. Cleanup and final commissioning of the tunnel will be completed in 2017, and is the last obstacle before owner Bangalore Metro Rail Corporation Ltd. (BMRCL) can open the Malleswaram-Majestic link. The TBM’s sister machine, “Kaveri”, completed a parallel tunnel in June 2016.
The success follows a gauntlet of challenges on the two tunnel sites. Due to severe delays on the original tunnel drives, Robbins was approached and asked to take over the operations of the remaining two competitor-manufactured TBMs in February 2015. After obtaining agreement from the project owner and the contractor, Robbins took over the responsibility for all aspects of the underground operations. “We provided a team of over 60 staff including TBM operators, TBM technicians, ring builders, a grouting team, and more. We were also responsible for running surface installations and equipment such as the grout batching plant, gantry cranes and power supply. Contractor Coastal Projects Ltd. (CPL) provided a team of people including surveyors, QC engineers, and loco operators who reported directly to our site management team,” explained Jim Clark, Projects Manager for Robbins India. 
The Robbins crew carried out tunneling operations while the Chickpet station was being constructed around them to mitigate delays incurred before they took over project operations. The project’s most difficult challenges included a low overburden and unconsolidated ground along the alignment, and the discovery of several uncharted wells directly on the alignment. Difficult ground frequently prevented proper pressurization during cutting tool replacement, requiring a grout solution to be pumped in to fill voids and left to cure. Initially the curing process took up to 36 hours, but with improved application methods this was reduced to a 12-hour curing time.
Another challenge involved the sensitive building structures along the tunnel path. Issues with surface vibration, explained Clark, required that cutterhead speed be limited to 1.8 RPM during the day shift and 1.2 RPM during the night shift. Despite the obstacles, the TBMs advanced at rates of up to 50mm (2 in)/min in highly weathered rock.
“This is an industry first, wherein a TBM manufacturer has utilized their in-house expertise and knowledge to take on this level of responsibility for a project,” said Clark, addressing the magnitude of the successful breakthroughs. “The fact that it was ‘a first’ and we were successful in bringing this high-profile project back on track is a great achievement for The Robbins Company.”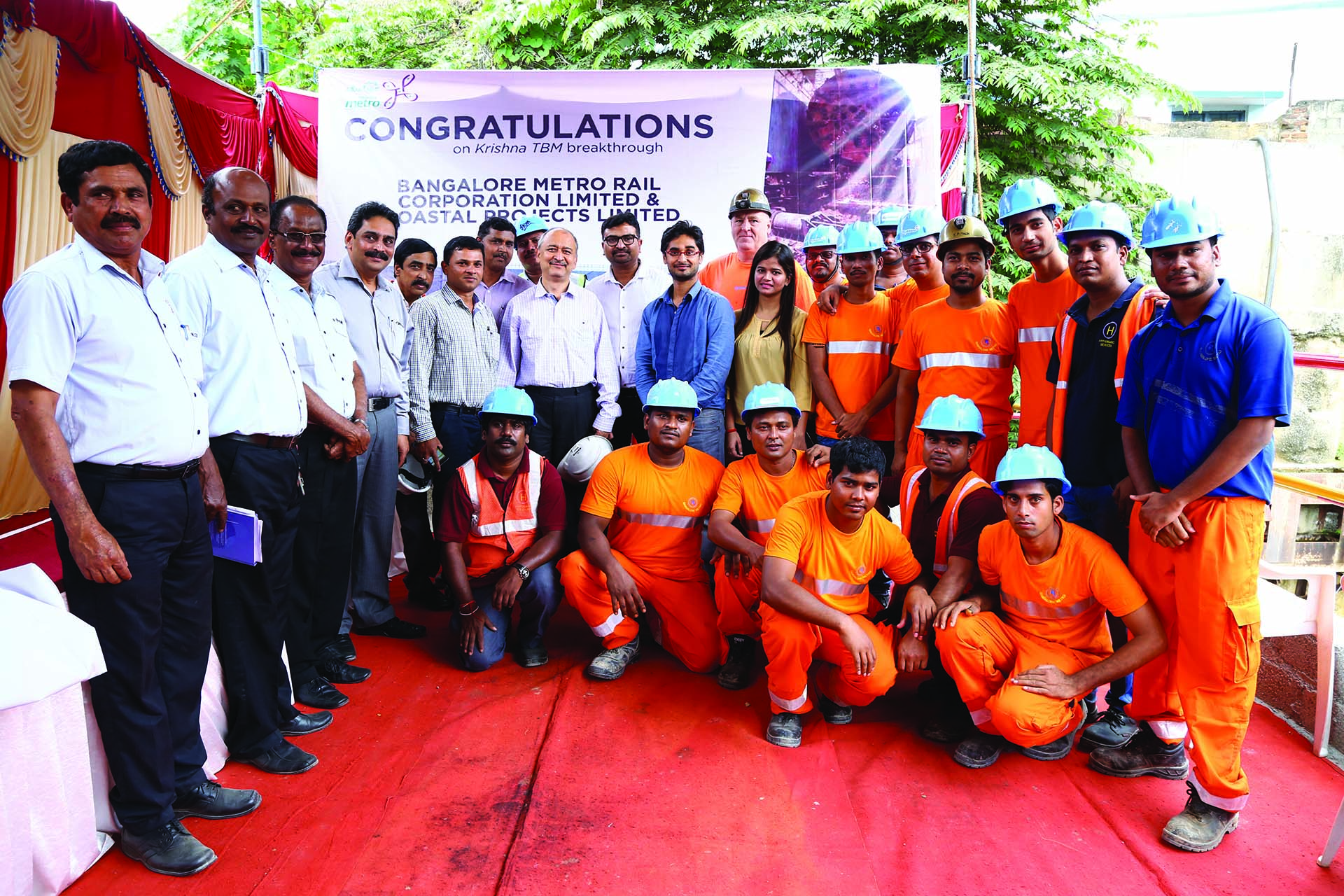
Now that tunneling is complete, the North and South runs of the Namma metro will be connected–a line that, once in service, will carry an estimated 40,000 passengers daily. It is anticipated that Phase One of the metro will be opened in its entirety in 2017.