Blog, Industry News, trenchless people
The South Central Chapter was established in 2015 to serve the members of NASTT from Oklahoma, Texas and the south central area of the United States. The Chapter is holding their second event on June 20 at the University of Texas, Arlington. This year we are excited to announce that the Chapter is also offering a student scholarship of $1,500!
Completed applications will be reviewed by the NASTT South Central Chapter board members. Selections will be based on academic achievement, demonstrated leadership, honors achieved, work experience, goals/aspirations, and interest stated in the underground construction industry. Completed applications must be received by 11:59 p.m. on June 1, 2017. Completed applications must be submitted to smatthes@ditchwitch.com. The scholarship award presentation will take place at the annual NASTT/UTA South Central Chapter event in Arlington, Texas on June 20, 2017.
For all the details on the scholarship, click here.
For details on the conference, please visit the conference website.
Blog, Industry News, trenchless projects
April 4, 2017 – LAKE MILLS, Wisc. – HammerHead Trenchless Equipment, a Charles Machine Works company, has introduced the new HammerHead Roughneck™ R200, the first two-inch rock hammer engineered specifically for horizontal directional drilling applications. The R200, the smallest pneumatic rock hammer of HammerHead’s Roughneck line, is designed to expand the capabilities of small utility drills allowing 7000- to 10,000-ton class directional drills to effectively drill through solid rock as well as other difficult soil conditions.
The R200 rock hammer was made to be the most efficient system available to HDD contractors in communications, gas, electrical and water service installations. The R200 model drills a 3.125-inch pilot hole.
“The R200 allows you to use a small drill on jobs you couldn’t before. If you needed to drill through solid rock, you’d have to bring a large drill to supply enough power which requires more labor, more support equipment, and more time to complete the job. With the R200, contractors can save money by maximizing the capabilities of a small drill,” explained Josh Hood, HammerHead HDD product manager. “When you’re working in small spaces or drilling short distances such as under a road bed, it makes sense to use a small drill and now you can, regardless of soil conditions.”
A key feature unique to the R200 rock hammer is the electronically-controlled air flow. With the touch of a button, the operator can adjust the air flow from open to closed and anywhere in between which allows them to manage the power of the hammer on the fly. This feature is critical in situations where soil conditions change abruptly. The ability to reduce or increase power quickly prevents costly interruptions during the bore.
The HammerHead R200 air hammer shares similar features with the other models of the HammerHead Roughneck line. The Roughneck R400, R500 and R600 are recognized as some of the most trusted and productive pneumatic rock hammers available for HDD applications. All four models are capable of drilling at rates of up to 150-feet per hour with exceptional steering performance. Additionally, all Roughneck rock hammers feature side-load high-flow housing, a patented pull back kit system and a lightweight control station.
Serviceability is a key design feature in all HammerHead pneumatic hammers and the R200 is no exception. Patented spanner wrench holes in the front and rear of the hammer reduces the number of breakout jaws required when performing maintenance or changing out rock bits.
The HammerHead R200 rock hammer is offered as a complete system to get contractors up and running. The system includes a R200 Roughneck air hammer, offset and angled offset bits, patented pullback kit, control station/oiler with tethered electronic remote control, hydraulic breakout tooling, 2.5-inch universal high-flow housing, and a conversion kit specific to the drill.
The R200 rock hammer system is available from HammerHead Trenchless Equipment or from authorized dealers, worldwide. Authorized dealers can be found on the web at www.hammerheadtrenchless.com or by calling 800.331.6653. (International: + [1] 920.648.4848).
Blog, Industry News, trenchless projects
NASTT’s South Central Regional Chapter is hosting their second event on June 20!
If you’re in the South Central region, plan to attend the Trenchless Technology and Pipe Conference for Water, Sewer, Oil, and Gas Applications: TTP 2017, sponsored by South Central Chapter of NASTT.
Abstracts for presentations are currently being accepted for the event.
The abstract submission deadline is May 1 and final presentation submission deadline is May 31.
Abstract information (paper is not required):
Abstracts should be submitted in the following format:
- The abstract should not be more than 500 words.
- Please type all text in 12 point Times New Roman.
- Name of the Author/s should be included, with the presenting author’s name underlined.
- Please include the full contact details of the presenting and corresponding author(s) (Address, Phone, Fax, and Email).
Abstracts should be submitted by email, as an attached document, in MS Word format (.doc or .docx) to CUIRE at cuire@uta.edu. Abstract should be submitted by May 1, 2017.
Get all the abstract details on the conference website here.
Be a part of this growing chapter’s history and network with your industry peers!
Blog, Industry News, trenchless products
THOMPSON, CONNECTICUT USA, April 4, 2017
Numa, the world’s leading drilling technology provider, offers one of the largest ranges of DTH rock drilling hammers and bits available in the industry today. The company boasts over 110 DTH products for drilling holes 3½ to 48 inches (89 – 1219 mm) in all types of conditions, applications, and industries.
Numa works with drillers on job sites around the world to support its products and gain first hand insight for advancing DTH product design. The company holds 13 patents, with more pending, for DTH equipment capable of drilling vertical, horizontal, and reverse circulation holes. Numa products are used in over 11 industries including construction, oil & gas, mining, quarry, geothermal, water well, and many more.
Numa’s wide range of DTH products includes:
SMALL HAMMERS AND BITS
Drills holes from 3-1/2″ to 10″ (89 – 254 mm) Numa offers eighteen different small diameter hammers for diverse drilling conditions. Built specifically for longevity and penetration rate, Numa’s Patriot® hammers and bits drill at high frequency and require less air. Even against high heads of water.
MID-RANGE HAMMERS AND BITS
Drills holes 7-7/8” to 20” (200 – 508 mm) Numa’s mid-range hammers and bits provide a combination of speed and life to excel against hard, abrasive and just plain nasty conditions. A simplified hammer design with less internal components promotes less vibration and smooth operation.
LARGE HAMMERS AND BITS
Drills holes 18” to 48” (457 – 1219 mm) Numa pioneered the large hammer industry and leads the market in performance and reliability. Our forward thinking designs have proven themselves again and again in demanding applications around the world.
REVERSE CIRCULATION HAMMERS AND BITS
Drills holes 5-1/4” to 36” (133 – 914 mm) Numa’s Reverse Circulation products have the unique ability to bring all cuttings up the center of the hammer and drill string to be safely collected at the surface, which is essential in today’s environmentally conscious society.
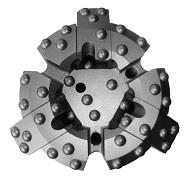
SUPER JAWS® BITS
Drills holes 5-1/2” to 42” (457 – 1066 mm) Super Jaws provides superior performance for simultaneous drilling and casing in hard rock and overburden formations. Wings extend out to drill a full diameter hole then retract to bring all tooling to the surface. No expensive tools are left in the hole and no casing teeth are required.
ABOUT NUMA
Numa provides the world’s leading drilling technology with over 110 DTH Hammer and Bit products serving 11 different industries. Our products are capable of drilling vertical, horizontal, and reverse circulation holes from 3½ to 48 inches (89 – 1219 mm) in diameter and are used in 105+ countries. We have built our customer-centric reputation on providing the highest value in products, performance and personal service available in the rock drilling industry.
Blog, Industry News, trenchless products
Vision LX, FLX2 and GX2 models provide fast, easy and accurate utility locates
GREENVILLE, S.C. — March 22, 2017 — McLaughlin revealed a new line of underground utility locators at 2017 CONEXPO-CON/AGG, the industry’s largest trade show held in Las Vegas. The Vision locators combine proven McLaughlin technologies to ensure accuracy with new features to help contractors find underground utilities more efficiently.
The Vision product line includes three models: the LX for utility contractors, the FLX2 with fault finding capabilities for power companies and secondary power contractors, and the premium GX2, designed with professional locators in mind.
“Utility contractors face a crowded underground infrastructure, unmarked utility lines and increasingly strict regulations, which makes accurate, timely locating more important than ever,” said Jeff Wage, vice president of sales at McLaughlin. “With the addition of the Vision product line, McLaughlin has an underground utility locating solution for everyone from the new utility contractor who is just starting out to the professional One Call contractor.”
Vision LX locator
The Vision LX locator has a streamlined design and simple user interface. For example, the LX combines the peak locating screen and null locating screen into one display. This allows the user to capitalize on the benefits of both functions — the accuracy of the peak mode and the user-friendliness of the null mode — without toggling back and forth between screens.
Other improvements to the display include an automatic depth and current measurement index, which automatically appears when the locator is positioned over a utility line, and a new compass icon. The compass automatically calculates the peak signal and visually informs the user of the direction of the utility path, making it easier to locate the entire line.
Vision FLX2 locator with fault finder capabilities
The Vision FLX2 has the same features and functions as the Vision LX locator plus secondary and sheaths fault-finding capabilities. Designed with power companies and secondary power contractors in mind, the FLX2 allows contractors to quickly and accurately pinpoint the location of faults in power and telecommunications cables.
Once the locator is connected to the utility line, a contractor can use an A-frame transmitter to find the fault. The contractor places the A-frame transmitter’s prongs into the ground, and the reading is sent to the receiver. If the receiver shows the signal is on the right side of the screen, the contractor proceeds forward along the utility line. If the receiver shows the signal is on the blue side of the screen, the contractor has passed the fault and is alerted to back up. Using this process, a contractor can narrow the location of the fault to within a few inches.
When used for its traditional locating capabilities, the FLX2 has five active frequency modes. Lower- frequency modes provide more accurate locates over longer distances; high-frequency modes use a powerful signal to get through resistant lines, like cast-iron pipes. The FLX2 allows the operator to adjust the frequency based on the needs of the utility line, which provides a more accurate locate.
Vision GX2 locator
The GX2 is the most powerful locator in the Vision product line. Using a 7-watt transmitter — instead of the standard 5-watt — the GX2 allows contractors to push the locating signal farther, which is ideal for long fiber runs or gas distribution projects with tracing wires.
To further extend the signal, the GX2 uses a dual frequency mode — that does not require Bluetoothâ — to simultaneously inject 9.5 kHz and 38 kHz signals into the utility line. When the 38 kHz signal begins to fade, the operator can use the receiver to toggle to the 9.5 kHz frequency and can continue locating.
Because some fiber providers use a custom frequency, the GX2 gives contractors the flexibility to program other frequencies into the locator for added jobsite efficiency.
McLaughlin-exclusive features
McLaughlin strives to provide the most accurate locating tools in the industry. While each Vision locator has features that make it unique, some McLaughlin-exclusive technologies come standard on all three models.
Semiautomatic and manual gain adjustment
Gain adjustment refers to the receiver’s sensitivity to the magnetic field emitted by a utility line.
“The benefit of the semiautomatic gain is that it’s a very precise method of locating — especially in congested areas — and the technology is exclusive to McLaughlin,” says Wage. “Because manual gain is a more commonly used method of locating, some contractors are hesitant to try the semiautomatic gain feature.”
All three Vision locators offer dual functionality, which means contractors can engage the semiautomatic gain on congested, urban jobsites where signal distortion is a common challenge, and use the manual gain method when working in less congested areas.
Three antennas
While competitive products use two antennas to measure depth readings, McLaughlin Vision locators use three. With the push of a button, the locator simultaneously takes depth readings from all three antennas and averages the measurements for a more accurate reading. For added durability, the antennas are rubber mounted inside the injection-molded locator case so they can stand up to tough jobsite conditions.
Inductive clamp
To help contractors be more efficient on the jobsite, the Vision locators have a waterproof inductive clamp. This means the Vision locator can lay on or partially grip the utility and produce an accurate reading, unlike competitive locators that require the clamp to fully encircle the utility, which creates extra labor for contractors.
The Vision locators come with a three-year warranty and weatherproof guarantee and are sold exclusively through the McLaughlin sales channel. To learn more, visit mclaughlinunderground.com or
email McLaughlin at mmole@mightymole.com.
Blog, Industry News, trenchless people, trenchless products, trenchless projects
Specialized TBM will work below the Hudson River on the Delaware Aqueduct
Robbins has completed the manufacture and testing of a unique tunnel boring machine that will be used to repair the longest continuous tunnel in the world. The TBM will be used to overhaul a section of New York City’s Delaware Aqueduct, a 137 km (85 mi) long tunnel that delivers about 50 percent of the City’s drinking water each day. Over the span of two days in February, representatives from the owner New York Department of Environmental Protection (NYDEP), consultant McMillen Jacobs (MJ), and JV contractor Kiewit-Shea Constructors (KSC) traveled to the Robbins facility in Solon, Ohio to witness the Factory Acceptance Testing of the custom tunnel boring machine.
The Robbins Single Shield TBM will bore a tunnel to replace a 3.8 km (2.4 mi) stretch of the Delaware Aqueduct. The Delaware Aqueduct currently leaks about 75 million liters (20 million gallons) of water per day into the Hudson River. Investigations of the Delaware Aqueduct dating back more than a decade revealed cracks in the tunnel lining. While several inspections with an automated underwater vehicle showed that these cracks were stable, it was determined they could not be fixed from within the existing tunnel. New York City then decided that a new tunnel would be built under the river to bypass the leakage.
To build a bypass tunnel around the aqueduct’s leaking section, Robbins manufactured the 6.8 m (21.6 ft) diameter Single Shield TBM to safely seal against pressures up to 30 bar, and to operate in variable hard rock conditions. The Delaware Aqueduct was completed in 1944. During its original construction, work crews documented groundwater inflows of 7.5 to 15 million liters (2 to 4 million gallons) per day. Because this particular section of the tunnel lies 183 m (600 ft) below the Hudson River, the inflows are under immense head pressure and thus require the unique tunneling technology.
Due to the challenges presented by the Aqueduct Repair, such as difficult geology and considerable water inflows, the TBM had to be designed accordingly. Difficult Ground Solutions (DGS) features, including powerful drilling, grouting, and water inflow control systems have been incorporated into the machine’s design to overcome the expected challenges. “One unique feature of this TBM is the closeable bulkhead, which allows the excavation chamber to be sealed off,” said KSC Tunnel Manager Niels Kofoed. “We expect this to be a key feature in the event that groundwater flows (shunt flows) from the excavated portion of the tunnel cause washout of the annulus grout. Once the bulkhead is closed the groundwater flows are stopped and secondary grouting of the precast liner can be performed, effectively cutting off the flow path of the shunt flows.”
Robbins Project Manager Martino Scialpi further noted that, “the TBM was designed with a 9,500 liter/min (2,500 gallon/min) dewatering capacity. The machine is equipped with two drills in the shields for drilling through the head in 16 different positions and a third drill on the erector to drill through the shields in an additional 14 positions. Drilling and pre-excavation grouting will be a routine job to control and minimize water inflows.” In addition, water-powered, high pressure down-the-hole-hammers will allow for drilling 60 to 100 m (200 to 330 ft) ahead of the machine at pressures up to 20 bar if necessary.
In order to provide access to launch and retrieve tunneling equipment, two deep shafts were constructed in the towns of Newburgh and Wappinger, New York, where the bypass will begin and end. The project site itself poses challenges to the assembly and launch of the TBM because of the limited space available.
Robbins worked closely with KSC to ensure that TBM components were designed and sized so all could be lifted with the contractor’s hoist system and fit down the narrow, 270 m (885 ft) deep shaft. Once assembled, the machine is expected to begin boring in autumn 2017.
Image: The Robbins crew, contractor KSC, and project officials stand proudly in front of the Robbins Single Shield TBM that will tackle hard rock and high water inflows in New York State.