Industry News, trenchless people
Robert H. Westphal
5/4/1944 – 3/31/2020
A memorial service celebrating the life of Robert H. “Bob” Westphal will be held at 3 p.m. on Friday, Oct. 30, at Faith Lutheran Church in Fond du Lac, WI.
Bob passed away on March 31, 2020. He is remembered for his many contributions to Michels Corporation, and to the pipeline and trenchless construction industries. An industry icon, Bob devoted 55 years of his life to Michels.
A memorial service remembering the life of Bob Westphal will be held at 3 p.m. on Friday, Oct. 30, at Faith Lutheran Church, 55 Prairie Road, in Fond du Lac, WI.
Friends and family are invited to attend the service. Based on current rules for public gatherings, masks will be required. Bob’s family will meet with guests immediately following the service.
In lieu of flowers, memorials can be sent to The Robert H. Westphal Memorial Scholarship Fund. To contribute, send checks to Michels Scholarship Fund, Attn: Nate Redig, P.O. Box 128 Brownsville, WI 53006. Enter Robert H. Westphal Memorial on the memo line.
Memorials may also be sent to Faith Lutheran Church and School, 55 Prairie Road, Fond du Lac, WI 54935 in memory of Bob.
Blog, Industry News, trenchless products
October 2020—Crosslink Technology Inc. has developed PIPE (Pressure Infused Protective Epoxy) Cure, a fast, easy, and cost-effective way to completely rehabilitate the inside of underground pipes, specifically laterals.
PIPE Cure provides a less destructive and less costly alternative to digging out underground pipes for repair, and it also provides unique advantages over the traditional CIPP (Cure in Place Pipe) restoration products.
While CIPP is a widely used trenchless technology, it can use unsaturated styrenated polyester resin, which may give concern to volumetric shrinkage, odor, adhesion/strength, and sensitivity to temperature.
Crosslink Technology Inc.’s PIPE Cure has been formulated to have:
- Excellent strength and adhesion (flexural modulus of over 500,000 psi and flexural strength of 7000 psi)
- Exceptionally low linear shrinkage (0.0001 inch/inch)
- No odor
- Ability to cure in underground temperatures as low as 10°C/ 50°F (without a heat source AND regardless of the ambient temperature when it was mixed)
- Excellent wetting out of fiber in the liner
- Better health and safety rating than styrene
With Crosslink Technology’s PIPE Cure, you will get a safe, easy, budget-friendly cure for your underground pipe repair problems.
About Crosslink Technology Inc.:
At Crosslink Technology Inc., we deliver innovative thermoset solutions which make a real difference to our customers’ business. We produce a wide range of Epoxy and Polyurethane applications and Custom-cast Electrical components which lower processing costs, improve product quality, and boost profitability.
Since 1981, we have dedicated ourselves to staying on the leading edge of technical innovation, creating solutions tailored to customer needs and processes.
Today our dedicated and knowledgeable workforce produces applications embraced by companies in the United States, Mexico, Australia, and the Far East.
For More Information:
Christa Foy
Product Manager
Crosslink Technology Inc.
6380 Viscount Rd.
Mississauga, ON L4V 1H3 Canada
Cell: (437) 244-7620
Industry News, trenchless projects
Resilient TBM completes Bahçe-Nurdaği Railway
On July 24, 2020, a jubilant ceremony marked a milestone for southern Turkey’s arduous Bahçe-Nurdaği High-Speed Railway Tunnel. The first TBM-driven portion of tunneling using an 8.0 m (26.2 ft) diameter Robbins Single Shield machine is now complete. The 8.9 km (5.5 mi) long TBM tunnel was no easy bore, as it was excavated through some of the hardest and most abrasive rock ever encountered in the country.
“We are proud of the TBM crew who acted rapidly and were well organized to overcome the challenging ground conditions with a unique Single Shield TBM for the completion of the first tube of the Bahçe-Nurdağı Railway Project,” said Deniz Sahin, TBM Chief for contractor Intekar Yapi A.Ş.
Ground conditions during tunneling ranged from abrasive, interbedded sandstone and mudstone with quartzite veins to highly weathered shale and dolomitic limestone. The TBM encountered rock measuring between 136 and 327 MPa (19,700 to 47,400 psi) UCS. Water ingress with fines was expected in fault lines and shear zones affected by the East Anatolian Fault. “The TBM became stuck in three different fault zones, which we got through by building bypass tunnels. In smaller fault zones, we encountered excessive material flow and the TBM had to be stopped, while ground had to be stabilized with chemical injections while we cleaned the cutterhead,” said Sahin. Water inflows of 10 liters per second on average were removed using a dewatering system.
The majority of tunneling, said Sahin, was in metasandstone with quartz, with an average of 220 MPa (31,900 psi) UCS and a Cerchar abrasion value of 3.87. In such regions, the TBM’s 19-inch back-loading disc cutters had to be changed frequently and there was high vibration. Despite the challenges, Sahin was impressed by the machine’s overall capacity: “The Robbins Single Shield TBM’s motor power, hydraulic power and cutterhead torque were quite strong. The secondary ventilation and air suction systems inside the TBM were powerful. The connections between the gantries, scaffolding systems, walkways and working areas were good.”
The TBM ultimately achieved up to 456 m (1,500 ft) per month, a result achieved with the help of a Robbins continuous conveyor system for muck removal. “The electric motor and gearbox capacity of the conveyor system was quite enough for a 10 km (6.2 mi) tunnel and we had no failure on them. The conveyor performed well even under excess material and the whole system was quite robust,” said Sahin.
The owner, Turkish State Railways Directorate (TCDD), is aiming to overhaul the railway connection in southeastern Turkey by providing a shorter, faster route in one of the country’s busiest railway corridors. The new rail line between the towns of Bahçe and Nurdağı includes two parallel 9.8 km (6.1 mi) tunnels being excavated by both NATM (850 m / 0.5 mi) and TBM (8.9 km / 5.5 mi).
Image 1: Contractor Intekar Yapi A.Ş celebrated the breakthrough of the Robbins Single Shield TBM on July 24, 2020 in southeastern Turkey.
Image 2: The Robbins TBM bored an 8.9 km (5.5 mi) long tunnel through some of the hardest rock in Turkey, measuring up to 327 MPa (47,400 psi) UCS.
Image 3: The new rail line between the towns of Bahçe and Nurdağı includes two parallel 9.8 km (6.1 mi) tunnels being excavated by both NATM (850 m / 0.5 mi) and TBM (8.9 km / 5.5 mi).
Image 4: The Robbins TBM excavated interbedded sandstone and mudstone with quartzite veins, highly weathered shale, and dolomitic limestone using back-loading 19-inch disc cutters.
Industry News, trenchless people
CEO, second-generation owner, Dan Liotti announces retirement
Greenfield, Indiana — August 25, 2020 — Midwest Mole Inc., a premiere specialty underground contractor providing boring, trenchless tunneling and directional drilling services throughout the Midwest and beyond, has announced that CEO and second-generation owner Dan Liotti is retiring.
Ownership of the family business founded in 1982 by Len Liotti will be transferred to an Employee Stock Ownership, in which the company’s employees own shares. “It’s 100% employee-owned,” states Jason Miller, president. An ESOP is a kind of employee benefit plan, similar to a profit-sharing plan, providing advantages for growth and employee retention without alteration of the management structure.
The change of ownership is expected to be a seamless transition for clients and vendors, as the company continues to focus on providing cost-effective and environmentally friendly trenchless solutions, working safely and creating a welcoming work environment.
Midwest Mole is considered a trenchless technology expert, tunneling under highways, railroads, buildings and airports on municipal and private sector projects, operating as either prime contractor or subcontractor. The majority of their work involves utilities or sewer, stormwater and water pipes.
To reflect these changes, Midwest Mole has refreshed its goals and mission statement and adopted new branding, which includes an updated logo and visual identity. The employee-owned company remains committed to long-standing industry relationships and delivering quality work in the demanding world of tunneling, building on their decades of experience to expand services geographically as part of their plan of growth for the future.
For more information, please contact David Howell at david@midwestmole.com.
Industry News, trenchless people, trenchless products
SewerAI secures $2 million in seed funding for its breakthrough technology
San Francisco, CA, August 3, 2020—SewerAI , a startup that uses artificial intelligence and computer vision to inspect, identify and analyze sewer infrastructure defects before they reach catastrophic levels, announced that it has secured $2 million in seed funding led by venture capital firms Builders VC and EPIC Ventures.
SewerAI was established by sewer infrastructure inspection technology veterans to address the
massive problem of aging pipe infrastructure—with over 6 billion feet of sewer pipe in just the
U.S. alone, approximately 3 billion feet are in need of repair or replacement. US municipalities
spend approximately $50 billion each year maintaining this infrastructure, mainly using manual
inspections, data delivered via physical disks, and desktop-based software. SewerAI harnesses
the power of artificial intelligence and computer vision, along with a cloud workflow platform to
automatically detect pipeline defects, allowing sewer inspections to be completed in a fraction of
the time with increased accuracy.
“The cost to state and local communities to maintain and repair aging pipes, and the cost of
system failures, are in the billions of dollars,” explained SewerAI CEO Matthew Rosenthal.
“Utility companies and engineering firms help to manage the problem of aging pipes by
deploying robotic cameras to identify defects, collecting tens of thousands of hours of video each
day that are manually reviewed and assessed in a painstaking and time consuming process. This
inspection process is typically slow, expensive, and inconsistent—not to mention subject to
human error.”
Matt Rosenthal and Bill Gilmartin have separately been working in the industry for more than 10
years and have a unique combination of technical capability and real-world operational
experience. They have prior experience and seeing the problems for 10+ years and that is what
led to this AI that is solving real industry problems.
SewerAI’s groundbreaking AI, cloud-based software AutoCode™ significantly enhances and
accelerates this sewer infrastructure inspections.
“With our technology, sewer inspection crews in the field can now change their workflow to
survey significantly more feet of pipe per day,” continued Mr. Rosenthal. “ Machine learning
training dataset consists of millions of feet of labeled video inspection data, all reviewed and
validated by our expert labelers. This training dataset grows every day, allowing SewerAI
AutoCode to gain intelligence with every foot of inspection processed through the SewerAI IMP.
As the data comes in, our clients save money, accelerate their work flows, and receive more
accurate asset information than ever before.”
This technological breakthrough is setting the stage for the wastewater industry to enter the 4th
technological revolution; creating an entirely new category of business in the process.
Mr. Rosenthal added, “The cost savings to utility companies and their customers that can be
achieved with our technology, coupled with the environmental and public health benefits
resulting from a modernized sewer infrastructure, are tremendously beneficial to our society.”
With over 860 billion gallons of raw sewage leaking into lakes, wetlands, rivers and oceans, the
dire environmental impact of a deteriorating sewer infrastructure makes the need for accurate,
fast, and cost-effective inspections all the more urgent.
Coupled with the SewerAI Inspection Management Platform® (IMP)—a web-based tool that
stores the inspection data and enables users to stream inspection videos, view reports, and access
data analytics and predictive models for risk assessment—AutoCode™ empowers asset owners
to move from expensive reactive maintenance activities to more cost-effective proactive asset
management strategies.
SewerAI’s mission is to challenge the status quo of infrastructure management by delivering
advanced technology that helps engineers plan repair projects, automate routine maintenance
schedules, and manage environmental compliance with unparalleled efficiency and accuracy. For
more information, visit http://www.sewerai.com/
Industry News, trenchless people
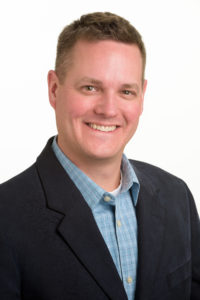
Lithos Engineering is thrilled to announce the addition of Richard (Bo) Botteicher, PE to their team. Bo brings over 20 years of experience in the underground infrastructure industry including extensive trenchless new installation and rehabilitation projects for the water, wastewater, reclaimed water, stormwater, industrial and power markets. Bo has been involved with multiple historical projects related to horizontal directional drilling (HDD), sliplining, and pipe bursting across the US.
Robin Dornfest, President of Lithos Engineering said, “Bo is a fantastic addition to the Lithos team and with his experience in trenchless rehabilitation and new installations, he will allow us to expand to meet the needs of the ever growing rehabilitation market. We have known Bo for many years and always had great respect for his tireless work in the trenchless world and are extremely excited that he has chosen Lithos as his new home.”
Bo is a registered professional engineer and has worked both on the design and commercial sides of the underground construction industry. He started his career designing municipal underground infrastructure and facilities, including new installation and rehabilitation projects. Bo spent the last 14 years working for a specialty trenchless pipe supplier, with the last four years as the General Manager of that business. Bo is very active with the North American Society for Trenchless Technologies (NASTT) and is a member of their Board of Directors.
“I want to thank Lithos for staying true to their growth mindset and entertaining the idea of adding me to their impressive group,” said Bo. “Working directly with the utilities, municipalities, contractors, engineers, and technology firms on the present and future challenges of the underground infrastructure industry is what I enjoy most – and I am looking forward to much more of this with the world-class Lithos Engineering team.”
Lithos Engineering is extremely excited about the expanded skill set that Bo brings to their team and the ability to better serve their clients now and in the future. If you want to reach out to Bo, please email him at Bo@LIthosEng.com
Lithos says, “Welcome aboard Bo!”