trenchless projects
Expansive Metro Project Will Provide Transportation Within Rapidly Developing City
On Tuesday, October 31, 2017, a 6.65 m (21.8 ft) diameter Robbins EPB TBM broke through at Chennai Metro, making this the third tunnel the machine has bored for the project and for contractor Afcons Infrastructure Ltd. The three separate bores for the EPB are part of an increasing trend, as many Robbins EPBs have been used on multiple tunnel drives with good performance. Robbins EPBs are built one third heavier than any other EPB on the market and are designed for 10,000 hours of usable life, making them ideal machines for use over many kilometers. “Robbins is known for designing resilient machines,” said Mr. Gopal Dey, Afcons Senior Manager. “For this project, we needed a machine that was specifically tailored to project conditions from soft clay to mixed ground with rock. Robbins EPB TBMs have unique design features that optimize the machine for the geology.”
After completing its original twin tunnels, the EPB was refurbished in preparation to bore its latest 1.8 km (1.1 mi) section. During refurbishment, the inner seal greasing system was changed from auto to manual mode and the foam nozzle system was modified. These changes optimized the machine for excavation in the highly variable mixed face conditions encountered in the first two tunnels.
The EPB was launched on February 3, earlier this year. According to contractor Afcons, the machine faced a major challenge right out of the gate. “When the TBM came out of the launching shaft, a few rings were erected and then the machine had to cross a live railway track, which meant there would be a possibility of ground settlement,” said Afcons Director, Mr. Manivannan. “At this stage, we had to closely monitor TBM face pressure and advance the machine at a uniform rate to ensure proper primary grouting.” The bore’s geology mainly consisted of clayey sand and about 60 meters (197 ft) of mixed ground.
“We [Afcons] chose this machine for this project due to the underground geology in Chennai, which continuously changes from soil to mixed ground,” said Mr. Dey. “We also liked that Robbins EPB machines are designed with active articulation to allow the machine to turn or steer with ease.” During active articulation, thrust cylinders react evenly against the entire circumference of the tunnel lining, even in a curve—a design that eliminates the problem of tunnel lining deformation. “This feature enabled the machine to negotiate through well-controlled conditions,” added Mr. Manivannan.
With all three tunnels, Robbins Field Service members were on location to assist and support as required. During the course of each bore, Robbins was there to advise Afcons on how best to maneuver through challenging ground and provide instruction for machine operation. The ability of the contractor and manufacturer to work well together, as Robbins and Afcons have throughout their contracts, was critical to the good advance rates. The result was a robust machine that advanced at rates of 80 mm (3 in) per minute in challenging conditions.
This latest tunnel connects multiple stations along the metro line, starting from Washermenpet through to Sir Theagaraya and to Kurukpet. The Chennai Metro Project will provide much needed transportation to a rapidly developing city.
Image 1: On Tuesday, October 31, 2017 a 6.65 m (21.8 ft) Robbins EPB made its third breakthrough at India’s Chennai Metro.
Image 2: Robbins and contractor Afcons celebrate the breakthrough and good performance of the EPB, which achieved rates up to 80 mm (3 in) per minute in mixed ground conditions.
Desiree Willis
Technical Writer
Email: willisd@robbinstbm.com
Direct: 253.872.4490
The Robbins Company
Industry News, trenchless projects
SANTA CRUZ ACCOMPLISHES EMERGENCY HORIZONTAL DIRECTIONAL DRILL FOR
LOMBARDI GULCH CROSSING
HDD provides a rapid and reliable way to replace aging steel pipeline
Overview
The City of Santa Cruz Water Department (SCWD) has long anticipated the need to assess, design and build a new pipeline system as part of the existing North Coast System (NCS) which delivers raw water to their water treatment plant. The existing NCS is a series of stream diversion structures and collection
conduits and includes approximately 16 miles of pipelines that are nearing, or have exceeded, their design life and must be replaced. The replacement pipeline is a series of phased projects and will provide a water delivery system that will be reliable for the next fifty years or more.
Phase 3 of the overall initiative included the replacement of 18,600 feet of primarily 24-inch diameter pipe using open cut methodology. Additionally, five trenchless crossings, one horizontal directional drill (HDD) crossing under sensitive environmental habitats and four horizontal auger bores crossing under California Department of Transportation and railroad right-of-ways were included in Phase 3.
In 2015, this phase of the NCS project had been designed but had not gone out to bid when a failure of a 1,200-foot critical section of the existing steel pipeline at the Lombardi Creek Crossing location prompted SCWD to schedule that section for immediate replacement. Site conditions at this location required replacing the pipeline using HDD installation methodology. Its location within the Wilder Ranch State Park elevated environmental concerns because the park has strong biological, scenic, cultural and recreational values.
The replacement of the Lombardi Creek crossing began in late 2015 after selecting the HDD Company from Granite Bay, California to be the contractor. The actual drill alignment length was approximately 1,300 feet with an elevation change of approximately 60 feet. Entry and exit angles were approximately 10 degrees. The final alignment was 25 feet below the bottom of the creek. 24-inch DR 18 Fusible PVC®
pipe was selected as the replacement pipe. Overall, the drill alignment and bore preparation took four weeks. While the bore hole was being drilled and reamed, the Fusible PVC® pipe was fused by Underground Solutions. Once the bore hole was prepared, the Fusible PVC® pipe was pulled into place,
a process that took approximately 8 hours. The replacement project took two months from mobilization to pressure test and the replacement pipe was placed into service after completion. This new segment will be tied into the new NCS Phase 3 pipeline when it is complete.
Project Manager Kevin Crossly stated, “The Lombardi Gulch HDD Undercrossing is the largest and longest installation of Fusible PVC® pipe to date for the City of Santa Cruz. The City was very pleased during all phases of the project with Underground Solutions which provided technical support solutions during design of the project. When the City experienced the 0.5 MGD leak and fast tracked the construction phase, Underground Solutions was responsive to the project requirements to secure, fabricate, deliver and fuse the 1,300 LF of pipe that was ultimately installed on a very aggressive schedule of approximately eight weeks. Fusible PVC® pipe is a great product that Underground Solutions will support and stand behind. We will definitely consider using Fusible PVC® pipe on future projects.”
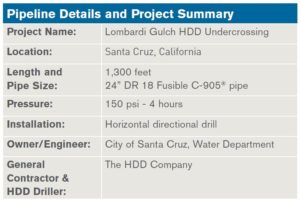
Industry News, trenchless products, trenchless projects
First of Two Mixed Ground Machines will begin boring this autumn
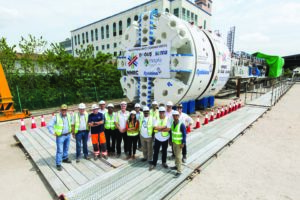
Singapore industrial photographer service
The first of two Slurry TBMs, a rebuilt 6.65 m (21.8 ft) diameter machine, passed its factory acceptance on September 4, 2017 in Singapore. The machine, fitted with a Robbins cutterhead and outer shields, is destined for the Mumbai Metro Line 3 under contract UGC03 for the Dogus-Soma JV (DSJV), and will begin excavation in late 2017. The factory acceptance for a second 6.65 m (21.8 ft) diameter Slurry TBM will be conducted by the end of 2017.
The on-time delivery of the first machine is just the beginning of partnership that will span years. “There are few companies in the international arena that are as professional as Robbins. Robbins has been very helpful to DSJV since the inception of the project and will be our partners until the end of the contract. Robbins’ presence in India including field service crews will be a great help for us in future,” said Mr. DV Raju, Senior Vice President for SOMA.
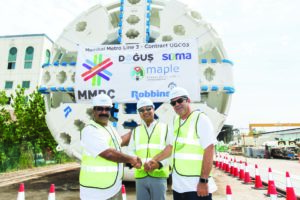
Singapore industrial photographer service
The two machines will excavate parallel 3.5 km (2.2 mi) long tunnels between Mumbai Central and Worli station sites, passing through three intermediate cut and cover stations on the way. Ground conditions consist of fresh to weathered basalt and breccia up to 100 MPa UCS with water pressures up to 3 bar.
The JV selected Slurry machines for their contract due to the challenging ground conditions expected. “I have worked with Slurry TBMs on similar geology globally. Slurry TBMs have real power and will suit the hard rock geology of our Mumbai Metro contract 3. The water table and variable geology, especially basalt of higher hardness, can be easily tackled by Slurry TBMs,” said Mr. Tamay Sayin, Project Manager for DSJV. The cutterheads of the machines are fitted with wear protection, wear detection bits, and Robbins 17-inch disc cutters for the conditions. Grizzly bars will limit the size of boulders that can enter the cutterhead to 250 mm (9.8 in). The slurry systems includes rock crushers as well as abrasion-resistant plating in high-wear areas.
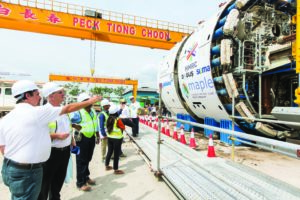
Singapore industrial photographer service
The two TBMs are the first of a total of four machines being provided by Robbins for the Mumbai Metro Line 3. Another two 6.65 m (21.8 ft) diameter Crossover XRE machines will bore parallel 2.8 km (1.7 mi) tunnels on a separate contract in 2018. “Mumbai Metro is one of the most prestigious metro works in the country, and Robbins’ involvement in providing suitable machines and associated services is an honor,” said Kapil Bhati, Managing Director for Robbins India.
The 33.5 km (20.8 mi) long Line 3 of Mumbai Metro being constructed by the Mumbai Metro Rail Corporation (MMRC) will consist of 26 underground stations and one at-grade station that will reduce heavy traffic and rail congestion between Bandra and Churchgate areas of the city. A total of 17 TBMs are being procured to bore various sections of the tunnels, which will be excavated at average depths of 15 to 25 m below the city. The entire line is expected to be operational by 2021.
Image 1: Officials from Robbins, owner MMRC, contractor Dogus-Soma JV, and consultant Maple celebrate the successful factory acceptance testing of a Slurry TBM bound for the Mumbai Metro on September 4, 2017.
Image 2: (From left to right) Mr. DV Raju, Senior Vice President-SOMA, Mr. Kapil Bhati, Managing Director-Robbins India, and Mr. Tamay Sayin, Project Manager-DSJV mark the occasion of the first Robbins TBM to be sent to India’s Mumbai Metro Line 3 project.
Image 3: The Slurry machine is the first of four Robbins TBMs that will be supplied to Mumbai Metro, including two Crossover XRE machines to be supplied to another contract in 2018.
Industry News, trenchless projects
Irrigation and Hydroelectric Project to Ease Food Crisis in Mid-Western Region of Nepal
Nepal will welcome its first TBM ever this summer, a 5.06 m (16.6 ft) diameter Double Shield machine for the Bheri Babai Diversion Multipurpose Project (BBDMP). The Robbins TBM underwent its Factory Acceptance Testing in July 2017 and is currently being shipped to the jobsite in the Siwalik Range, part of the Southern Himalayan Mountains. Pre-construction, including laying gravel onto rural roads and excavating wells for drinking water, has been completed to make way for the TBM and its impending launch.
The BBDMP is one of Nepal’s 11 National Pride Projects–prioritized plans sanctioned by the Government of Nepal to further develop the mainly rural country. This project will irrigate 60,000 hectares (almost 15,000 acres) of land in the southern region of Nepal, benefitting an estimated 30,000 households. It will divert 40 cubic meters of water (1,400 cubic feet) per second from Bheri River to Babai River under a head of 150 m (492 ft) using a 15 m (49 ft) tall dam, providing year-round irrigation in the surrounding Banke and Bardia districts. The water will also be used for hydroelectricity, with a generating capacity of 48 MW benefiting the country with NPR 2 billion (20 million USD) annually.
Contractor China Overseas Engineering Group Co. Ltd. Nepal Branch (COVEC Nepal Branch), represented by China Railway No.2 Engineering Co., Ltd Chengtong Branch, is responsible for the headrace tunnel and is aware of the challenges associated with tunneling in tough geology. “The design of Robbins TBMs is good, and in particular Double Shield TBMs,” said Project Manager of BBDMP, Hu Tianran, for China Railway No.2 Engineering Co., Ltd Chengtong Branch. The Siwalik range is projected to consist of mainly sandstone, mudstone and conglomerate, requiring a TBM that can withstand squeezing ground, rock instability, possibly high ingress of water and fault zones. Maximum cover above the tunnel is 820 m (0.5 mi).
Due to the challenges in the young geology of the Himalayas, Difficult Ground Solutions (DGS) have been incorporated into the machine’s design. A stepped shield has been designed to move through squeezing ground. Robbins Project Engineer Missy Isaman talked about the DGS features incorporated into the TBM: “There is a probe drill in the rear that probes through the gripper shield in 14 places. We added ports in the forward shield for drilling too. There are eight ports around the circumference for hand drilling. There are also six ports in the top 100 degrees of the shield for forepoling.” She further noted that no equipment was ordered for either of the forward shield drilling options, but it’s easier to add the ports to the shield now, in case more comprehensive drilling is needed later in the bore. Other machine modifications included 35 mm (70 mm on the diameter) of possible overcut for gage cutters, and additional ports in the forward shield for dewatering.
Muck removal will be achieved by muck cars. Robbins will provide Field Service to support the machine erection, testing, commissioning and boring of the first 500 m (1,640 ft). The tunnel will be lined with hexagonal precast concrete segments.
The project owner, the Government of Nepal’s Ministry of Irrigation (MOI), has chosen a TBM over the traditional method of Drill &Blast due to the faster mobilization and rate of advance offered by mechanized mining. “The reason a TBM was chosen for this project was because using D&B method could have taken at least 12 years for project completion. This was due to there only being one excavation heading with no possibility of launching multiple operations using adit tunnels,” said Robbins General Manager for Nepal, Prajwal Man Shrestha. More generally, Mr. Shrestha saw the project as a way to prove that TBMs can indeed take on complex Himalayan rock. “Since the Himalayan range has a young geology and not much has been surveyed yet, the use of newer technology is looked upon with slight apprehension. The first few TBM projects and additional surveys will show how suitable TBM technology will be for the Himalayan Range.”
The success of the BBDMP, a national pride project, is paramount for the country as well as the TBM industry. It is expected to help aide the food crisis in the mid-western region of Nepal by increasing agricultural yields and invigorating socio-economic development in the region. The Robbins TBM for the 12.2 km (7.5 mi) tunnel is scheduled to launch in November 2017.
Image 1: The 5.06 m (16.6 ft) diameter Double Shield TBM will bore a 12.2 km tunnel from the Bheri River to Babai River.
Image 2: Due to the geological challenges in the Himalayas, DGS features have been added to the machine including a stepped shield, and dozens of ports throughout the front, rear and around the circumference of the machine.
Image 3:. Mr. Saroj Chandra Pandit, Deputy Director General of DOI (Department of Irrigation) speaking at the Factory Acceptance Testing. Other speakers included Mr. Lin Qiang, Deputy Manager of China Railway No. 2 Engineering Co., Ltd and Mike Kolenich from Robbins.
Image 4: The Robbins crew, contractor COVEC Nepal Branch, and project officials stand proudly in front of the Robbins Double Shield TBM that will tackle the challenging geology in the Himalayas.
Blog, Industry News, trenchless projects
Custom Robbins Machine finishes on a High Note under Low Cover
On June 8, 2017, a select group of project officials, including Mexico’s President Enrique Peña Nieto, celebrated the final breakthrough of an epic tunneling project. The 8.7 m (28.5 ft) diameter Robbins Crossover TBM is the first such hybrid machine to operate in North America, and it completed the Túnel Emisor Poniente (TEP) II on a high note. The TBM, known an XRE—a Crossover (X) between Rock (R) and EPB (E) TBMs—navigated fault zones, variable ground, low cover, and more to achieve a national record of 57 m (187 ft) in one day as well as maximum rates of 231 m (758 ft) in one week and 702 m (2,303 ft) in one month.
“The XRE has a great advantage as it is designed to work in open and/or closed mode (EPB); allowing it to excavate the tunnel either in soil or in rock. We’ve verified that its performance was very efficient,” said Ing. Juan Alberto Herrera Moro y Castillo, TEP II Section Chief for owner CONAGUA, Mexico’s National Water Commission.
The unique machine and its Robbins continuous conveyor system were built on location using Onsite First Time Assembly (OFTA), and designed for a contractor consortium of Aldesem, Proacon, and Recsa. The Robbins XRE TBM featured components like a convertible cutterhead with interchangeable cutting tools, interchangeable TBM belt conveyor and screw conveyor, and multi-speed gearboxes to increase torque for tunneling through difficult ground. “The benefits of the design are in its exceptional thrust power and in the ease of changing the cutterhead torque. This makes the process much easier should the machine become stuck in difficult ground,” said Alberto Martinez, head of the tunneling department for RECSA.
The XRE machine was launched in August 2015 to bore the 5.8 km (3.6 mi) long wastewater tunnel. The machine was set up in a hard rock configuration and mounted with 20-inch diameter disc cutters. Early in 2016 the TBM hit the first of several contact zones, a 30 m (98.4 ft) wide fault of fractured and blocky rock. While the excavation through the contact zone was slow going, progress picked up again in the more competent andesite rock. After an intermediate breakthrough in March 2016 into an 80 m (262.5 ft) deep shaft followed by inspection and maintenance, the TBM continued on.
While boring in fractured andesite rock in autumn 2016, the TBM encountered a naturally occurring cavern believed to be the result of either a rock fall in a transition zone, or an old, underground lake body that had eroded the rock away. The cavern was estimated at 90 cubic meters (3,200 cubic ft) in size, including about 57 cubic meters (2,010 cubic ft) of unstable floor area. The TBM was stopped and immediate measures were taken to stabilize the ground in front of the machine with polyurethane foam before filling the cavern with a mixture of pea gravel and grout.
By the end of October 2016, the TBM had reached a final 900 m (2,950 ft) long section of soft ground, where it was converted to EPB mode. In this final reach of tunnel with low cover, the distance from the top of the tunnel to residential home foundations was as low as 4 m (13 ft), and the ground had the consistency of reconsolidated soil. In order to stabilize the soft soils and minimize the risk of settlement below the residential area, the tunneling crew drilled from the surface and installed 890 micro-piles at 1.0 m (3.3 ft) intervals. “We were able to do this without causing damage to property owned by neighbors in the zone bordering the path of TEP II, or to the road or the urban infrastructure installed in that area,” explained Ing. Francisco Miguel Lopez, Jobsite Manager TEP II for contractor Aldesa.
Now that tunneling is complete, the tunnel will receive a secondary concrete lining of 35 cm (14 in) thickness before going into service. The wastewater tunnel will overhaul the current system in western areas outside of Mexico City and serve to prevent recurrent flooding in Valle Dorado. In particular, the tunnel will benefit the cities of Cuautital Izcalli, Tlalnepantla, and Atizapan de Zaragoza, which altogether are home to 2.1 million inhabitants.
Image 1: The 8.7 m (28.5 ft) diameter Robbins XRE TBM was the first Crossover machine to bore in North America.
Image 2: Robbins personnel stand proudly in front of the Crossover TBM for Túnel Emisor Poniente (TEP) II—the project resulted in challenges as well as national records for TBM advance.
Image 3: During its bore, the Crossover achieved a national record for TBM advance, excavating 57 m (187 ft) in one day as well as achieving high rates of 231 m (758 ft) in one week and 702.2 m (2,303 ft) in one month.
Blog, Industry News, trenchless projects
Large Diameter XRE Machine to bore Akron, Ohio’s Wastewater Tunnel
A Robbins Crossover (XRE) TBM measuring 9.26 m (30.4 ft) in diameter underwent factory acceptance on May 30, 2016. The gargantuan machine was initially unveiled at Robbins’ Solon, Ohio headquarters during a press day on May 25 before being shipped 40 km (25 mi) south for construction of the Ohio Canal Interceptor Tunnel (OCIT) in Akron. Those present included Akron Mayor Daniel Horrigan, Robbins chief engineer Dennis Ofiara, and David Chastka, project engineer for contractor Kenny-Obayashi JV.
The TBM, which includes features of both EPB and Hard Rock Single Shield TBM types, is the first Crossover machine to be used in the United States. It will be launched from a 12 m (40 ft) deep portal site and build the first 68 m (226 ft) in soft ground, transitioning to a 183 m (600 ft) long zone of partial face shale before switching to hard-rock mode for the remainder of the drive in full face shale. Probe drilling will be done continuously using two probe drills to determine which mode the TBM should be in.
Unique aspects of the machine include a versatile cutterhead that will be configured with consideration for both the short soft ground section and the longer section (about 65% of the tunnel) in hard rock. A combination of disc cutters and sacrificial rippers will be used in case a cutter becomes blocked. The required rolling torque of the disc cutters has been reduced by 25% to encourage smooth rotation in soft ground. The motors of the XRE machine have been reworked from an original EPB configuration to permit higher motor speed at reduced torque for the open mode segments of the drive.
Muck removal will be achieved with a durable screw conveyor, the first flight of which is covered welded-in wear plates. The auger shaft is lined with hard facing in a crosshatch pattern, while the screw conveyor casing has been similarly lined in wear plates and hard facing. A wear monitoring plan has been prepared for the entire drive in order to maximize efficiency in the section of more abrasive rock. Robbins Project Manager Pablo Salazar is proud of the utilization of local jobs during the TBM construction and design process: “We have built good portion of the machine in the northeast Ohio area. Many components were fabricated locally with sub-suppliers, as well as in our own shop.” The muck will be transported out of the tunnel using a Robbins continuous conveyor system—the setup will be the 100th such conveyor supplied by Robbins for operation behind a TBM.
The machine was dubbed “Rosie” in honor of Rosie the Riveter, an icon representing the American women who worked in factories and shipyards during World War II. Hundreds of “Rosies” including Akron resident Rose May Jacob worked in factories to turn out materials and armaments for the Allied war effort. The TBM will be shipped in truckloads to the jobsite, with the large cutterhead shipped in four pieces. “The entire process of assembly has allowed the contractor to follow very closely through the testing of the machine, so they are very familiar with the TBM at this point. At the jobsite, we will also provide immediate support for both spare parts and personnel,” said Salazar. Jobsite supervisors from Robbins will assist in TBM assembly and excavation for at least the first 1,000 m (3,280 ft) of boring. Tunnel boring is scheduled to begin in August of this year.
The OCIT Project for the City of Akron consists of the construction of a conveyance and storage tunnel system to control Combined Sewer Overflows (CSOs) for several regulators in the downtown Akron area. The EPA-mandated project includes the 1.89 km (1.17 mi) conveyance and storage tunnel, as well as drop shafts, diversion structures, consolidation sewers, and related structures. The consent decree specifies that the tunnel must be operational by December 31, 2018.
Image 1: The 9.26 m (30.4 ft) diameter Robbins Crossover Tunnel Boring Machine (TBM) was designed and built in Robbins’ Solon, Ohio, USA facility.
Image 2: Robbins personnel proudly stand in front of the 9.26 m (30.4 ft) machine dubbed “Rosie”—the first Crossover TBM in the U.S.
Image 3: The Robbins TBM will bore in sections of both hard rock and soft ground to complete the Akron Ohio Canal Interceptor Tunnel (OCIT).