Uncategorized
Akkerman Tunnel Boring Systems have been installing pipe around the world for over 40 years. Akkerman is pleased to introduce the 5200 Pump Unit, the most essential element of the Tunnel Boring System. This flagship product has been improved in several essential areas while retaining the best qualities of its predecessors, to achieve optimal pipe jacking performance.
The 5200 Pump Unit maximizes the Tunnel Boring System’s capabilities with enhanced functionality to offer the utmost power and precision in many geological circumstances. The unit presents application flexibility with three independent hydraulic sources – two low-pressure sources for the Tunnel Boring Machine (TBM) boring head supply and one high-pressure source for jacking and Intermediate Jacking Stations (IJSs).
Low-pressure hydraulic boring head supply is provided by two, 100 HP (74 kW), totally enclosed fan-cooled (TEFC) electric motors. Each motor features variable displacement piston pumps managed with electronic displacement control, allowing the user to select between 30, 60, 90, or 120 gpm at the flip of a switch. The boring head system supplies 30-120 gpm of oil at 3,000 psi to all Akkerman TBMs or 30-60 gpm at 5,000 psi to Series II TBMs. The advanced 5,000 psi boring head supply is advantageous in demanding ground conditions which require increased cutter torque and greater horsepower in single feed applications.
All jacking and IJSs functions are accomplished by a 12.5 gpm, 8,000 psi capable pump, driven by a 60 HP TEFC electric motor. At 8,000 psi, the jacking system offers 400 tons of jacking force and 30% more pressure for the IJSs. Operators will appreciate the handling of jacking functions with variable pump output and electronic valve actuation.
A 240 gal (908 L) hydraulic tank supplies oil to the pumps and in-tank filtration keeps it free of contaminates. Oil also continuously flows through a dedicated cooling and filtration circuit.
The importance of operator’s safety is evident in the 5200 Pump Unit design. An emergency e-stop is located on the operator’s platform and an optional remote cabled e-stop is available for in-shaft personnel. The control panel on the operator’s station has an enhanced interface and simplified appearance.
The 5200 Pump Unit touts many additional quality features. The unit can be hoisted from a single lift point. The location of the laser slot ensures an unobstructed laser path. Removable, vandal resistant, lockable doors protect the unit during when not in use. Electric is facilitated through a 400-amp, 480-volt, 3-phase connection. The 5200 Pump Unit is 90-in. (2,286 mm) tall, making it ideal for clearance when used with most pit shorting configurations.
The 5200 Pump Unit is interchangeable with all Akkerman Tunnel Boring System components. Contact a sales engineer for more information about this and all Akkerman equipment offerings at +1 (800) 533.0386 and visit akkerman.com.
Uncategorized
Vac-Tron Equipment, the industry innovation leader in industrial vacuums, potholing, daylighting, hydro excavation, air excavation and environmental clean-up equipment, would like to introduce the new LP 533/833 SGT, our new gas unit.
SGT: Powered by a 37 HP Kohler Gas Engine, this is a unit with similar performance specs as the pre tier 4 final SDT model with 1000 CFM Vacuum Pump. The SGT delivers great performance with a much lower cost of the Tier 4 final Diesel option.
This machine features the new SERIES 33 SAFETY REAR DOOR. The hydraulic screw rear door offers a high torque motor with a self-adjusting threaded shaft designed for low maintenance and easy operation. It opens to a full 90” angle and is equipped with a safety lock that engages automatically.
It features CVS FILTRATION HOUSING. The LP ground level filtration housing also incorporates a 28″ (71.1 cm) diameter cyclone, four-way valve for reverse pressure, and the largest silencer in the industry for quiet performance. Patent pending.
It has an OPTIONAL STRONG ARM. The Optional strong arm is to help support the weight of the vacuum hose.
It has 6″ (15.2 CM) DEBRIS DISCHARGE VALVE. For quickly off-loading liquid materials by gravity or under pressure to another container.
EASY ACCESSIBILITY. Easy access engine compartment for service and regular maintenance of all components.
For more information contact Vac-Tron Equipment LLC at 1-888-Vactron or visit us online at www.vactron.com.
Vac-Tron Equipment, LLC. reserves the right to make changes in engineering, design and specifications; add improvements; or discontinue manufacturing at any time without notice or obligation. Equipment shown is for illustrative purposes only and may display optional accessories or components.
Uncategorized
EPA is committed to promoting sustainable practices that will help ensure that citizens continue to enjoy the benefits of clean and safe water. Guided by the
Agency’s Clean Water and Drinking Water Infrastructure Sustainability Policy, EPA is working with a broad group of stakeholders to help bring about more sustainable practices on three levels.
· Sustainable Water Infrastructure—Sustaining the collection and distribution systems, treatment plants and other infrastructure that collects, treats and delivers water-related services.
· Sustainable Water Sector Systems—Sustaining all aspects of the utilities and systems that provide water-related services.
· Sustainability Communities—Promoting the role of water services in furthering the broader goals of the community.
Each of these levels supports the others. The effective management of water infrastructure is one of the main challenges faced by our water sector systems. Our water sector systems must also address a range of other challenges to ensure their operations and infrastructure are sustainable. Sustainable infrastructure and systems are essential to ensuring the environmental and economic sustainability of communities throughout the nation. Learn more here.
Source: EPA.gov
Uncategorized
Improving the security and resilience of our nation’s drinking water and wastewater infrastructures is vital to ensure the provision of clean and safe water to all in the United States.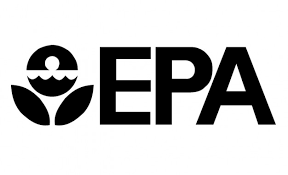
Significant actions are underway to assess and reduce consequences, threats, and vulnerabilities to potential terrorist attacks; to plan for and practice response to natural disasters, emergencies, and incidents; and to develop new security technologies to detect and monitor contaminants and prevent security breaches.
Visit the EPA’s basic information page for more info or read Nancy Stoner’s blog post about water security.
Source: EPA.gov
Uncategorized

Iron Workers Reward World-Class Safety on Challenging Projects
First-Ever Project of the Year Winner Announced at Annual Meeting
WASHINGTON –The Iron Workers and the Ironworker Management Progressive Action Trust (IMPACT) honored the safest, most complex and most creative ironworker projects of 2014 on February 24, 2015, at the North American Iron Workers/IMPACT Annual Meeting in Las Vegas. Anthony Pangere of the Pangere Corporation and Ronald Ware, Jr., of Iron Workers Local 395 in Hammond, Indiana, accepted the award.
The decision was made by a panel of independent judges who critiqued each submission on the safety, complexity, and ingenuity used to achieve success.
“We are proud of all of the finalists in the first-ever Project of the Year award competition,” said IMPACT CEO Kevin Hilton. “We are so inspired by the projects submitted, and look forward to see even more submissions next year.”
“Our aim is to make sure all workers come home safely each day,” added Iron Workers General President Walter Wise. “The Iron Workers and IMPACT are excited to see so many projects completed with such complexity, ingenuity and with a focus on safety.”
“The Project of the Year award is a source of pride for us,” said IMPACT Co-Chair Bill Brown. “The award shows our dedication to creating the safest possible environment for ironworkers, so that we in turn can provide the highest level of service to end-users.”
In order to maintain the safest conditions and ensure no disruption to production, Pangere required ironworkers to communicate the facilities movements to work crews before they happened. Communication was key between ironworkers and plant operators to avoid the dangers of hot metal splashes and moving equipment. Pangere supervision attended all production meetings to ensure proactive planning around plant operations and held meetings with all ironworkers before each shift to discuss changes in the environment and potential hazards. In addition, Pangere will send ironworkers to the Construction Advancement Foundation a local training facility for additional safety courses.
The Project of the Year award honors the safest, most challenging projects completed in the last calendar year. Numerous contractors go above and beyond the call of duty to not only provide safe conditions for their workers on challenging jobs with unique circumstances, but to also demonstrate ingenuity and creativity. The Project of the Year award spotlights contractors’ outstanding projects for their unique nature and their commitment to excellence in safety.
Source: ironworkers.org
Uncategorized
McLaughlin introduces VX30-300 vacuum excavator with big features and small footprint
Unit has patented rear hydraulic door, reverse pressure flow, water heater
GREENVILLE, S.C.— McLaughlin has introduced the VX30-300, a vacuum excavator that is compact in size but with features typically found only on larger machines.
The VX30-300 features a cam-over rear hydraulic door, a cyclonic filtration system, optional reverse flow for pressure offloading of materials and the ability to add a water heater to help when working in frozen ground conditions.
All of this comes in a machine with a 9,999-pound gross vehicle weight rating, alleviating the need for a CDL for drivers transporting the vacuum excavator. That makes it an ideal unit for rental stores and their customers.
Utility companies and contractors also will benefit from the portable, compact and versatile VX30-300 vacuum excavator for their potholing jobs and fluid management on horizontal directional drilling projects.
The VX30-300 has a 300-gallon (1,135.6 L) spoil tank and a 31-horsepower (23.1 kW) Yanmar diesel engine.
“The VX30-300 has many of the same features that our larger vacuum excavators offer, but in a smaller package,” McLaughlin Vice President Jeff Wage said.
The VX30-300 has a hydraulic door, which makes dumping and cleaning the spoils tank faster and more convenient. It also has a patented cam-over locking system that provides a 360-degree positive seal, even under reverse pressure, without additional clamping requirements. It also has no in-tank parts, so all maintenance is external.
Unlike a manual door, the hydraulic door allows for reverse pressure to clear hose clogs simply by changing the valve position to reverse the airflow. It also lets operators work faster by pressure offloading spoils and being able to strategically direct fluids rather than just dumping them into a big puddle.
The VX30-300 also has room for a water heater, or hot box. Such a feature benefits crews working in cold weather and digging in frozen ground, or in soil conditions where grease is present, like at a car dealership or car wash.
The unit’s 3-stage cyclonic filtration system allows for wet and dry vacuum excavation while prolonging filter life and keeping maintenance costs low
The VX30-300 also comes with a tandem axle chassis, which aids in stability and axle life.
The McLaughlin vacuum excavator line is available through the Vermeer dealer network.
For more information on McLaughlin products and services, visit the company’s Website at www.mclaughlinunderground.com or email McLaughlin at mmole@mightymole.com.
For over 85 years, McLaughlin has been actively involved in the drilling tool industry. During that time McLaughlin has developed a reputation for designing and building dependable, low maintenance trenchless construction equipment. McLaughlin takes pride in providing solutions for OEMs and the underground industry.
© 2015 McLaughlin Group, Inc.
All Rights Reserved.
Please send all reader inquiries to:
McLaughlin Group, Inc.
2006 Perimeter Road
Greenville, SC 29605
Please send all sales inquiries to:
mole@mightymole.com