Industry News, trenchless people
THOMPSON, CONNECTICUT USA: Numa, the world’s leading drilling technology provider, has announced the addition of Gregg Hayes as Product Manager HDD. Gregg is based in New York and will head up business development, service, and support of Numa’s horizontal directional drilling (HDD) products. The position will require him to grow direct and dealer sales of Numa’s horizontal hammers, bits, and drilling systems.
Gregg is a recognized expert in HDD and comes to Numa with 20 years of experience in the drilling industry. For the past 5 years, he was a top HDD salesperson selling into multiple US markets while also focusing on the further development of horizontal rock drilling products. Previously, he served in various sales and management roles for companies selling tooling, drilling fluids, bits, reamers, rock tools, swivels, etc. His experience and background provide drillers with a wealth of knowledge and insight.
“Gregg is one of the foremost experts in HDD with a proven track history of teaching drillers the most effective ways to drill using pneumatic hammers and bits in horizontal drilling applications,” said Numa Vice President of Sales, Neal Kuszewski. “He is a great addition to our team and further demonstrates Numa commitment to providing the best drilling resources in the industry.”
Gregg commented, “Throughout my career, I have recognized Numa to be the industry leader in rock drilling products. I am very excited to join Numa and continue their long history of providing customers with the right products, expertise, and support.”
ABOUT NUMA
Numa is the world’s leading drilling technology provider, dedicated to ongoing product innovation and results-oriented consistency. We’ve built a strong legacy of high quality, U.S. made hammers and bits for drilling holes 3½ – 50½ inches (89 -1283 mm) in diameter. With over 100 hammer and bit products serving 11 different industries, our products are capable of drilling vertical, horizontal, and reverse circulation holes in hard rock and unconsolidated formations.
Industry News, trenchless projects
Galerie des Janots Main Beam completes Arduous French Drive
In April 2019, a Robbins 3.5 m (11.5 ft) diameter Main Beam TBM broke through into open space, completing its 2.8 km (1.7 mi) long tunnel. It was not the first time the machine had encountered open space: twice during tunneling, the machine hit uncharted caverns, the largest of which measured a staggering 8,000 cubic meters (283,000 cubic ft) in size.
The obstacles overcome at the recent breakthrough are a significant achievement, said Marc Dhiersat, Project Director of the Galerie des Janots tunnel for contractor Eiffage Civil Construction. “We are proud to have led a motivated and conscientious team to the end of the tunnel who worked well without accidents despite the many technical difficulties encountered.”
The water tunnel, located below the community of Cassis, France, is an area of limestone known for its groundwater, karstic cavities, and voids. The limestone, combined with powdery clays, made for difficult excavation after the machine’s March 2017 launch. At the 1,035 m (3,395 ft) mark, the crew hit a cavern on the TBM’s left side. The cavern, studded with stalactites and stalagmites, was grazed by the TBM shield. The crew had to erect a 4 m (13 ft) high wall of concrete so the TBM would have something to grip against. The TBM was then started up and was able to successfully navigate out of the cavern in eight strokes without significant downtime to the operation—the process took about two weeks. Despite the challenges, Dhiersat thought positively of the TBM throughout the ordeal: “This has been the best machine for the job due to all the geological difficulties.”
The first cavern, while the largest, was not the most difficult void encountered. The machine was averaging 20 to 22 m (65 to 72 ft) advance per day in two shifts after clearing the first cavity, with a dedicated night shift for maintenance. While excavating, a combination of probe drilling and geotechnical BEAM investigation—a type of electricity-induced polarization to detect anomalies ahead of the TBM—were used. Crews ran the excavation five days per week, achieving over 400 m (1,310 ft) in one month. This performance continued until the 2,157 m (7,077 ft) mark, when the machine grazed the top of an unknown cavity that extended deep below the tunnel path. The structure measured 22 m (72 ft) long, 15 m (49 ft) wide, and 14 m (46 ft) deep, or about 4,500 cubic meters (159,000 cubic ft) of open space.
Crews probed in front of the cutterhead and began work to stabilize and secure the cavity with foam and concrete, as well as excavate a bypass gallery. “After filling much of the cavity (1,500 m3/53,000 ft3), our biggest difficulty was to ensure the gripping of the machine: We needed six bypass galleries and four months of work to reach the end of this challenge,” said Dhiersat. For the last 600 m (2,000 ft) of tunneling, “we were finally in good rock,” he emphasized. Overall rates for the project averaged 18 m (59 ft) per day in two shifts, and topped out at 25 m (82 ft) in one day.
“The cooperation with Marc and his team on site was very good and we always enjoyed their professionalism and commitment to the project and the task. This, without any doubt was key for the success we achieved,” said Detlef Jordan, Business Manager Robbins Europe. “For us, it was satisfying and motivating to see that, by working together and joining the efforts of all partners on the project, the best and most successful outcome can be achieved. This commitment for decades has been at the heart of success in the tunneling industry, but it has not always been observed on other recent projects.”
Galerie des Janots is one of fourteen operations designed to save water and protect resources, which are being carried out by the Aix-Marseille-Provence metropolis, the water agency Rhône Mediterranean Corsica, and the State Government. The Janots gallery, once online, will replace existing pipelines currently located in a railway tunnel—these original pipes have significant deficiencies with estimated water losses of 500,000 cubic meters (132 million gallons) per year. The new tunnel will increase capacity to 440 liters (116 gallons) per second.
Image 1: Contractor Eiffage Civil Construction celebrates the April 2019 breakthrough of a 3.5 m (11.5 ft) diameter Robbins Main Beam TBM in Cassis, France.
Image 2: Despite challenges including karstic limestone and clay, the Robbins TBM at Galerie des Janots achieved rates of 18 m (59 ft) per day on average, and topped out at 25 m (82 ft) in one day.
Image 3: The Robbins machine overcame tough conditions including two uncharted caverns, the largest of which measured a staggering 8,000 cubic meters (283,000 cubic ft) in size.
Image 4: The first cavern, encountered at the 1,035 m (3,395 ft) mark, was grazed by the TBM shield on one side and was studded with stalactites and stalagmites.
Industry News, trenchless products
May 1, 2019: Pipe Lining Supply announces its 15th anniversary as a nationwide, full‐service,
Pipe Rehabilitation Distributor.
Pipe Lining Supply (PLS) was founded on January 1, 2004 by Linda Heisler. Her primary focus was the CIPP industry in the California area. She saw a need to service customers with reasonably priced materials and great customer service. Two years later her husband John Heisler joined the company bringing a wealth of expansive knowledge of the industry including CIPP Lateral Lining, Pipe Bursting, HDD, Pipe Coating, Sewage Lining, Open Cut and Cover,
Water and Sewer Utility work.
Since 2004 Pipe Lining Supply, has evolved to a reputable company that manufactures and
distributes CIPP lateral lining equipment such as the Quik‐Shot™ System (launched in 2009),
resin and lining materials. In 2017, PLS introduced its AIPPR Quik‐Coating System designed for
drain, waste and vent (DWV) piping extending pipe life by 50+ years. PLS offers a full line of
equipment, materials and expert training to plumbers and drain cleaners so they have a “one
stop shop” in the pipe rehabilitation industry.
The company has also expanded its market, their team includes technical experts across the
USA, but also have a presence nationwide. “Pipe Lining Supply has experienced exceptional
growth and development over the past years” said Heisler. “Moving forward, our focus will
remain the same as day one, offering great equipment and materials with top notch training
and superior customer support.”
Over the past 15 years, Pipe Lining Supply has been evolving into a successful business that is a
leader in the industry with an enthusiasm to keep it growing and changing in the most
competitive way possible.
For more information on Pipe Lining Supply and their products please visit
http://www.pipeliningsupply.com
Contact info: Michelle Strasburg
Director of Marketing
info@pipeliningsupply.com
Phone: +1‐888‐354‐6464
Industry News, trenchless people
Brownsdale, MN – April 11, 2019 – Akkerman Inc., a premier trenchless underground construction systems manufacturer, attained the International Organization for Standardization (ISO) ISO 9001:2015 for its quality management system at its sole manufacturing facility in Brownsdale, MN.
Following an independent audit conducted by SAI Global, the certificate was issued on January 18, 2019.
The scope of the certification applies to the design, manufacture, sales, and services of on line and on grade tunneling and pipe jacking products for the underground sewer, water, gas, and electrical utilities industries.
Akkerman embarked on the implementation of its quality management system in 2015 with consulting assistance from Enterprise Minnesota who was integral to the system’s execution.
Justin Akkerman, Akkerman operations manager, remarks, “Minnesota Occupational Safety and Health recognized us through the Minnesota Safety and Health Achievement Recognition Program for our safety program in 2010. Having our management system certified to ISO 9001:2015 was a natural progression to strengthen the business.”
Akkerman furthers, “Not only does our comprehensive quality management system benefit our employees through procedure efficiencies and repeat-ability, but our customers can also feel confident in knowing that the equipment that we manufacture is subject to the highest standards and continuous improvement at every step in the manufacturing process. Our ISO 9001:2015 Quality Management System ensures that from design conception to final product testing, our equipment is produced with quality and value at the forefront.”
Established in 1973, Akkerman develops, manufactures and supports advanced guided boring, microtunneling, pipe jacking, sliplining and tunneling underground construction solutions that accurately install a variety of pipe in an extensive range of ground conditions and project challenges. Akkerman systems are available for purchase, lease-to-purchase, or rent from our rental fleet. Contact us to partner with you on your next project at 800.533.0386 and visit akkerman.com.
Industry News, trenchless products
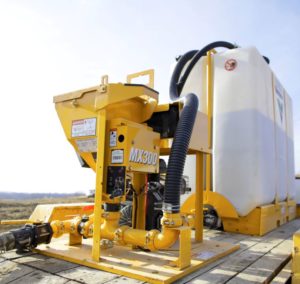
PELLA, Iowa, April 11, 2019 – The right-sized mixing system is key for drilling operations. With a redesigned, slim rectangular profile tank, the new Vermeer MX300 mixing system helps horizontal directional drilling (HDD) contractors optimize productivity and offers customizable mounting configuration options. Equipped with a 23 hp (17.2 kW) Kohler ECH 7300 EFI gas engine that outputs 350 gpm (1,324.9 Lpm) of flow, the MX300 mixing system power unit can be paired with up to two tanks at once to help decrease time spent mixing and refilling drilling fluid tanks. The unit’s narrow rectangular tank design also helps maximize fluid volume, and a small footprint can help with convenient transporting and storage.
“The Vermeer MX300 mixing system is an upgrade to the MX240 model,” explained Tod Michael, product manager of trenchless products at Vermeer. “With the ability to use one pump with one or two tanks, the MX300 is scalable to a contractor’s jobsite needs from small bores to large-diameter and longer-distance HDD applications in varying soil types.”
The new Vermeer mixing system can be paired with a 750 gallon (2,839.1 L) or 1,000 gallon (3,785.4 L) tank and works with a variety of horizontal directional drills. It features a wide-mouth hopper and suction hose for the convenient pouring of drilling additives. The tapered bottom of the rectangular tank design helps prevent additives from settling, building up and assists with efficient drainage. At a width of just 40 inches (101.6 centimeters), the MX300 can be mounted to transport two tanks inside a standard-sized enclosed truck.
The MX300 comes with a 16 gallon (60.6 L) fuel tank and is convenient to service with access to the roll jets through the top of the tank and two drainage points that are operated by two accessible valves.
For more information about the Vermeer MX300 mixing system, visit Vermeer.com or contact your local Vermeer dealer.
About Vermeer Corporation
Vermeer delivers a real impact in a progressing world through the manufacture of high-quality underground construction, surface mining, tree care, agriculture and environmental equipment. With a reputation for durability and reliability, that equipment is backed by localized customer service and support provided by independent dealers around the world. To learn more about Vermeer, products, the dealer network and financing options, visit Vermeer.com.
Vermeer Corporation reserves the right to make changes in engineering, design specifications; add improvements; or discontinue manufacturing at any time without notice or obligation. Equipment shown is for illustrative purposes only and may display optional accessories or components specific to their global region.
Please contact your local Vermeer dealer for more information on machine specifications.
Industry News, trenchless people
Active NASTT volunteer, instructor and past Board Chair, George Ragula recently visited the NASTT Student Chapter at Rutgers University in New Jersey to speak with them about trenchless technology and the gas industry.
George stated that is was a very interactive and informative session for the students. He gave a detailed presentation of the 36” world record gas CIPL renewal and there were a lot of questions. The students were curious as to how and when George got started in trenchless, his motivation and how he came up through the ranks at NASTT when he first joined in 1993.
The students also expressed interest in developing a trenchless curriculum as part of a Masters course and he offered his help and guidance. They discussed the fast growing pace of this particular industry. The students feel positive about this niche in the construction industry and many hope to pursue a career in trenchless.
Industry News, trenchless people
Laney Group, Inc. (“Laney”) and Innovative Pipeline Crossings, Inc. (“IPC”) have signed a teaming agreement, under which they will cooperatively pursue projects that require a combination of their services and expertise. Laney provides an integrated suite of Engineering, HDD, Direct Pipe® and Project Management solutions internationally. IPC, a Bothar Group Company, provides Direct Pipe®, Auger Boring, Pipe Jacking and Microtunneling solutions throughout Canada. Laney and
IPC will strategically augment each other’s existing capabilities in their respective markets.
Laney Group, Inc. has a long history and is an established leader in HDD and Direct Pipe® Installations internationally. As part of a recent management change and a industry acquisition, Laney now delivers integrated Engineering, Procurement, Construction and Project Management Solutions to serve our clients in the trenchless industry and beyond… Worldwide. Per Todd Miller, Laney Group CEO, “First and foremost, IPC and Bothar are both world-class companies led by world-class leaders. We are thrilled to be partnering with IPC to be able to deliver a comprehensive suite of trenchless solutions to our
international clients in a world-class manner. We look forward to the next steps”.
With a proven track record of successful projects, IPC is currently one of the largest Direct Pipe® contractors in Canada. Notable accomplishments include simultaneous DPI operations in British Columbia and Ontario in 2017 and a Performance World Record for drilling 218m in 24hours.
IPC was acquired by the Bothar Group of Companies in November 2018, one of the largest Microtunneling contractors in the world. Since the acquisition, IPC has been expanding its range of operations into other disciplines such as Auger Boring, Pipe Jacking and Microtunneling.
This cooperation agreement allows both companies to collaborate on a full range of trenchless installation technologies and solutions in North America and internationally. Combined technical experience, access to specialized equipment and utilization of engineering knowledge and experience will enable both parties to provide the best technical and most costeffective solutions to clients across the range of trenchless solutions.
Peter Hennig – CEO of IPC, Inc.: “A trustful relationship between the senior management of both entities will allow for a successful future in this alliance. I’m very excited for both of our companies and our employees. New opportunities, paired with each of our experiences and available resources, will open up the path to exciting new horizons.”
For further information, please contact:
IPC Contact details: info@ipipecrossings.com
Laney Group, Inc. contact details: info@laneydrilling.com
Industry News, trenchless projects
XRE Machine completed National Priority Water Line set to go Live in March
Excavation of Turkey’s longest water tunnel came to an end on December 18, 2018. To get there, a 5.56 m (18.2 ft) diameter Robbins Crossover (XRE) TBM and the contractor JV of Kolin/Limak had to overcome dozens of major fault zones and water pressures up to 26 bar. The completed national priority water line is set to go into operation in March 2019.
The 31.6 km (19.6 mi) long Gerede Water Transmission Tunnel is an urgently needed project due to severe and chronic droughts in the capital city Ankara. Its final leg, a 9.0 km (5.6 mi) section of extremely difficult ground including sandstone agglomerate, limestone and tuff, was just one section in the middle of a tunnel widely considered to be the most challenging ever driven by TBMs in Turkey. “I’ve had the chance to study and visit the majority of mechanized tunnelling projects in Turkey since the 1980s. The Gerede project is one of the most challenging projects among them,” said Dr. Nuh Bilgin, Professor of Mine and Tunnel Mechanization at Istanbul Technical University and Chairman of the Turkish Tunnelling Society.
The Robbins XRE TBM was called in to complete the tunnel, which was at a standstill after using three Double Shield TBMs from another manufacturer. Those machines encountered incredibly difficult geology including massive inrushes of mud and water. The Kolin/Limak JV had to develop a new strategy given the unexpected ground conditions. They contacted The Robbins Company, who suggested a Crossover (Dual-Mode Type) TBM for the remaining section of tunnel. “The Crossover TBM provided great ease and versatility during the entire project with frequently changing ground conditions. The TBM was equipped with features such as increased thrust, two-speed gearbox, and modular screw conveyor. It was capable of giving the necessary responses in different geologies, which was our most important asset in achieving our goal,” said Barış Duman, Project Manager for the Kolin – Limak JV.
“The challenging part for us was to design and manufacture a TBM that could complete the difficult section of the Gerede Tunnel where two other competitor TBMs had failed,” said Yunus Alpagut, Robbins representative in Turkey. The specialized machine was designed to statically hold water pressure up to 20 bar, a failsafe that none of the standard Double Shield TBMs had been equipped with. A convertible cutterhead was also provided that was designed for ease of conversion between hard rock and EPB modes, and with cutter housings that could be fitted with either disc cutters or tungsten carbide tooling. To cope with difficult ground, the Gerede machine was also equipped with the Torque-Shift System, multi-speed gearing allowing the machine to function as either an EPB or a hard rock TBM. This function is done by adding another gear reduction–heavy duty pinions and bull gears accommodate high torque at low speed, allowing the machine to bore through fault zones and soft ground without becoming stuck.
The Crossover machine was assembled in spring 2016 after crews excavated a bypass tunnel to one side of one of the stuck Double Shield TBMs. An underground assembly chamber allowed the machine to be built in the tunnel using Onsite First Time Assembly (OFTA). “The logistics of getting components through the existing tunnel were the most challenging thing. The assembly chamber was 7 km (4 mi) from the portal. The water inflow of 600 l/s (159 gal/s) made it difficult to get the materials to the machine,” said Glen Maynard, Robbins Field Service Site Manager.
Despite the challenges, the machine began boring in summer 2016 and within the first 50 m (160 ft) of boring had successfully passed through the section that buried the original Double Shield TBM. The machine was required to be used in EPB mode as it encountered water pressures up to 26 bars, alluvium, flowing materials, clay and a total of 48 fault zones. Water pressure was lowered by draining the ground water through the rear shield probe drill ports, which were equipped with normally-closed ball valves. Probe drilling was done on a routine basis to get through the ground conditions. “Together with the difficult geological conditions the travel time to reach the TBM within the tunnel had effects on TBM performance. Despite this constraint, the tunnel excavation achieved a best day of 29.4 m (96.5 ft), best week of 134.6 m (441.6 ft) and a best month of 484 m (1,588 ft),” said Duman.
“We had many challenging areas with water and high pressures up to 26 bar along with alluvial material in fault zones. Ground pressure on the shield body caused squeezing conditions in clay. In these regions, we were able to quickly pass through by keeping the TBM advance rate, cutterhead rpm and screw conveyor rotation speed at the ideal level. Ultimately, we think our decision to select a Crossover TBM was correct,” continued Duman.
With tunneling complete, the pipeline is on track to open in March 2019. The tunnel will convey water from the Gerede River to Çamlıdere Dam, which provides potable water for the Ankara city water system.
Image 1: To achieve their recent breakthrough, the Kolin/Limak crew, including Barış Duman – Project Manager of Kolin – Limak JV (7th from left), had to guide the Crossover XRE TBM through multiple fault zones and withstand water pressures of up to 26 bar.
Image 2: The Robbins team and contractor JV of Kolin/Limak pause during Onsite First Time Assembly (OFTA) of the TBM more than 7 km (4 mi) from the tunnel portal.
Image 3: Geology encountered in the Gerede tunnel included a mix of volcanic rock including tuff, basalt, and breccia, giving way to sedimentary formations like sandstone, shale, and limestone, all punctuated by fault zones that contained clay and alluvium.
Image 4: The Crossover TBM launched in summer 2016 and within the first 50 m (160 ft) of boring was able to pass through a difficult fault zone where one of the original, non-Robbins Double Shield TBMs was stuck.
Image 5: The Gerede Water Transmission Tunnel is considered by many to be the most difficult TBM-bored tunnel in Turkey.
Industry News, trenchless people
RICHMOND, VA – Matrix Capital Markets Group, Inc. (“Matrix”), a leading, independent investment bank, is pleased to announce the sale of Chesapeake, VA-based Tri-State Utilities Company (the “Company” or “Tri-State”) to Hoffman Southwest Corp. (“HSW”), a portfolio company of ORIX Capital Partners LLC (“ORIX”).
Founded in 1990 by Steve McSweeney, Tri-State is a leading, award-winning, regional provider of trenchless repair, rehabilitation, inspection, and other maintenance services to the municipal utility market. After nearly two decades of successfully providing technical services to support the maintenance needs of its customer base, Mr. McSweeney passed leadership of the Company’s operations to his two sons, Andy McSweeney and Joe McSweeney, in 2007. The change in leadership coincided with a period of rapid expansion for Tri-State, as the McSweeney brothers invested heavily in fleet and human capital in order to establish the Company as a market leader in trenchless utility rehabilitation throughout the Mid-Atlantic and Southeast. As a result of those investments, Tri-State maintains long-term sewer and stormwater contracts with an enviable list of blue-chip customers. Additionally, the Company has received recognition from its customers, vendors, and the broader industry for its exceptional safety credentials, technical expertise, increasingly diverse suite of services, and expanding geographic reach.
Andy McSweeney, President of Tri-State commented, “We are thrilled to be partnering with the HSW team to expand the breadth of services we’re able to offer our valued customer base. When Joe and I began contemplating a possible ownership transition, it was critical that we find a group that shared our Company’s values and commitment to growth. We feel confident that the HSW and ORIX teams are precisely the partners that share this vision.” Joe McSweeney, Chief Executive Officer of Tri-State added, “I have no doubt that HSW will help us build on the tremendous foundation that our father established and Andy and I were fortunate enough to continue. As shareholders in the combined entity, we are looking forward to personally maintaining the level of service and responsiveness that our customers and vendors have come to expect from Tri-State.”
HSW provides underground pipe inspection, trenchless pipe repair, excavation and cleaning services for municipal and utility customers.
Matrix served as exclusive financial advisor to Tri-State, which included valuation advisory, marketing the business through a confidential, structured sale process, and negotiation of the transaction. The transaction was led by David Shoulders, Managing Director and Head of Matrix’s Consumer & Industrial Products Group, and William O’Flaherty, Vice President. Robbie Nickle, Associate, and John Mosser, Analyst, also advised on the transaction. Regarding Matrix’s services, Andy McSweeney noted, “In the face of what could have been an exhausting and emotional process for Joe and I, the Matrix team was an unwavering source of support, providing professional and thoughtful guidance throughout the engagement. We can’t imagine getting this transaction done without their assistance, and we feel fortunate that we selected Matrix as our advisor.”
Mr. Shoulders added, “The McSweeney family has built an impressive business that is poised for exceptional growth as it continues to address the needs of aging underground infrastructure. We are pleased to have assisted them in identifying a partner that brings a strategic commitment to expansion, supportive capital to achieve the Company’s objectives, and the opportunity for Joe and Andy to remain with the business as both managers and shareholders.”
Troutman Sanders served as legal counsel for Tri-State.
About Matrix Capital Markets Group, Inc.
Founded in 1988, Matrix Capital Markets Group, Inc. is an independent, advisory focused, privately-held investment bank headquartered in Richmond, VA, with additional offices in Baltimore, MD, Chicago, IL, and Dallas, TX. Matrix provides merger & acquisition and financial advisory services for privately-held, private-equity owned, and publicly traded companies, including company sales, recapitalizations, corporate carve outs, corporate recovery, management buyouts, capital raises of debt & equity, corporate valuations, fairness opinions and business consulting. Matrix serves clients in a wide range of industries, including downstream energy, convenience retail, industrial products, building products, consumer products and business services. For additional information or to contact their team members, please visit www.matrixcmg.com.
Securities offered by MCMG Capital Advisors, Inc., an affiliate of Matrix Capital Markets Group, Inc., Member FINRA & SIPC.
Industry News, trenchless products
The team at Kobus Services Ltd, the UK based creators of the innovative Kobus Pipe Puller trenchless utility pipe repair and replacement system, has launched the new KPP400 excavator mounted pipe puller.
Pipe pulling removes the old pipework from the ground thereby eliminating the potential environmental pollution, as well as enabling the recycling and scrap value recovery of the old pipe.
The 400 Series Pipe Puller delivers a state-of-the-art solution for quickly and effectively removing and replacing service pipes.
The system requires two excavation holes, no larger than 3’ x 3’ depending on depth of service, to extract an old pipe while towing in the new replacement. Up to 85 feet of steel, copper, lead or plastic pipe can be easily replaced in a single pull (for diameters up to 1¼ in), and a new copper or PE pipe drawn in at the same time.
The 400 Series Pipe Puller is mounted on a compact excavator such as 35 or 45 series, and operates from the auxiliary hydraulics. It provides greater pulling power and efficiency improvements for contractors. The unique spool design makes removal of the pipe from the spool after extraction quicker and easier, while the rotatable foot means the puller can be positioned in any direction to suit excavator access.
The 400 Series Pipe Puller, already in use in five states in the Mid-West and being displayed for the first time at the No Dig Show in Chicago in 17-21 March 2019, can replace all types of service pipes, and combinations of pipe materials with fittings, much faster than more traditional methods. It is ideal for cross road applications and replacement programmes.
With several new features and capabilities, it has been designed in partnership with some of the UK’s leading utility companies, and will bring economic, logistical and business transforming benefits to contractors using it.
“In the United States, the problem is acute. It is estimated there are around 7 million lead pipes, totalling 65,000 miles of lead” says Simon Drain, Kobus Services managing director.
“In the US alone, with just one foot of lead pipe weighing 11 lbs and for an average 50 feet in length, this equates to an astronomical 3.8 billion lbs of lead. Aside the logistical and restoration benefits pipe pulling provides, the average scrap value of lead is approx. US$ 0.75 per lbs. Therefore, the potential scrap value of lead pipe to US contractors alone is worth $2.5 – 3bn”.
Visit https://us.kobuspipepuller.com/ to find out more or http://nodigshow.com/ to book to attend the show in Chicago and meet the Kobus team at booth 246.