Blog, trenchless people
We are proud to spotlight one of NASTT’s newest Student Chapters, University of Massachusetts Lowell! 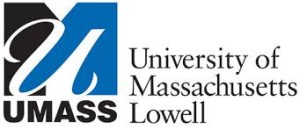
UMASS Lowell joined NASTT’s Student Chapters in the summer of 2016. The chapter membership is comprised of Civil Engineering students at the university.
The University of Massachusetts Lowell is an urban public research university located in the greater Boston area. UMass Lowell is the largest university in the Merrimack Valley and is committed to preparing students for work in the real world by providing affordable, high-quality education. Students and faculty in the Department of Civil and Environmental Engineering (CEE) are enthusiastic about actively engaging in trenchless activities and to promote learning. The CEE Department has long enjoyed a strong reputation of producing “work ready” engineers within the New England region. The CEE Department is widely known and it has 16 dedicated full-time faculty members who are committed to teaching, research, and community service. Students on this university campus are passionate and highly energetic.
The UMASS Lowell students would like to attend and contribute to the 2016 Northeast Trenchless Conference being held at the University Inn & Conference Center in collaboration with the University of Massachusetts Lowell. The tentative plan of the student chapter includes: Student participation in conferences, inviting leaders from the trenchless industry as guest speakers on specific topics, identifying trenchless projects and scheduling field visits to practice and experience trenchless methods and conducting trenchless research under the supervision of a faculty.
The NASTT student chapter at the University of Massachusetts Lowell will be advertised to students who have not yet had any experience with the trenchless technology and will encourage them to learn about the trenchless world.
Welcome to NASTT, UMASS Lowell! The North American Society for Trenchless Technology’s Student Chapters, working to build the future of trenchless!
Blog, Industry News, trenchless products
AURORA, IL- TT Technologies recently introduced a new cutterhead configuration for its Grundoburst static pipe
bursting system. The new configuration consists of three specially designed bladed, roller cutterheads in succession. The bladed roller cutting head configuration allows contractors to burst/split large diameter steel and ductile iron pipes when used with larger Grundoburst static bursting systems. The new special cutterhead design allows for a smoother host pipe cut and greater protection for the new pipe.
Pulled by a hydraulic bursting unit, the cutterhead’s special cutting wheels split the host pipe. An attached expander spreads and displaces the split pipe into the surrounding soil while simultaneously pulling in the new pipe. The Grundoburst system features Patented QuickLock bursting rods that are linked together not threaded. This saves time, prevents twisting and extends the life of the cutterhead over threaded bursting rods.
Blog, Industry News, trenchless people, trenchless products
September 20, 2016 – LAKE MILLS, Wisc. HammerHead Trenchless, a Charles Machine Works company, has announced the acquisition of RS Lining Systems, LLC, the provider of RS Technik® pipe rehabilitation solutions in the Americas. This acquisition will allow HammerHead to better serve customers across the underground infrastructure rehabilitation market by providing an enhanced suite of CIPP trenchless solutions.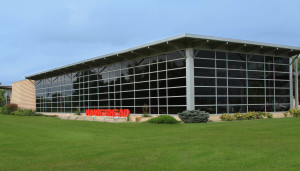
HammerHead Trenchless Equipment facilities in Lake Mills, Wisc.
“HammerHead strives to offer its customers a unique, comprehensive set of solutions for any rehabilitation or replacement project. The combination of HammerHead and RS Lining will expand our existing product and services offering to provide our customers the most complete set of solutions for rehabilitating underground utility infrastructure,” says Kevin Smith, President of HammerHead Trenchless Equipment. “Our goal is to offer customers not just any solution but the right solution to fit their needs, and the synergy between HammerHead and RS Technik solutions expands our position as the trusted advisor in the trenchless industry.”
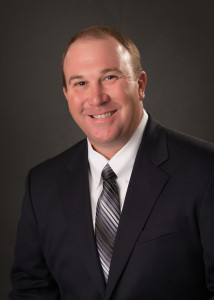
Kevin Smith, President of HammerHead Trenchless Equipment.
RS Lining is a leader in CIPP technology, providing a full suite of RS Technik pipe rehabilitation solutions for gravity sewer, pressure pipe and potable water including RS CityLiner®, RS CityMain®, and RS BlueLine® all of which feature mobile, state-of-the-art, CIPP impregnation and installation equipment RS MobiPreg™. RS Lining has engineered systems that provide unique solutions developed to meet the emergent needs of asset managers in performance, durability, and cost-effective sustainability of pipeline infrastructure.
“We are excited to add the talent and experience of the RS Lining team to our HammerHead family. The RS Lining team is made up of industry veterans with unique skills that will be valuable in the growth of HammerHead’s rehabilitation business segment and will give customers access to unparalleled expertise,” continues Smith. As part of the acquisition, the RS Lining team will be joining HammerHead at its facility in Lake Mills, Wisconsin.
“It is exciting for us to become part of the HammerHead team. HammerHead is an established leader in the industry and together we will usher in the next generation of trenchless solutions,” said RS Lining Senior Vice President Joanne Carroll. “RS Lining customers will continue to have access to the same RS Technik products now backed by the strength and support of HammerHead and the Charles Machine Works Family of Companies.”
“This union is a natural fit for the vision of HammerHead and Charles Machine Works. Both HammerHead and RS Lining are driven by providing effective and reliable solutions. Our customers now have access to every advantage possible for restoring gravity and pressure sewer, water and industrial pipe infrastructures,” said CEO of Charles Machine Works, Rick Johnson. “Their combined ability to deliver an inclusive range of innovative products aligns perfectly with Charles Machine Works vision.”
Blog, trenchless people
Written by Molly Gallagher, NASTT Membership Manager
We are proud to spotlight one of NASTT’s newest Student Chapters, Montana Tech!
Montana Tech joined NASTT’s Student Chapters in the summer of 2016. The chapter membership is for students
enrolled at Montana Tech at the University of Montana.
The NASTT Student Chapter at Montana Tech’s mission is to advance the science and practice of Trenchless Technology for the public benefit; to promote and participate in education, training, study, and research in said science and practice for the public benefit; and to make available information thereof to all interested and concerned parties.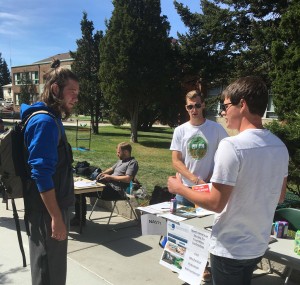
The Chapter held a Club Rush event on campus where they recruited new, interested members into the chapter. 18 students joined this semester! They have plans to visit two job-sites, hold a fundraiser, and get as many of their student members as possible to attend NASTT’s 2017 No-Dig Show in Washington, D.C.
Pictured are Zak Kypfer, chapter secretary, and John Grill, chapter president, talking with a fellow student during Club Rush.
Welcome to NASTT, Montana Tech! The North American Society for Trenchless Technology’s Student Chapters, working to build the future of trenchless!
Blog, Industry News, trenchless products
Vermeer VX30 Gen3 by McLaughlin packs innovative tools in compact footprint
GREENVILLE, S.C. — Building on the successful introduction of the VX50 Gen3, McLaughlin is introducing the next generation of its popular VX30, a vacuum excavator that is compact in size but offers the same power and productivity found in its predecessor. The introduction of the Vermeer VX30 Gen3 vacuum excavator built by McLaughlin brings new features, including automotive-style belt tensioners, quick-grip tool storage, quick-drain technology and more. The portable, versatile nature of this vacuum excavator makes it the ideal choice for utility contractors’ potholing and fluid management needs.
“The VX30 Gen3 vacuum excavator is a result of a design process driven by operator feedback,” said Jeff Wage, vice president at McLaughlin. “We are proud of the existing VX30 series, but the new generation shows we want to continuously grow and produce vacuum excavators that meet the needs of our customers.”
The new VX30 Gen 3 vacuum excavator is available with a no-hassle hose and strong arm option — an industry exclusive that allows crews to move quickly and easily between jobsites to create a more productive, ergonomic machine by eliminating the need to disconnect the suction hose. Additionally, the automatic belt tensioners on the blower and water pump rely on a proven design from the VX50 Gen3 to make service simpler and more efficient.
Additional key features:
• Gen3 chassis with high-clearance trailer with Dexter torsion axles
• Standard reverse pressure airflow for offloading fluids
• New high-lift version of the patented cam-over hydraulic rear door opens 40 percent higher than previous generations, allowing for easier access when cleaning the tank
• Quick-grip tool storage and tool box for one convenient place to store and access tools without the hassle of loose clips
• Remote service points for easy-to-access drains and grease points for curbside product daily servicing
The third-generation vacuum excavator is powered by a Tier 4 Final compliant 24.8 hp (18.5 kW) Kubota diesel engine with a common-rail fuel injection system. This four-cylinder, high torque engine requires no regeneration or DEF fluid, allowing for constant productivity without shutdown. Available in 300, 500 and 800 (1135.6 – 3028.3 L) spoil tank sizes and with the patented in-tank wash-down system — designed to remove debris and increase productivity —the VX30 Gen3 can be customized to the unique needs of cable, utility, fiber and rental markets.
The VX30 Gen3 includes the industry-exclusive three-stage cyclonic filtration system, a feature McLaughlin customers have come to rely on. The system allows for both wet and dry vacuum excavation while prolonging filter life and helping to keep maintenance costs low.
McLaughlin continues to provide the proven and patented cam-over hydraulic rear door, which provides a 360-degree positive seal, even under reverse pressure, without additional clamping requirements to keep fluids securely in the debris tank. No components are inside the tank, so all necessary maintenance is external.
For more information or to request an on-site demonstration of the new VX30 Gen3, contact your local Vermeer dealer, call McLaughlin at 1(800) 435-9340 or visit mclaughlinunderground.com.
For over 85 years, McLaughlin has been actively involved in the drilling tool industry. During that time McLaughlin has developed a reputation for designing and building dependable, low maintenance trenchless construction equipment. McLaughlin takes pride in providing solutions for OEMs and the underground industry.
© 2016 McLaughlin Group, Inc.
All Rights Reserved.
Please send all reader inquiries to: Please send all sales inquiries to:
McLaughlin Group, Inc. mmole@mightymole.com
2006 Perimeter Road
Greenville, SC 29605
Blog, Industry News, trenchless products
Allows users to see deeper targets and operate in noisy conditions
By Jeffrey Feigin, PhD, GSSI
Ground-penetrating radar (GPR) is an electromagnetic imaging technique that allows users to see beneath the
surface through soil, pavement, concrete, ice, and even water. GPR is widely used for utility mapping, concrete inspection, forensic investigations, geological surveys, and archaeology. Regulatory agencies place stringent power emission limits on GPR equipment to prevent disruption to other technologies that share the same spectra, for example, wireless communications and global positioning systems.
Now, new technology has been developed that meets even the most stringent GPR emissions regulations, including those of the U.S. Federal Communications Commission (FCC) and the European Telecommunications Standards Institute (ETSI), while operating at similar or faster speeds than conventional systems in difficult soil conditions. This new HyperStacking technique allows users to see deeper targets and operate in conditions considered too “noisy” for conventional systems.
Measuring signal variations caused by a buried object
GPR is an electromagnetic technology that uses the same kind of radio waves as microwave ovens, cellular phones, and broadcast radio and television. GPR systems operate under the same principle as other radar systems, medical ultrasound, and even fish finders. A GPR system includes an antenna, a power supply, and a control unit with electronics that trigger the pulse of radar energy the antenna sends into the subsurface. The antenna receives the electrical pulse produced by the control unit, amplifies it and transmits it into the ground or other medium at a particular frequency.
Subsurface variations will then cause these signals to bounce back. The strength and time required for the return of the reflected signals is then recorded on a computer integrated into the system. As the technician using the GPR equipment moves along the area being scanned, items detected are revealed and information is displayed on the computer screen in real time. The data collected is then analyzed and used to make specific recommendations.
For example, a GPR wave directed through the soil towards a piece of buried PVC pipe would reflect back some of the signal towards the surface. The magnitude and timing of this echo will be proportionate to the size and depth of the buried pipe. Since electromagnetic waves travel at the speed of light, if this pipe were buried at 3 feet (1 meter), a typical echo will occur just 20 nano-seconds (billionth of a second) after the signal is sent. This means that exceptionally fast receiver circuitry is required to correctly estimate the timing and scale of the signal.
Unfortunately, the standard signal observation methods are slow, particularly in certain soil conditions. The classic method for observing very fast events with relatively slow circuitry is to use a stroboscopic technique known as equivalent time sampling (ETS). This method requires multiple sampling acquisitions at different clock timing. The samples taken from each acquisition are put together and reconstructed. Multiple triggers are required to capture enough points to reconstruct the waveform. The technique is most useful when capturing repetitive signals. [1]
Like a camera flash, which can make a fast-moving object look frozen in time, electrical waveforms can also be captured at just one precise instant. By repeating the transmitted signal many times, but moving the exact instant of capture, one can simulate the echo response.
It can be likened to making a 100-frame motion picture of a bullet travelling through the air – but doing so by firing the gun 100 times and triggering the camera at a different time for each firing. Though stroboscopic techniques can be effective for capturing extremely fast-moving events, they are not the best or most efficient way.
Just as modern high-speed video cameras now exist for capturing a bullet in flight in real-time, we can now also capture an entire ultra-fast radar reflection the same way – by averaging (or stacking) the results of many individual GPR scans. Random environmental and electronic noise disappears through this averaging process, while weak targets emerge from the snow-like obscurity. Since high speed GPR systems recover identical radar scans hundreds of times faster than conventional ETS systems, this averaging operation goes on in the background and does not affect the rate of data collection.
HyperStacking technology
The technique is used in a new technology patented by GSSI [2], which greatly improves the receive performance of a GPR system while maintaining measurement speed and radiated emission limits. The new technology, known as “HyperStacking,” uses high speed interpolated sampling to reduce such commonly encountered issues as dynamic range limitations, regulatory compliance issues, sampler core offset error, and timing errors.
The benefits of the new HyperStacking technology are pronounced in lower frequency applications (GPR applications requiring an antenna below 1.6 GHz), such as in dirt, clay, sand, and more. In these conditions, the ground media is sufficiently lossy to make the benefits of HyperStacking clear. GSSI is developing its HyperStacking technology in a range of antenna frequencies to meet the specific needs of a variety of applications.
The 350 MHz antenna, for instance, is ideal for utility detection in soil conditions in the 0-15 ft range. Lower-frequency antennas, in to 100-200 MHz range, are well-suited for geotechnical applications, such as water table analysis, characterization of shallow stratigraphy, bedrock depth analysis, and analysis of deep geological structures. In these applications, traditional techniques such as ETS cannot achieve the same level of precision as HyperStacking.
With the commonly used ETS technique, hundreds or even thousands of pulses are transmitted to obtain a full measurement set over the desired time range. However, most of the received energy is discarded and the resultant measurement is inefficient, in terms of noise, relative to the amount of energy transmitted. By contrast, the new technology uses high speed interpolated sampling, which recovers all or most of the reflected radar information, greatly improving the measurement signal energy with respect to noise. In the past, these techniques have been expensive and far too energy-consuming, but recent advances in integrated circuit technology have enabled the development of low-cost devices that perform at reasonably high speeds while consuming relatively small amounts of power.
This more efficient signal detection directly translates to improved system performance in certain applications. Measurement results produced by the technique resolve targets at least 5 percent deeper and 5 percent smaller than conventional ETS GPR. The system can also produce individual measurement results at extremely high speeds – at least 1000x that of a conventional ETS system.
Figure 1 shows an example of a HyperStacked GPR measurement compared to a conventional ETS measurement. It shows that the HyperStacking system can see significantly more clearly and deeper than the conventional ETS system. Both are 400 MHz GPR systems and the measurements were taken at the same time and same location with identical processing. [Caption: Two GPR files taken at the same location at the same time with identical processing. left: HyperStacking, right: conventional (ETS)]
[1] Understanding Real Time and Equivalent Time Sampling, https://bkprecision.desk.com/customer/portal/articles/1535427-understanding-real-time-and-equivalent-time-sampling, retrieved 11/19/15.
[2] Realization of time-domain ultra wideband ground-penetrating radar using high speed accumulation and interpolated sampling, Patent EP 2698647 A1, http://www.google.com/patents/EP2698647A1?cl=en, retrieved 11/19/15