Industry News, trenchless projects
Join Deep Trekker for a free virtual conversation on Friday, June 26 from 10-11AM EDT.
FROM SEWER TO STORM TO CLEAN WATER PIPE INSPECTIONS
This week’s “Think Tank Friday” addresses robotic solutions for trenchless technology. Providing tools, techniques, and best practices, this panel gives you the inside scoop on optimizing your trenchless operations. Hear from maintenance operators, and software and asset management experts in this live, interactive conversation.
Visit Deep Trekker’s website to register.
Blog, Industry News, trenchless projects
Tough TBM breaks through after navigating Faults, Karst, and More
In January 2020, a Robbins 5.97 m (19.6 ft) diameter Main Beam TBM cleared its final hurdle when it broke through in Guangxi Province, China. The TBM excavated its first of two tunnels, an 11.9 km (7.4 mi) long conduit for Lot 1 of the North Line Water Irrigation Project, Letan Water Reservoir, Drought-Relief. The tunnel was marked by a gauntlet of challenges, from karst cavities to fault zones and water inflows. The workers on the jobsite, contractor Guangdong No. 2 Hydropower Bureau Co., Ltd., and the owner, Construction Management Bureau for the Letan Water Reservoir, had much to celebrate after completion of what is widely regarded as the most complex and longest tunnel on the North Line project.
Boring with the Robbins Main Beam TBM and continuous conveyor system began in summer 2015. “There was no precedent in this province for using a Main Beam TBM to excavate a tunnel longer than 10 km. We didn’t have relevant local experience to use for reference,” explained Yongjiu Jin, Deputy Manager of the Project for contractor Guangdong No. 2 Hydropower Bureau Co., Ltd. The machine did encounter a number of difficult geological obstacles as it bored through limestone rock, but was still able to achieve advance rates up to 40 m (130 ft) per day in good ground.
Much of the geology consisted of lightly weathered limestone in rock class II to III, with some sections in class IV to V rock that required the heaviest amount of ground support, ranging from rock bolts to ring beams and mesh. “Our team encountered a coal seam, gasses in the tunnel, two large water inrushes, three fault zones up to 103 m long, 11 karst cavities, and more. In order to solve the ground problems, there were more than 160 special technical research meetings held,” said Yongjiu.
Throughout tunneling, the contractor expressed thanks for Robbins Field Service staff. “Robbins personnel provided good technical support from equipment installation and commissioning through to tunnel completion. After the equipment was handed over to our company, they still helped us with equipment usage on our project, which makes us very satisfied with the Robbins after-sales service. Robbins really delivered: the after-sales phase was not the end of service, but the beginning of site service,” said Yongjiu.
While the completion of the first tunnel—the longest single-heading construction on record for water tunnels in Guangxi—is a milestone, there is more to do. The Robbins machine will be inspected and relaunched to bore a second tunnel 4.2 km (2.6 mi) in length. The ground conditions are predicted to be equally challenging, but the tunneling operation has some help from ground prediction methodology. Tunnel Reflection Tomography (TRT)—consisting of ground prediction using seismic waves—is being used to detect changing conditions ahead of the TBM. The method can predict the distribution and scale of joints and fissures, allowing the crew to plan ahead.
Located near Laibin City, the North Line project provides much needed drought relief using a network of tunnels totaling 29.4 km (18.3 mi). “This tunnel will realize the dream of drought control that people in Central Guangxi have had for many years. The breakthrough is the most important milestone event in this first phase of the North Line project,” said Yongjiu.
Image 1: Contractor Guangdong No. 2 Hydropower Bureau Co., Ltd., the project owner, and Robbins celebrate the January breakthrough of a Robbins Main Beam TBM.
Image 2: The 5.97 m (19.6 ft) Robbins TBM traversed fault zones, karst cavities, a coal seam, and more while achieving up to 40 m (130 ft) in one day.
Image 3: Robbins Field Service and Engineering staff played an important role in the project’s overall success. They advised the contractor and gave after-sales support throughout the difficult ground conditions.
Image 4: The Robbins Main Beam TBM bored through limestone rock, and installed a full range of ground support, from rock bolts to ring beams and wire mesh.
Industry News, trenchless projects
Barbco, Inc. Co-Owner and CEO, Anthony R. Barbera was granted U.S. Patent #10465460 for the Barbco FlexBor tooling and technology on November 5, 2019. This is a proud moment in this East Canton, Ohio manufacturer’s storied 30-year history of driving the trenchless technology, horizontal boring, and underground manufacturing industries forward with world class capital equipment and cutting-edge technology. The FlexBor is an extremely cost-effective, environmentally safe trenchless method and tooling. The FlexBor is designed to virtually eliminate “frac-outs” / ”inadvertent returns” that are often associated with horizontal directional drilling and the use of bentonite.
The Patent Abstract reads: “A cutting assembly and method for drilling an underground borehole. The cutting assembly includes front and rear cutting heads of different diameters mounted on a shaft. An air passage defined through the cutting assembly may be placed in fluid communication with a pressurized remote air source and with a bore of a casing extending rearwardly from the cutting assembly. Pressurized air flows through the air passage and entrains cuttings produced by the front and rear cutting heads. A housing extends rearwardly from the larger diameter rear cutting head and an auger provided within the housing aids in directing cuttings into the casing. The auger rotates independently of the rest of the cutting assembly and may be configured to further reduce the size of the cuttings. A collar on the housing seals the borehole cut by the rear cutting assembly and aids in preventing frac-out.”
For more information on Barbco’s products and services, visit their website.
Industry News, trenchless people, trenchless products, trenchless projects
In the trenchless excavation, horizontal directional drilling, and underground manufacturing industries, one family stands out as leaders in this close-knit community: The Barberas. Family Patriarch, James S. Barbera founded Barbco, Incorporated, a world class capital equipment manufacturer in these industries. In fact, his status is so renown and legendary, that in April, he will be posthumously inducted as a member of the Class of 2020 into the North America Society for Trenchless Technology’s Hall of Fame, joining a very elite and highly esteemed society of industry ground breakers. James S. Barbera has passed the torch onto his three sons, Anthony, David, and James A., who now own the family business, Barbco. The Barbera clan continues to drive the industry forward and now have brought the third generation of the family into this exciting field.
On January 2nd, grandsons Drake Barbera (son of Anthony) and James V. Barbera (son of James A.) along with co-owner Clay Gillian successfully completed their very first horizontal bore with their new company AccuLine Underground at an urban work site in Metuchen, New Jersey. AccuLine partnered with project General Contractor J. Fletcher Creamer & Son, Inc. to complete a 250 foot long crossing that was at a depth of 20 feet under the length of a busy city road skillfully avoiding numerous very critical city main utilities. To say that this 3,000 man hour project was challenging is a complete understatement.
The AccuLine team’s years of experience and deep knowledge of the industry was readily apparent before the first shovelful of dirt was removed from the job site. In his initial meeting with the job owners, Drake made a strong and convincing counter-proposal to the microtunneling option with his recommended approach using a conventional auger boring machine pushing a BMTA (boring machine tunnel attachment). Drake’s proposal proved to the winning combination, securing AccuLine this very prestigious and highly visible contract.
The crew faced numerous job site challenges ranging from old and forgotten infrastructure to rocky and sandy soils. Their expertise allowed them to make on site equipment modifications and adjustments coupled with some new to the field innovations to keep the job on line and on grade, dramatically saving the job owners both time and money. This highly successful initial foray into the Barbera family business as proven that the third generation of Barberas and their company, AccuLine Underground is a force to be reckoned with! Grandfather Barbera must be very proudly watching over his progeny!
Industry News, trenchless products, trenchless projects
Adaptable machine will begin bore at 11.6 m then size down to 9.9 m
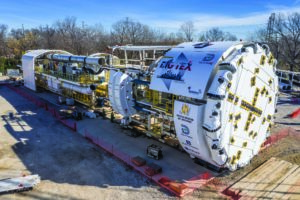
In December 2019, the City of Dallas, Texas, USA unveiled the largest hard rock TBM ever to bore in the U.S. The 11.6 m (38.1 ft) diameter Robbins Main Beam TBM will excavate the 8 km (5 mi) Mill Creek Drainage Relief tunnel, and its size is not its only distinction. The adaptable machine will change size partway through the bore, to a more compact 9.9 m (32.5 ft).
The unique Robbins TBM will be used to dig a tunnel designed to provide 100-year flood protection for east and southeast Dallas, areas affected in recent years by severe storms. The tunnel will protect 2,200 commercial and residential properties, including Baylor Medical Center. The current drainage system in these areas was constructed 50 to 70 years ago, and only provides two to five years of flood protection. “The completion of the TBM assembly marks a major milestone in the Mill Creek Tunnel Project,” said Council Member Lee Kleinman, chair of the Transportation and Infrastructure Committee for the City of Dallas. “I’m thrilled to see this type of engineering marvel happening right here in Dallas.”
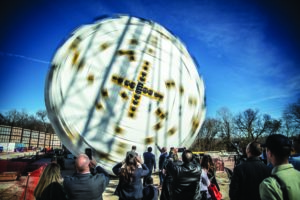
The dual-diameter aspect of the Robbins TBM will be a first-of-its-kind conversion process. The contractor, Southland/Mole Joint Venture (SMJV), will make the conversion underground about 2.8 km (1.8 mi) into the bore. The two diameters are needed as the upstream section of the tunnel is designed with a circular cross section and peak flow rate of 42 m3/sec (15,000 ft3/sec), while the downstream 2.8 km (1.8 mi) portion has a higher peak flow of 565 m3/sec (20,000 ft3/sec) and was initially designed as a horseshoe cross section. Using the TBM for the entire tunnel is less time consuming and costly. “Robbins and SMJV are working closely to create the safest and most efficient sequence for completing this conversion within the limits of the bore. The City of Dallas (Owner) and our Project Team are very excited to embark on this unique challenge,” said Nick Jencopale, Project Manager for Southland Holdings.
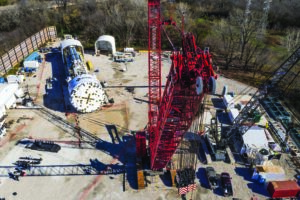
The Robbins TBM, named “Big Tex” with permission of the State Fair of Texas, has been designed with a specialized cutterhead including removable spacers and adjustable bucket lips to convert to a smaller diameter. The TBM will first complete its 11.6 m (38.1 ft) diameter section of the alignment, then back up about 21 m (75 ft) to a transition area for the conversion, which is expected to take six to eight weeks.
As the TBM bores, it will pass through Austin Chalk between 12 to 30 MPa (1,800 to 4,400 at depths from 31 to 46 m (100 to 150 ft) below the city. The route is potentially gassy, so probe drilling is mandatory throughout the project. Crews will utilize ground support including eight 3.9 m (13 ft) long rock bolts every 1.5m (5 ft) with wire mesh and channel straps as needed. The finished tunnel will be lined with a 380 mm (15 in) thick cast-in-place concrete lining.
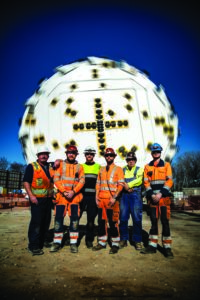
“Big Tex will work 24 hours a day to excavate the tunnel with crews ranging in size depending on activities,” said Rachel Sackett, marketing and communications director for Southland Holdings. Based on previous work through similar geology, the project team expects TBM excavation to progress rapidly to an average of 25m (80 ft) per day, allowing the project to be completed on schedule in 2023.
Image 1: The 11.6 m (38.1 ft) Robbins Main Beam TBM is the largest hard rock TBM ever to be used in the U.S.
Image 2: A ceremony was held in December 2019 to mark the impending launch of the unique Robbins TBM, which will undergo a first-of-its-kind diameter conversion approximately 2.8 km (1.8 mi) into the bore.
Image 3: The 8 km (5 mi) Mill Creek Drainage Relief tunnel will provide 100-year flood protection for east and southeast Dallas, areas affected in recent years by severe storms.
Image 4: The adaptable Robbins machine will change size partway through the bore, to a more compact 9.9 m (32.5 ft).
Photos by Shannon Faulk
For more information/questions please contact:
Desiree Willis
Technical Writer
Email: willisd@robbinstbm.com
Direct: 253.872.4490
The Robbins Company
29100 Hall Street
Solon, OH 44139
USA
Industry News, trenchless products, trenchless projects
40 Years after Original Tunnel, Robbins Returns to Russia
In 1979, a 4.56 m diameter Robbins Double Shield TBM was delivered to bore the Severomuysky Service Tunnel, a 15.3 km long railway through the remote mountains of Siberia. Now, 40 years after the original machine was delivered, Robbins is returning to the role. Two 10.37 m diameter Crossover (XRE) TBMs will bore the second Severomuysky Tunnel, clocking in at 15.5 km long and running through mixed ground and fault zones. The new rail line is needed due to limitations on carrying capacity on the current Baikal-Amur Mainline (BAM) railway through the area. Currently 16 million tonnes of cargo are carried through the existing Severomuysky tunnel but the Russian Government wants to increase cargo carrying capacity by more than six times in the region.
The largest global anthracite producer, Sibanthracite Group, is taking on the tunnel construction with management by VostokCoal Management Company. The companies, owned by Dmitry Bosov, aim to increase coal transport by up to 100 million tonnes per year through the addition of the second tunnel. “Robbins has established itself on the market as the best manufacturer of hard rock machines, which are able to provide the maximum penetration rate in hard rock. This is one of the determining factors in connection with the tight deadlines for the implementation of our project. Also, Robbins is the only manufacturer to build the Crossover TBM,” said a representative of Sibanthracite Group. Other aspects of the supply include a continuous conveyor for muck removal, rolling stock, spare parts, and cutting tools.
Sibanthracite Group chose Crossover technology for a number of reasons, geology being chief among them. “A Crossover type tunnel boring machine was selected for tunneling due to the fact that the construction of the tunnel will be carried out in difficult heterogeneous geological conditions (from unstable waterlogged soils to hard rock). The Crossover is able to operate in two modes: Open mode, used while boring in hard rock formations, and closed mode (with earth pressure balance), used when boring in unstable water-logged soils,” said the Sibanthracite representative.
The lessons learned during the first Severomuysky tunnel—the importance of probe drilling, consolidation grouting, and preventing a shielded machine from becoming stuck in fault zones or squeezing ground—are all part of the Crossover TBM solution. “I was a young engineer working at Robbins when the Double Shield TBM was delivered for the first tunnel, so it is a special honor to bring this new technology to the second Severomuysky Tunnel in Siberia,” said Robbins President Lok Home. “Per the contract Robbins is supplying Crossover TBMs for the new parallel rail tunnel—these machines are made to bore in highly variable ground conditions while maintaining good advance rates. With our latest technology we hope to again prove TBMs are the better choice over Drill and Blast when difficult ground conditions are to be encountered.”
The machines will be designed for varying water pressures, ranging from 5 to 20 bar. They will feature Water Inflow Control, a system that seals off the face and periphery and creates a safe working environment in which to dewater and consolidate ground. The machines will feature probe drill ports and capabilities for 360-degree probe drilling and grouting ahead of the excavation face, while the Robbins Torque-Shift System will enable the machines to bore through collapsing ground and other situations that demand high torque. The machines will also be designed with a belt conveyor in hard rock mode that can be switched out with a screw conveyor when crossing into soft ground.
Crews will bore through the Severomuysky Ridge, a mountain range in Buryatia and part of the Stanovoy Highlands, which separates the basins of the Upper Angara and Muya Rivers. “The second Severomuysky tunnel is located in one of the most geologically active areas of our planet—on the north-eastern flank of the Baikal rift zone. The region is characterized by high seismic activity, difficult geological and hydrogeological conditions against the backdrop of a harsh climate (the summer period lasts only 80-100 days, temperatures from + 39°C in summer to -58°C in winter). The construction work on the portals is complicated by the presence of permafrost as well,” said the Sibanthracite representative. Construction of the new tunnel is expected to begin in 2020 and take five years.
Image 1: The original 4.56 m diameter Double Shield machine was supplied for the Severomuysky Service Tunnel in 1979.
Image 2: The new 10.37 m Robbins Crossover (XRE) TBMs are designed for highly variable geology and will have a belt conveyor that can be switched out with a screw conveyor in challenging conditions.